Лазерное спекание - это разновидность технологии аддитивного производства (3D-печати), в которой используется мощный лазер для сплавления порошкообразного материала в твердую структуру.Она широко используется в таких отраслях, как аэрокосмическая, автомобильная и медицинская, для создания сложных высокоточных деталей.Процесс включает в себя наслоение порошкообразного материала и выборочное спекание его с помощью лазера для создания желаемого объекта слой за слоем.Этот метод особенно выгоден для производства деталей со сложной геометрией, высокой прочностью и отличной отделкой поверхности.Кроме того, он энергоэффективен и экономичен, поскольку сводит к минимуму отходы материалов и позволяет использовать материалы с высокой температурой плавления, не расплавляя их полностью.
Объяснение ключевых моментов:
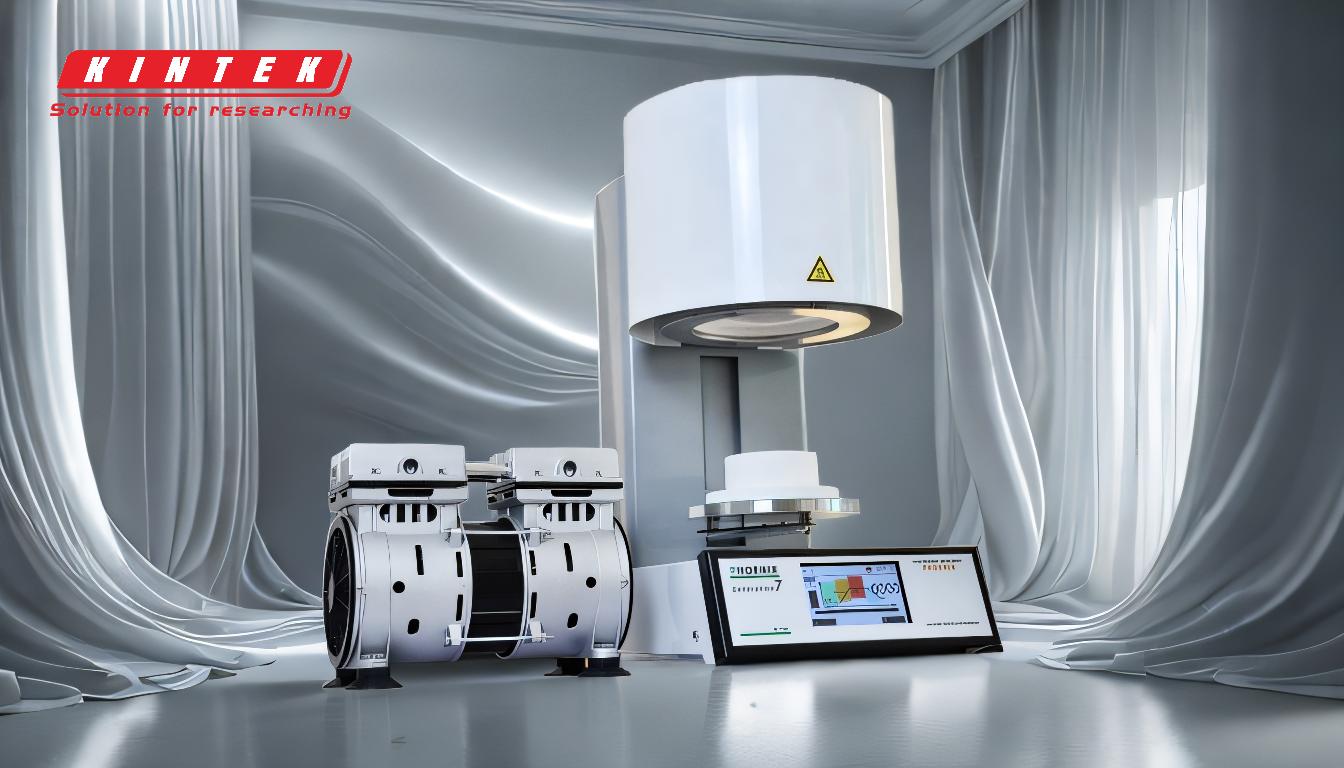
-
Определение лазерного спекания:
- Лазерное спекание - это процесс аддитивного производства, в котором используется лазер для сплавления порошкообразного материала в твердую структуру.
- Это послойный процесс, в котором каждый слой порошка выборочно спекается для создания конечного 3D-объекта.
-
Материалы, используемые при лазерном спекании:
- К распространенным материалам относятся металлы (например, титан, алюминий, нержавеющая сталь), полимеры (например, нейлон, полиамид) и керамика.
- Выбор материала зависит от желаемых свойств конечной детали, таких как прочность, долговечность и термостойкость.
-
Обзор процесса:
- Шаг 1: Подготовка:3D-модель детали создается с помощью программного обеспечения CAD и нарезается на тонкие слои.
- Шаг 2: Осаждение порошка:Тонкий слой порошкообразного материала равномерно распределяется по платформе для сборки.
- Шаг 3: Лазерное спекание:Мощный лазер сканирует слой порошка, выборочно спекая его в соответствии с дизайном 3D-модели.
- Шаг 4: Добавление слоев:Платформа для сборки опускается, и новый слой порошка наносится на предыдущий слой.Процесс повторяется до тех пор, пока деталь не будет готова.
- Шаг 5: Постобработка:После изготовления детали она может подвергаться дополнительным процессам, таким как охлаждение, очистка и обработка поверхности.
-
Преимущества лазерного спекания:
- Сохранение материалов:Лазерное спекание минимизирует отходы материала, так как спекается только необходимый порошок.
- Энергоэффективность:Процесс требует меньше энергии по сравнению с традиционными методами производства, так как не предполагает расплавления всего материала.
- Экономическая эффективность:Сокращение отходов материалов и энергопотребления ведет к снижению производственных затрат.
- Гибкость конструкции:Лазерное спекание позволяет создавать сложные геометрические формы и замысловатые конструкции, которые было бы трудно или невозможно достичь традиционными методами.
- Высокая точность и согласованность:Этот процесс обеспечивает превосходный контроль над процессом спекания, в результате чего получаются детали с высокой точностью размеров и стабильным качеством.
- Улучшенные свойства материала:Спеченные детали часто демонстрируют улучшенные механические свойства, такие как повышенная прочность и твердость, благодаря контролируемому процессу спекания.
-
Области применения лазерного спекания:
- Аэрокосмическая промышленность:Используется для производства легких и высокопрочных компонентов, таких как лопатки турбин и структурные детали.
- Автомобильная промышленность:Применяется в производстве деталей на заказ, прототипов и сложных компонентов, таких как детали двигателей и кронштейны.
- Здравоохранение:Используется для создания имплантатов, протезов и хирургических инструментов с высокой точностью.
- Товары народного потребления:Используется в производстве ювелирных изделий, очков и других потребительских товаров с замысловатым дизайном.
-
Проблемы и соображения:
- Материальные ограничения:Не все материалы подходят для лазерного спекания, для некоторых могут потребоваться специализированные порошки или последующая обработка.
- Обработка поверхности:Лазерное спекание позволяет получать детали с хорошей чистотой поверхности, однако для задач, требующих сверхгладких поверхностей, может потребоваться дополнительная постобработка.
- Стоимость оборудования:Первоначальные инвестиции в оборудование для лазерного спекания могут быть высокими, что может стать препятствием для мелких производителей.
- Контроль процесса:Достижение стабильных результатов требует точного контроля таких параметров, как мощность лазера, скорость сканирования и толщина слоя порошка.
В целом, лазерное спекание - это универсальный и эффективный метод аддитивного производства, который обладает множеством преимуществ, включая экономию материалов, энергоэффективность и возможность изготовления сложных высокоточных деталей.Несмотря на некоторые сложности, он широко используется в различных отраслях промышленности благодаря своей способности создавать прочные, высококачественные компоненты с минимальным количеством отходов.
Сводная таблица:
Аспект | Подробности |
---|---|
Определение | Аддитивное производство с использованием лазера для послойного сплавления порошкообразного материала. |
Материалы | Металлы (титан, алюминий), полимеры (нейлон), керамика. |
Этапы процесса | Подготовка, осаждение порошка, лазерное спекание, добавление слоев, постобработка. |
Преимущества | Экономия материалов, энергоэффективность, экономичность, гибкость конструкции, высокая точность. |
Области применения | Аэрокосмическая промышленность, автомобилестроение, здравоохранение, потребительские товары. |
Проблемы | Ограничения по материалу, качество поверхности, стоимость оборудования, контроль процесса. |
Готовы узнать, как лазерное спекание может улучшить ваш производственный процесс? Свяжитесь с нами сегодня чтобы узнать больше!