Историческое развитие технологии вакуумных покрытий
Ранние проблемы и технология CVD
Технология вакуумных покрытий сделала первые значительные шаги в 1960-х годах с появлением химического осаждения из паровой фазы (CVD). Эта новаторская технология, хотя и была революционной в то время, не обошлась без проблем. Одним из наиболее серьезных препятствий было требование высоких температур, что ограничивало типы подложек, на которые можно было эффективно наносить покрытия. Высокие температурные требования CVD-процессов означали, что только материалы с высокой термической стабильностью могли выдержать условия осаждения, что значительно сужало область потенциальных применений.
Кроме того, ранние CVD-технологии были ограничены разнообразием покрытий, которые они могли создавать. Сложность и специфичность химических реакций, протекающих в CVD, означала, что надежное осаждение возможно лишь для небольшого числа материалов, что еще больше ограничивало возможности ее применения. Эти ограничения создали значительные трудности для развития и широкого распространения технологии вакуумного нанесения покрытий, что привело к необходимости поиска альтернативных методов, способных преодолеть эти барьеры.
В последующие десятилетия эти ранние проблемы проложили путь к разработке более универсальных и эффективных технологий нанесения покрытий, таких как физическое осаждение из паровой фазы (PVD), появившееся в 1970-х годах и предложившее более адаптируемое и экологически безопасное решение.
Появление технологии PVD
К 1970-м годам ландшафт вакуумных технологий нанесения покрытий претерпел значительные изменения с появлением технологии физического осаждения паров (PVD). Этот новый метод не только решил некоторые экологические проблемы, связанные с его предшественником, химическим осаждением из паровой фазы (CVD), но и позволил получить множество универсальных свойств поверхности, которые ранее были недостижимы. Переход от CVD к PVD ознаменовался снижением рабочих температур и расширением спектра наносимых покрытий, что расширило сферу его применения в различных отраслях промышленности.
Особого внимания заслуживают экологические преимущества PVD. В отличие от CVD, где часто требовались высокие температуры и потенциально опасные химикаты, PVD работает в более контролируемых условиях, что приводит к снижению потребления энергии и уменьшению выбросов. Такая экологичность в сочетании со способностью создавать покрытия с превосходной твердостью, износостойкостью и защитой от коррозии быстро привлекла внимание исследователей и промышленников.
Быстрое развитие технологии PVD в этот период можно объяснить ее адаптивностью и значительным улучшением качества и долговечности покрытий. Отрасли промышленности, от автомобильной до аэрокосмической, начали применять PVD благодаря его способности улучшать характеристики инструментов и компонентов, что привело к повышению эффективности и увеличению срока службы изделий. Такое широкое распространение способствовало дальнейшему совершенствованию методов PVD, двигая технологию вперед и укрепляя ее место в сфере современных промышленных процессов.
Текущее состояние и проблемы
Несбалансированное развитие
Несмотря на широкое распространение технологии вакуумного нанесения покрытий в декоративных целях, применение этих покрытий в промышленном производстве пресс-форм по-прежнему сопряжено с трудностями. Основное препятствие заключается в жестких требованиях к адгезии, предъявляемых промышленными пресс-формами, которые требуют более прочного и долговечного соединения между покрытием и основой. Эти повышенные требования нелегко удовлетворить с помощью существующих технологий нанесения покрытий, которые зачастую отдают предпочтение эстетической привлекательности перед функциональной долговечностью.
Более того, отсутствие комплексных технологий, специально разработанных для нанесения покрытий на промышленные пресс-формы, еще больше усугубляет эти проблемы. В отличие от декоративных покрытий, которые могут позволить себе менее строгие методы нанесения, покрытия для промышленных форм требуют точных и контролируемых процессов для обеспечения оптимальных характеристик и долговечности. Такое несоответствие в технологическом развитии привело к несбалансированному росту в отрасли вакуумных покрытий, где достижения в области декоративных покрытий не нашли адекватного отражения в промышленном применении.
Для решения этих проблем существует острая необходимость в разработке специализированных технологий и методик, способных удовлетворить уникальные требования к нанесению покрытий на промышленные формы. Это включает в себя не только улучшение адгезионных свойств покрытий, но и совершенствование всей технологической цепочки, от предварительной обработки до контроля качества после нанесения. Сосредоточившись на этих направлениях, отрасль сможет преодолеть разрыв между декоративными и промышленными покрытиями, способствуя более сбалансированному и комплексному развитию.
Технические различия
В сфере вакуумных технологий нанесения покрытий, особенно в контексте PVD (Physical Vapor Deposition), отечественные технические возможности часто отстают от международных стандартов. Это несоответствие касается не только сложности оборудования, но и более широкого спектра факторов, включая оптимизацию процессов, достижения в области материаловедения и методологии контроля качества.
Чтобы преодолеть этот разрыв, отечественной промышленности необходимо не только внедрять передовое оборудование, но и осваивать и интегрировать новейшие технологии. Это предполагает многосторонний подход, включающий в себя:
- модернизацию оборудования: Инвестиции в современные вакуумные камеры, источники питания и системы подачи газа, способные с высокой точностью выполнять сложные процессы PVD.
- Поглощение технологий: Участие в совместных исследованиях и разработках с международными партнерами для понимания и внедрения передового опыта в технологии PVD.
- Оптимизация процессов: Совершенствование существующих процессов для обеспечения однородности качества покрытия, решение таких вопросов, как адгезия и однородность слоя.
Аспект | Отечественный статус | Международные стандарты |
---|---|---|
Оборудование | Базовое или устаревшее | Современное и высокоточное |
Управление процессом | Ручное или полуавтоматическое | Полностью автоматизированное с поддержкой искусственного интеллекта |
Материаловедение | Ограниченный исследовательский фокус | Широкие исследования и инновации |
Контроль качества | Специальные методы | Систематический и строгий FQC |
Путь к паритету включает в себя не только приобретение технологий, но и создание надежной экосистемы, поддерживающей постоянные инновации и улучшения. Такой комплексный подход необходим для повышения отечественного потенциала и обеспечения его конкурентоспособности на мировом уровне.
Основные понятия и характеристики PVD-покрытия
Методы и технологии
Физическое осаждение из паровой фазы (PVD) включает в себя несколько передовых методов, каждый из которых обладает уникальными характеристиками и областью применения. Два основных метода PVD - это многодуговое осаждение и магнетронное распыление.
Многодуговое осаждение включает в себя испарение целевого материала с помощью электрической дуги, которая ионизирует материал и направляет его на подложку. Этот метод известен высокой скоростью осаждения и способностью наносить покрытия сложной геометрии. Однако он может страдать от таких проблем, как загрязнение частицами и неравномерная толщина покрытия.
С другой стороны, при магнетронном распылении используется магнитное поле для усиления ионизации атомов мишени, которые затем ускоряются по направлению к подложке. Эта технология позволяет лучше контролировать свойства покрытия, включая плотность и однородность, что делает ее идеальной для приложений, требующих точных покрытий. Несмотря на эти преимущества, магнетронное распыление может быть более медленным и энергоемким по сравнению с многодуговым гальваническим покрытием.
Метод | Преимущества | Недостатки |
---|---|---|
Многодуговое нанесение покрытия | Высокая скорость осаждения, подходит для сложных геометрий | Загрязнение частицами, неравномерная толщина покрытия |
Магнетронное напыление | Отличный контроль над свойствами покрытия, высокая плотность и однородность | Более медленный процесс, высокое энергопотребление |
Понимание этих методов и их соответствующих плюсов и минусов имеет решающее значение для выбора наиболее подходящей технологии PVD для конкретных промышленных применений.
Комбинация технологий
Объединение многодуговых и магнетронных технологий представляет собой значительное достижение в области вакуумного нанесения покрытий. Эта комбинация - не просто сумма частей, а синергетический подход, который максимально использует преимущества обеих технологий, обеспечивая производство стабильных и высококачественных покрытий.
Многодуговая гальваника, известная своими высокими скоростями осаждения и способностью создавать плотные покрытия, дополняет магнетронное распыление, которое позволяет получать однородные и конформные покрытия при минимальном нагреве подложки. Комбинируя эти методы, производители могут достичь баланса между скоростью осаждения и однородностью покрытия, что очень важно для приложений, требующих одновременно эффективности и точности.
Кроме того, гибридизация этих технологий позволяет оптимизировать свойства покрытия. Например, включение многодуговых ионов в процесс магнетронного распыления позволяет повысить адгезию и твердость покрытий, решая общие задачи в области промышленного покрытия пресс-форм, где высокая адгезия и долговечность имеют первостепенное значение.
Такая интеграция также открывает новые возможности для выбора материалов и управления процессом. Используя сильные стороны обеих технологий, можно наносить более широкий спектр материалов с индивидуальными свойствами, от твердых износостойких покрытий до более сложных многослойных структур. В результате получается более универсальное и надежное решение для нанесения покрытий, отвечающее разнообразным требованиям различных промышленных применений.
Таким образом, сочетание многодуговых и магнетронных технологий не только повышает качество и стабильность покрытий, но и расширяет диапазон достижимых свойств материалов и эффективности процессов. Это достижение позволяет расширить границы возможностей вакуумной технологии нанесения покрытий, что делает ее краеугольным камнем в эволюции промышленных покрытий.
Современное оборудование и процессы нанесения покрытий
Компоненты и системы
Современное оборудование для нанесения покрытий представляет собой сложную совокупность важнейших компонентов, каждый из которых играет решающую роль в процессе вакуумного напыления. Сердцем этой системы являетсявакуумная камерагерметичная среда, изолирующая подложку от атмосферных условий и обеспечивающая чистоту поверхности для нанесения покрытия. Вакуумная камера обычно изготавливается из таких материалов, как нержавеющая сталь, известная своей долговечностью и устойчивостью к коррозии.
Для достижения необходимого уровня вакуума,детали для получения вакуума используются детали для получения вакуума. К ним относятся вакуумные насосы, такие как пластинчато-роторные и турбомолекулярные, которые работают в тандеме, чтобы снизить давление в камере до сверхнизкого уровня, необходимого для PVD-процессов. Эффективность этих насосов очень важна, так как она напрямую влияет на качество и однородность покрытия.
Источники питания - еще один важнейший компонент, обеспечивающий электрическую энергию, необходимую для испарения материала покрытия. В современных системах часто используютсяпромежуточно-частотные источники питания илиимпульсная технологиякоторые обеспечивают точный контроль над процессом осаждения, что приводит к получению покрытий более высокого качества. Эти усовершенствованные источники питания помогают уменьшить такие проблемы, как искрение и неравномерное осаждение, которые часто возникают в традиционных установках PVD.
И, наконец, системасистемы подачи технологического газа являются неотъемлемой частью процесса. Эти системы вводят реактивные газы в вакуумную камеру, что позволяет формировать сложные покрытия с заданными свойствами. Точный контроль расхода и состава газа позволяет создавать покрытия с особыми механическими, химическими и оптическими характеристиками, что повышает универсальность и применимость технологии.
В целом, современное оборудование для нанесения покрытий представляет собой сложное взаимодействие вакуумных камер, деталей для получения вакуума, источников питания и систем подачи технологического газа, каждый из которых вносит свой вклад в точность и качество процесса PVD.
Передовые технологии
В области вакуумных технологий нанесения покрытий появилось несколько передовых методов, значительно повышающих качество и применимость покрытий. Одним из таких методов является использованиенеравновесных магнитных полей. Эти поля позволяют более точно контролировать процесс осаждения, обеспечивая создание покрытий с превосходной однородностью и адгезией. Это особенно важно для промышленных применений, где долговечность и эксплуатационные характеристики покрытия имеют решающее значение.
Еще одним важным достижением стало появлениепромежуточно-частотных источников питания. В отличие от традиционных источников питания, эти промежуточно-частотные системы обеспечивают большую стабильность и эффективность. Они позволяют наносить более толстые и прочные покрытия, не нарушая целостности основного материала. Эта инновация особенно полезна в отраслях, где требуются высокопроизводительные покрытия для пресс-форм и инструментов.
Дополнительно,импульсная технология произвела революцию в процессе нанесения покрытий. Благодаря подаче энергии короткими, контролируемыми импульсами импульсная технология минимизирует тепловую нагрузку на подложку, предотвращая ее деформацию и разрушение. Этот метод особенно выгоден для хрупких материалов или тех, которые требуют сложной обработки поверхности. Точная подача энергии также обеспечивает более эффективную адгезию покрытия, что приводит к более долговечным и надежным результатам.
Эти передовые методы в совокупности способствуют эволюции технологии вакуумного нанесения покрытий, делая ее более универсальной и эффективной в различных промышленных областях. Интеграция неравновесных магнитных полей, среднечастотных источников питания и импульсных технологий не только улучшает качество покрытий, но и расширяет сферу их применения, отвечая все более жестким требованиям современной промышленности.
Применение и контроль качества PVD-покрытий для пресс-форм
Предварительная обработка и процессы нанесения покрытий
Методы предварительной обработки являются важнейшими этапами подготовки поверхностей к нанесению покрытий методом физического осаждения из паровой фазы (PVD). Эти методы включают высокотемпературную очистку паром, которая эффективно удаляет загрязнения и обеспечивает чистоту подложки. Пескоструйная обработка - еще один важный метод, обеспечивающий шероховатую поверхность, которая улучшает адгезию покрытия. Сам процесс нанесения PVD-покрытий в значительной степени зависит от точного контроля температуры и равномерного нагрева для достижения оптимальных результатов.
Равномерный нагрев необходим, поскольку он обеспечивает равномерный нагрев подложки, что, в свою очередь, позволяет равномерно осаждать материал покрытия. Контроль температуры не менее важен, поскольку отклонения могут привести к несоответствию толщины и качества покрытия. Для поддержания стабильных и постоянных условий нагрева часто используются такие передовые технологии, как среднечастотные источники питания и импульсная технология, что повышает общее качество PVD-покрытия.
Эти процессы предварительной обработки и нанесения покрытия являются неотъемлемой частью успеха применения PVD в промышленных пресс-формах. Они не только улучшают прочность и производительность пресс-форм, но и продлевают срок их эксплуатации, что делает их незаменимыми в условиях высокоточного производства.
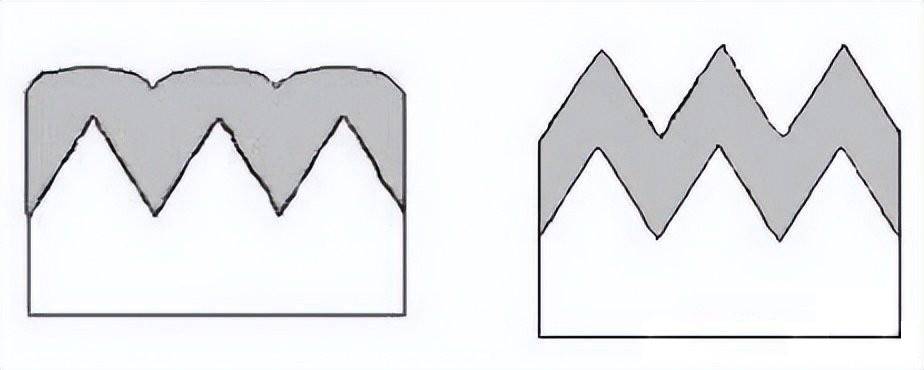
Меры контроля качества
Функциональный контроль качества (FQC) является важнейшим аспектом обеспечения надежности и производительности пресс-форм с покрытием. Этот процесс включает в себя несколько тщательных проверок, чтобы гарантировать соответствие покрытий требуемым стандартам.
Одним из основных методов FQC являетсяпроверка внешнего вида. Он включает в себя тщательный визуальный осмотр с целью выявления любых дефектов поверхности, таких как царапины, ямы или обесцвечивание. Эти дефекты могут существенно повлиять на функциональность и срок службы пресс-формы, поэтому данный этап является обязательным.
Другим ключевым методом являетсяпроверка глубины слоя. Этот метод позволяет измерить толщину слоев покрытия, чтобы убедиться в том, что они соответствуют заданным параметрам. Для точного определения глубины и равномерности покрытия используются различные приборы, такие как профилометры и сканирующие электронные микроскопы.
Сайтконтроль адгезии также имеет решающее значение. В ходе этого процесса оценивается прочность сцепления между покрытием и основой пресс-формы. Обычные методы включают в себя испытания на царапание, растяжение и поперечный разрез. Эти испытания помогают выявить любые потенциальные проблемы расслоения или отслаивания, обеспечивая долговечность и эффективность покрытия.
Интегрируя эти методы FQC, производители могут гарантировать, что их пресс-формы с покрытием не только соответствуют, но и превосходят промышленные стандарты, обеспечивая надежные и высокопроизводительные инструменты для различных промышленных применений.
СВЯЖИТЕСЬ С НАМИ ДЛЯ БЕСПЛАТНОЙ КОНСУЛЬТАЦИИ
Продукты и услуги KINTEK LAB SOLUTION получили признание клиентов по всему миру. Наши сотрудники будут рады помочь с любым вашим запросом. Свяжитесь с нами для бесплатной консультации и поговорите со специалистом по продукту, чтобы найти наиболее подходящее решение для ваших задач!