Спекание - важнейший процесс в материаловедении, особенно в производстве керамики и металлов, при котором порошкообразные материалы нагреваются до образования твердой массы без плавления.Физические свойства спеченных материалов зависят от различных факторов, таких как температура, давление, размер частиц и состав материалов.Эти факторы влияют на микроструктуру, пористость и механические свойства конечного продукта.Понимание этих свойств необходимо для оптимизации процесса спекания с целью достижения желаемых характеристик материала.
Объяснение ключевых моментов:
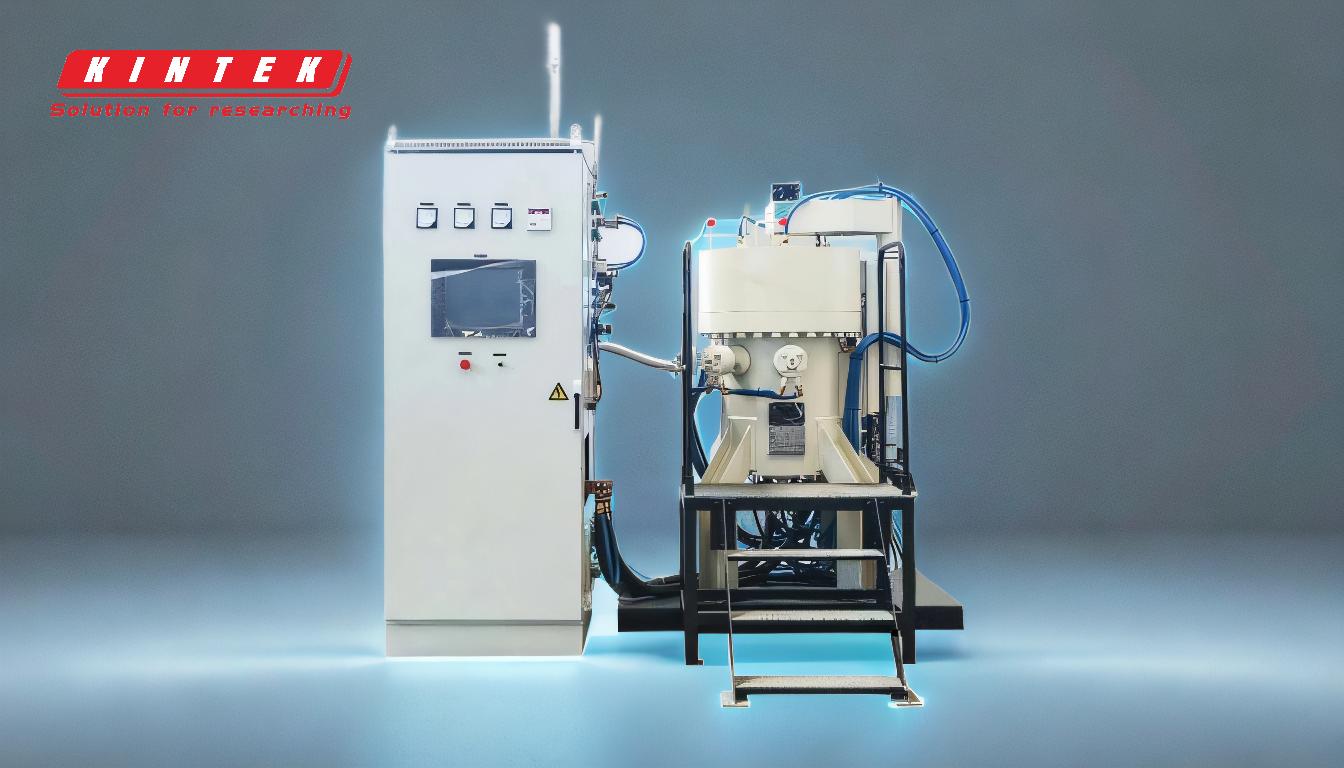
-
Микроструктурный состав:
- Микроструктура спеченных материалов обычно включает такие фазы, как гематит, магнетит и феррит кальция.
- Эволюция этих фаз в процессе спекания зависит от основности смеси для спекания, что влияет на свойства конечного продукта.
-
Влияние переменных спекания:
- Атмосфера:Атмосфера спекания (воздух, вакуум или инертные газы, такие как аргон/азот) может существенно повлиять на свойства спеченного материала.
- Температура:Более высокие температуры спекания обычно увеличивают прочность на растяжение, усталостную прочность при изгибе и энергию удара.
- Скорость охлаждения:Скорость охлаждения спеченного материала также может повлиять на его конечные свойства.
-
Техника и параметры:
- Различные методы спекания зависят от использования электрических токов, давления, источников тепла и конкретных спекаемых материалов.
- Такие параметры, как температура спекания, приложенное давление, средний размер зерна и газовая атмосфера, имеют решающее значение для оптимизации процесса спекания.
-
Пористость и плотность:
- Конечная пористость спеченной керамики зависит от начальной пористости зеленого компакта, а также от температуры и продолжительности процесса спекания.
- Применение давления во время спекания может уменьшить пористость и время спекания, особенно для чисто оксидной керамики, которая требует более длительного времени спекания и более высоких температур из-за диффузии частиц в твердом состоянии.
-
Управление процессом:
- В процессе спекания контролируются такие факторы, как объем воздуха, вакуум, толщина слоя, скорость и конечная точка спекания.
- Например, объем воздуха обычно составляет 3200 м³ на тонну спекаемой руды, а площадь спекания рассчитывается как 70-90 м³/(см²-мин).
-
Свойства материала:
- Область связывания, связанная с размером частиц, имеет решающее значение для определения таких свойств, как прочность и проводимость.
- Контролируемые переменные, такие как температура и начальный размер зерна, играют важную роль, поскольку давление пара зависит от температуры.
-
Кинетика спекания:
- Температура определяет кинетику спекания и свойства материала.
- Скорость нагрева влияет на уплотнение, причем более высокая скорость нагрева потенциально приводит к лучшему уплотнению.
-
Размер и состав частиц:
- Более мелкие частицы и однородный состав способствуют лучшему уплотнению при спекании.
- Состав материала также влияет на поведение при спекании, причем для разных материалов требуются индивидуальные условия спекания.
Понимание этих ключевых моментов помогает разрабатывать процессы спекания, которые позволяют получать материалы с желаемыми физическими свойствами, обеспечивающими оптимальные характеристики при их применении по назначению.
Сводная таблица:
Фактор | Влияние на спеченные материалы |
---|---|
Температура | Повышение температуры увеличивает прочность на разрыв, усталостную прочность при изгибе и энергию удара. |
Атмосфера | Воздух, вакуум или инертные газы (аргон/азот) влияют на свойства материала. |
Скорость охлаждения | Влияет на конечные свойства; контролируемое охлаждение обеспечивает желаемую микроструктуру. |
Размер частиц | Более мелкие частицы улучшают плотность и повышают прочность материала. |
Состав | Однородные составы и специально подобранные условия оптимизируют процесс спекания. |
Давление | Уменьшает пористость и время спекания, особенно для оксидной керамики. |
Скорость нагрева | Более высокая скорость нагрева может привести к лучшему уплотнению. |
Оптимизируйте процесс спекания с помощью экспертного руководства. свяжитесь с нами сегодня !