Основные принципы процесса нанесения PVD-покрытий
Испарение
В вакуумной среде твердый материал, называемый мишенью, переходит в газообразное состояние различными способами, в основном с помощью нагрева. Этот процесс, известный как испарение, является основой процесса нанесения покрытий методом физического осаждения из паровой фазы (PVD). Для достижения этого превращения используется несколько методов:
-
Термическое испарение: Этот метод предполагает нагрев материала до температуры испарения с помощью электрического сопротивления или других нагревательных элементов. Когда материал достигает точки испарения, он превращается в газ, который затем диффундирует и конденсируется на подложке, образуя тонкую пленку.
-
Электронно-лучевое испарение: Высокоэнергетический пучок электронов направляется на целевой материал, заставляя его испаряться. Этот метод особенно полезен для материалов с высокой температурой плавления, так как локализованный эффект нагрева позволяет точно контролировать процесс испарения.
-
Лазерное испарение: Используя высокоэнергетические лазерные импульсы, этот метод испаряет целевой материал. Лазерное испарение выгодно для подготовки сложных тонкопленочных материалов, поскольку оно обеспечивает высокую точность и может использоваться для испарения материалов, с которыми трудно работать традиционными методами.
Каждый из этих методов имеет свои уникальные преимущества и выбирается в зависимости от конкретных требований к процессу нанесения покрытия, таких как тип используемого материала и желаемые свойства получаемой пленки.
Транспортировка
Газообразный материал, перешедший в парообразное состояние, подвергается диффузии в вакуумной камере. Эта диффузия является критической фазой процесса PVD, поскольку она напрямую влияет на равномерность и качество последующего осаждения пленки. На эту фазу переноса существенно влияют несколько ключевых факторов:
-
Давление газа: Давление в вакуумной камере играет ключевую роль. Более низкое давление обычно повышает эффективность диффузии, обеспечивая более равномерное распределение газообразного материала по подложке. И наоборот, более высокое давление может привести к столкновениям между молекулами газа, что потенциально снижает общую скорость диффузии и влияет на однородность пленки.
-
Температура: Температура в вакуумной среде - еще одна важная переменная. Более высокие температуры могут ускорить процесс диффузии, но их необходимо тщательно контролировать, чтобы предотвратить термическое повреждение подложки или образование неоднородных отложений. Баланс между температурой и другими параметрами процесса необходим для оптимальной диффузии.
-
Положение подложки: Пространственное расположение подложки относительно источника газообразного материала также имеет большое значение. Правильное выравнивание обеспечивает равномерное поступление газообразного материала на все участки подложки, предотвращая локальное пере- или недоосаждение. Такие приемы, как вращение или наклон подложки, могут помочь добиться более равномерного покрытия.
Таким образом, транспортировка газообразного материала в вакууме - это сложный процесс, требующий тщательного контроля давления газа, температуры и расположения подложки для обеспечения успешного осаждения высококачественной пленки.
Осаждение
На этапе осаждения газообразный материал, который был доставлен на подложку, начинает охлаждаться и конденсироваться. Этот процесс охлаждения очень важен, так как он превращает газ в твердую тонкую пленку, прилипающую к поверхности подложки. Процесс осаждения - это не просто физическое изменение, но и трансформация, существенно меняющая свойства подложки в зависимости от конкретного применения.
Тип газа, используемого в процессе осаждения, играет ключевую роль в определении конечной структуры и характеристик пленки. Например, инертные газы, такие как аргон и гелий, часто используются для поддержания чистоты пленки, гарантируя отсутствие нежелательных химических реакций. С другой стороны, реактивные газы, такие как кислород, азот и фтор, вводятся для создания специфических соединений, таких как оксиды, нитриды и фториды, повышая функциональность пленки для конкретных применений.
Кроме того, давление газа в камере осаждения является критическим параметром, влияющим как на скорость осаждения, так и на качество пленки. Более низкое давление газа обычно приводит к образованию более плотных и однородных пленок, что желательно для многих применений. И наоборот, более высокое давление газа может привести к образованию более шероховатых пленок, что может быть полезно в некоторых случаях, например, когда требуется увеличение площади поверхности для лучшей адгезии или реакционной способности.
В целом, процесс осаждения представляет собой сложное взаимодействие охлаждения, типа газа и давления, каждый из факторов тщательно контролируется для достижения желаемых свойств пленки. Такая тщательная организация процесса гарантирует, что полученная тонкая пленка будет соответствовать строгим стандартам, предъявляемым различными отраслями промышленности, от электроники до оптики и не только.
Основные типы PVD-процессов
Осаждение испарением
Осаждение испарением - это сложная технология, используемая для получения тонких пленок путем нагрева целевых материалов до температуры их испарения. Этот процесс особенно эффективен для металлов и некоторых сплавов, переводя их из твердого в газообразное состояние с помощью тепловой энергии. Затем испарившиеся атомы конденсируются на подложке, образуя однородную и плотную тонкую пленку. Этот метод обычно проводится в высоковакуумной среде, чтобы свести к минимуму столкновения и загрязнения, обеспечивая чистоту и целостность осажденной пленки.
Одним из ключевых преимуществ испарительного осаждения является его способность создавать высококачественные пленки с отличной однородностью и конформностью. Этот метод универсален и позволяет осаждать широкий спектр материалов, включая металлы, керамику и полупроводники. Однако этот процесс требует высокого вакуума и очень чувствителен к факторам окружающей среды, что может ограничить его применимость в некоторых сценариях.
Осаждение напылением
Осаждение напылением - это сложный метод физического осаждения из паровой фазы (PVD), который включает в себя бомбардировку материала мишени высокоэнергетическими частицами, обычно ионами из плазмы. В результате бомбардировки целевой материал выбрасывает атомы или молекулы, которые затем проходят через вакуум и конденсируются на подложке, образуя тонкую пленку. Этот процесс универсален и применим к широкому спектру материалов, включая металлы, оксиды и нитриды.
При напылении материал подвергается воздействию плазмы, часто состоящей из ионов аргона и электронов. Эти энергичные частицы "сбивают" атомы с мишени, создавая облако исходных атомов. Затем это облако конденсируется на подложке, где образуется тонкая пленка. Выбор материала мишени и условия работы плазмы существенно влияют на характеристики осаждаемой пленки.
Одним из важных аспектов осаждения методом напыления является явление повторного напыления, когда уже осажденный материал может быть переизлучен при последующей бомбардировке ионами или атомами. Это может повлиять на однородность и толщину пленки, что требует тщательного контроля параметров осаждения для достижения желаемых результатов.
Осаждение методом напыления широко используется в различных отраслях промышленности благодаря своей способности создавать высококачественные, плотные пленки с отличной адгезией к подложке. Оно особенно популярно благодаря своей применимости к широкому спектру материалов, что делает его универсальным инструментом при изготовлении современных тонких пленок для электроники, оптики и механических компонентов.
Импульсное лазерное осаждение (PLD)
Импульсное лазерное осаждение (PLD) - это сложный процесс испарения, в котором используются высокоэнергетические лазерные импульсы для испарения целевого материала в вакуумной камере. Этот метод особенно хорошо подходит для получения сложных тонкопленочных материалов, что делает его предпочтительным выбором в различных научных и промышленных приложениях.
Процесс PLD начинается с того, что лазерный луч нацеливается на материал, заставляя его испаряться и образовывать плазму. Затем эта плазма оседает на подложке, где конденсируется, образуя тонкую пленку. Сложность этого процесса, включающего испарение, абляцию, образование плазмы и отшелушивание, требует тщательной оптимизации. Несмотря на увеличение времени и усилий, необходимых для управления многочисленными переменными, PLD обладает рядом преимуществ.
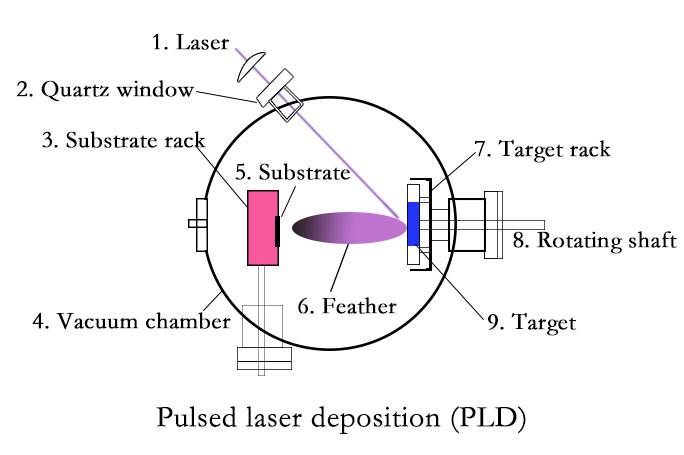
Одним из ключевых преимуществ PLD является высокая скорость осаждения, что значительно упрощает процесс по сравнению с другими методами. Кроме того, PLD не требует использования нитей, что упрощает обслуживание и уменьшает потенциальные источники загрязнения. Это делает PLD особенно подходящим для приложений, требующих высокой точности и чистоты, например, в электронной и оптической промышленности.
В общем, несмотря на то, что сложность PLD требует тщательного контроля, его способность эффективно и с минимальным обслуживанием производить высококачественные сложные тонкие пленки делает его ценным инструментом в сфере процессов нанесения покрытий методом PVD.
Химическое осаждение из паровой фазы (CVD)
Хотя химическое осаждение из паровой фазы (CVD) принципиально отличается от физического осаждения из паровой фазы (PVD), есть случаи, когда эти два метода комбинируются для достижения превосходных свойств пленки. CVD, метод вакуумного осаждения, известен тем, что позволяет получать высококачественные и высокоэффективные твердые материалы, в частности тонкие пленки, используемые в полупроводниковой промышленности. Процесс включает в себя воздействие на пластину (подложку) одного или нескольких летучих прекурсоров, которые вступают в реакцию и/или разлагаются на поверхности подложки, образуя желаемый осадок. Этот метод универсален и позволяет осаждать материалы в различных формах, включая монокристаллические, поликристаллические, аморфные и эпитаксиальные структуры.
В отличие от PVD, который основан на физических процессах, таких как испарение или напыление, CVD использует химические реакции для осаждения материалов. Такой химический подход позволяет лучше контролировать состав и свойства осажденной пленки. Однако в некоторых областях применения дополнительное использование CVD и PVD позволяет получить пленки с улучшенными характеристиками, такими как повышенная адгезия, лучшие механические свойства или более однородные покрытия. Например, предварительные PVD-слои могут быть использованы для создания более восприимчивой поверхности для последующих CVD-слоев, тем самым оптимизируя общее качество пленки.
Интеграция CVD и PVD особенно полезна в сложных процессах микрофабрикации, где сочетание химических и физических методов осаждения позволяет решать специфические задачи, с которыми ни один из методов не может справиться в одиночку. Такой гибридный подход не только расширяет спектр материалов, которые можно осаждать, но и повышает функциональность и производительность конечного продукта.
Применение газов в процессе PVD
Инертные газы
Инертные газы, такие как аргон (Ar) и гелий (He), играют важнейшую роль в процессах осаждения методом напыления, выступая в качестве газов-носителей. Эти газы предпочитают за их способность повышать эффективность напыления материала-мишени, не вызывая при этом никаких химических реакций. Такая нереакционная природа обеспечивает сохранение чистоты осаждаемой пленки, что очень важно для получения высококачественных покрытий.
Использование инертных газов не ограничивается осаждением распылением; они также применяются для предотвращения нежелательных химических реакций, которые могут разрушить образец. Как правило, к таким нежелательным реакциям относятся окисление и гидролиз, которые обычно инициируются присутствием кислорода и влаги в воздухе. Замена этих реактивных элементов инертными газами позволяет сохранить целостность образца.
Аргон, в частности, является наиболее часто используемым инертным газом в различных приложениях из-за его высокой природной распространенности и относительно низкой стоимости. Он составляет около 1 % атмосферы Земли, что делает его легкодоступным для промышленного использования. Хотя аргон является наиболее популярным, в зависимости от конкретных требований процесса могут использоваться и другие инертные газы, такие как гелий и неон.
Стоит отметить, что термин "инертный газ" зависит от контекста. Хотя инертные газы часто считаются инертными, они могут вступать в реакцию при определенных условиях, хотя и с низкой вероятностью. Эта особенность во многом обусловлена наличием у этих газов полных валентных оболочек, которые, как правило, делают их нереакционноспособными. Однако это не абсолютное правило, поскольку даже благородные газы могут образовывать соединения при определенных условиях.
При указании чистоты инертных газов принято указывать уровень загрязнения в частях на миллион (ppm). Например, уровень загрязнения в 100 ppm означает, что из каждого миллиона молекул инертного газа 100 являются чужеродными молекулами. Этот показатель имеет решающее значение для обеспечения эффективности инертного газа в поддержании чистоты осажденной пленки.
Таким образом, инертные газы, такие как аргон и гелий, незаменимы при напылении и других процессах, где сохранение чистоты и целостности материалов имеет первостепенное значение. Их нереакционная природа и доступность делают их идеальными для широкого спектра промышленных применений.
Реактивные газы
Реактивные газы играют важнейшую роль в подготовке различных тонких пленок в процессах PVD. Эти газы, включающие кислород (O₂), азот (N₂) и фтор (F₂), необходимы для создания оксидных, нитридных и фторидных пленок, соответственно. Введение этих реактивных газов часто необходимо для достижения желаемого химического состава и свойств осажденных пленок.
Например, при получении тонких пленок оксида алюминия (Al₂O₃) в качестве реакционного газа обычно вводят кислород. Это обеспечивает реакцию атомов алюминия в паровой фазе с кислородом для формирования стабильной и однородной пленки Al₂O₃. Использование реакционных газов не ограничивается оксидом алюминия; оно распространяется и на другие материалы, такие как нитрид кремния (Si₃N₄) и диоксид титана (TiO₂), где соответственно используются азот и кислород.
Выбор реактивного газа и его концентрация могут существенно повлиять на свойства пленки, включая ее плотность, твердость и химическую стабильность. Например, более высокая концентрация кислорода может привести к образованию более пористых и менее плотных пленок, а более низкая концентрация может привести к неполному окислению, что повлияет на общее качество пленки.
Таким образом, разумное использование реактивных газов - важнейший аспект PVD-процессов, позволяющий создавать высокоэффективные тонкие пленки с индивидуальными свойствами для различных применений.
Органические газы
В некоторых специализированных областях применения органические газы, такие как этилен и пропилен, играют решающую роль в получении полимерных пленок и композитов. Эти газы часто вводятся в процесс PVD для облегчения формирования специфических структур пленки, которые недостижимы при использовании только инертных или реактивных газов.
Использование органических газов в PVD-процессах особенно полезно для создания полимерных пленок, требующих специфической химической функциональности. Например, этилен может быть использован для получения полиэтиленовых пленок, которые известны своими превосходными механическими свойствами и химической стойкостью. Аналогично, пропилен можно использовать для создания полипропиленовых пленок, которые отличаются высокой термостойкостью и химической стойкостью.
Кроме того, органические газы можно комбинировать с другими газами для создания композитных пленок, в которых сочетаются свойства как органических, так и неорганических компонентов. Такой гибридный подход позволяет настраивать свойства пленок, что дает возможность создавать пленки для конкретных применений в таких отраслях, как электроника, оптика и машиностроение.
Таким образом, включение органических газов в процессы PVD открывает новые возможности для создания современных полимерных пленок и композитов, позволяя создавать материалы с уникальными и улучшенными свойствами.
Регулировка давления газа
Давление газа в PVD-процессе играет ключевую роль в определении скорости осаждения и качества пленки. Этот параметр напрямую влияет на поведение газообразного материала при его движении от мишени к подложке.
При более низком давлении газа газообразный материал имеет тенденцию к более равномерному распространению, что приводит к улучшению плотности и однородности пленки. Это происходит потому, что пониженное давление сводит к минимуму столкновения между молекулами газа, обеспечивая более упорядоченный процесс осаждения. Следовательно, полученная пленка имеет меньше дефектов и более однородную структуру.
Напротив, более высокое давление газа может привести к увеличению шероховатости пленки. В таких условиях газообразный материал чаще сталкивается, что может нарушить упорядоченный процесс осаждения. В результате получается менее однородная пленка с потенциально более высокой шероховатостью поверхности. Однако стоит отметить, что более высокое давление также может увеличить скорость осаждения, хотя и в ущерб качеству пленки.
Давление газа | Качество пленки | Скорость осаждения |
---|---|---|
Более низкое | Улучшенная плотность и однородность | Медленнее |
Выше | Повышенная шероховатость | Быстрее |
Оптимальное давление газа часто определяется специфическими требованиями конкретного приложения, балансируя между необходимостью получения высококачественных пленок и желанием обеспечить эффективную скорость осаждения. Этот тонкий баланс имеет решающее значение для достижения желаемых свойств конечного продукта.
Области применения процесса нанесения покрытий PVD
Электронная промышленность
В сфере производства полупроводниковых приборов, интегральных схем и дисплеев процесс физического осаждения паров (PVD) играет ключевую роль в изготовлении различных пленок. В частности, PVD используется для подготовки трех основных типов пленок: проводящих, изолирующих и оптических.
Проводящие пленки
Проводящие пленки необходимы для обеспечения прохождения электрического тока в электронных устройствах. Эти пленки обычно изготавливаются из таких металлов, как алюминий, медь и золото, которые осаждаются с помощью таких методов, как термическое испарение или напыление. Выбор металла и метода осаждения может существенно повлиять на проводимость, адгезию и общую производительность пленки.
Изоляционные пленки
Изоляционные пленки, с другой стороны, имеют решающее значение для предотвращения коротких замыканий и защиты чувствительных компонентов. Для создания таких пленок обычно используются такие материалы, как диоксид кремния (SiO₂) и нитрид кремния (Si₃N₄). Процесс PVD позволяет точно контролировать толщину и однородность пленки, что крайне важно для поддержания целостности и надежности устройства.
Оптические пленки
Оптические пленки предназначены для управления взаимодействием света с поверхностью устройства, повышая четкость изображения и уменьшая блики. Такие пленки часто включают антибликовые покрытия и слои, улучшающие пропускание. Процесс PVD позволяет создавать такие пленки с определенными оптическими свойствами, такими как коэффициент преломления и коэффициент пропускания, в соответствии с требованиями устройства.
Таким образом, процесс PVD незаменим в электронной промышленности, предлагая универсальный и точный метод производства проводящих, изолирующих и оптических пленок, которые являются основой современных электронных устройств.
Оптические устройства
Процесс PVD (Physical Vapor Deposition) играет важную роль в производстве оптических покрытий, которые необходимы для улучшения характеристик различных оптических устройств. К таким покрытиям относятся антибликовые покрытия, пленки, улучшающие пропускание, и защитные слои. Все они предназначены для оптимизации взаимодействия света с поверхностью устройства.
Типы оптических покрытий
-
Антибликовые покрытия: Эти покрытия предназначены для минимизации отражения света, тем самым увеличивая количество света, проходящего через оптическую поверхность. Это особенно важно в таких приложениях, как объективы камер, очки и солнечные панели.
-
Пленки для улучшения пропускания: Эти пленки предназначены для увеличения пропускания света определенной длины волны, что очень важно для таких устройств, как оптические фильтры и датчики.
-
Защитные слои: Эти покрытия защищают основной материал от воздействия факторов окружающей среды, таких как влага, пыль и механические повреждения, обеспечивая долговечность и производительность оптического устройства.
Преимущества PVD в нанесении оптических покрытий
- Точность: Процесс PVD позволяет точно контролировать толщину пленки, что очень важно для достижения желаемых оптических свойств.
- Долговечность: Оптические устройства с PVD-покрытием отличаются повышенной прочностью по сравнению с устройствами, покрытыми другими методами, что делает их идеальными для длительного использования в различных условиях.
- Универсальность: Процесс PVD может быть адаптирован для создания широкого спектра покрытий, отвечающих специфическим потребностям различных оптических приложений.
Применение в оптических устройствах
Тип устройства | Назначение покрытия |
---|---|
Объективы камер | Антибликовые покрытия для улучшения качества изображения |
Очки | Антибликовые и устойчивые к царапинам слои |
Солнечные панели | Антибликовые покрытия для максимального улавливания энергии |
Оптические фильтры | Улучшение пропускания для определенных длин волн |
Датчики | Защитные слои для обеспечения стабильной работы |
Процесс PVD не только улучшает функциональность этих устройств, но и продлевает срок их службы, что делает его незаменимой технологией в оптической промышленности.
Механические компоненты
В области обработки поверхностей механических компонентов процессы физического осаждения паров (PVD) играют ключевую роль в повышении их эксплуатационной долговечности и производительности. Методы PVD тщательно используются для повышения износостойкости, коррозионной стойкости и устойчивости к окислению этих компонентов. Это приводит к значительному увеличению срока их службы, делая их более надежными и долговечными в сложных промышленных условиях.
Применение PVD в механических компонентах - это не просто нанесение защитного слоя; это интеграция передовых достижений материаловедения для создания поверхностей, способных выдерживать экстремальные условия. Например, компоненты автомобильных двигателей, аэрокосмических турбин и промышленного оборудования часто подвергаются жестким условиям эксплуатации, которые могут привести к быстрому разрушению. Нанесение PVD-покрытий позволяет защитить эти компоненты от износа, вызванного трением, химическими реакциями и высокотемпературным воздействием.
Кроме того, PVD-покрытия могут быть адаптированы к специфическим требованиям различных механических компонентов. Будь то высокоточный инструмент в производственном секторе или критически важная деталь в медицинском приборе, возможность адаптации покрытия гарантирует, что каждый компонент будет работать оптимально в своих уникальных условиях. Такой уровень настройки достигается путем изменения параметров осаждения, таких как тип целевого материала, давление газа и температура, для точной настройки свойств получаемой пленки.
Таким образом, использование PVD-процессов для обработки поверхности механических компонентов - это стратегическая инвестиция в повышение их долговечности и производительности, что в конечном итоге способствует повышению эффективности и надежности различных промышленных применений.
Декоративные покрытия
PVD-процесс помогает создавать декоративные пленки, которые повышают эстетическую привлекательность различных изделий. Эти пленки, характеризующиеся металлическим блеском и яркими цветами, широко используются в таких отраслях, как производство ювелирных изделий, часов и предметов домашнего обихода. Процесс позволяет точно контролировать толщину и однородность пленки, обеспечивая соответствие конечного продукта высоким стандартам визуальной привлекательности и долговечности, предъявляемым в этих отраслях.
В ювелирном деле PVD-покрытия обеспечивают изысканную отделку, которая может имитировать внешний вид драгоценных металлов за меньшую стоимость. Это особенно выгодно для крупносерийного производства, где сохранение роскошного внешнего вида имеет решающее значение. Часы, с другой стороны, выигрывают от использования PVD-покрытий, которые не только повышают их визуальную привлекательность, но и обеспечивают устойчивость к царапинам и коррозии, продлевая срок службы этих часов.
Бытовые товары, такие как кухонная утварь и предметы декора, также используют PVD-покрытия для достижения современного и элегантного внешнего вида. Возможность использования различных цветов и узоров в покрытиях открывает широкие возможности для дизайна, что делает PVD универсальным инструментом в производстве потребительских товаров.
Кроме того, процесс PVD является экологически чистым, так как работает в условиях вакуума, сводя к минимуму количество отходов и уменьшая воздействие на окружающую среду, связанное с традиционными методами нанесения покрытий. Этот аспект устойчивости еще больше укрепляет его привлекательность в отраслях, где эстетика и экологическая ответственность имеют первостепенное значение.
Преимущества и проблемы процесса PVD
Преимущества
Процессы нанесения покрытий PVD обладают рядом неоспоримых преимуществ, которые делают их предпочтительным выбором в различных отраслях промышленности. Одним из наиболее значимых преимуществ является производствовысококачественные плёнки. Эти пленки демонстрируют исключительнуюадгезию,однородностьиструктурная целостностьчто очень важно для улучшения характеристик материалов с покрытием. Например, в электронной промышленности проводящие пленки с PVD-покрытием обеспечивают превосходную электропроводность и минимальные потери сигнала, а в оптических устройствах покрытия обеспечивают точные оптические свойства, которые улучшают работу устройства.
Еще одним заметным преимуществом являетсяэкологичность PVD-процессов. В отличие от некоторых других методов нанесения покрытий, PVD работает в условиях вакуума, что сводит к минимуму выделение вредных веществ в окружающую среду. Это делает PVD экологически чистым вариантом, особенно в отраслях, где действуют строгие экологические нормы. Кроме того, использование инертных газов, таких как аргон и гелий, позволяет поддерживать чистоту пленок без образования побочных продуктов, способных нанести вред окружающей среде.
Сайтуниверсальность PVD-процессов также является одним из ключевых преимуществ. PVD может применяться к широкому спектру материалов, включая металлы, керамику и полимеры, что делает его пригодным для различных применений. Будь то подготовка тонких пленок для полупроводников, повышение долговечности механических компонентов или создание декоративных покрытий для потребительских товаров, PVD предлагает гибкое решение, которое можно адаптировать к конкретным потребностям. Например, использование реактивных газов, таких как кислород и азот, позволяет создавать сложные оксидные и нитридные пленки, что еще больше расширяет спектр возможных применений.
Таким образом, сочетание высококачественного производства пленок, экологической устойчивости и широкой применимости делает процессы нанесения покрытий PVD очень выгодной технологией во многих отраслях.
Проблемы
Одной из основных проблем, связанных с процессами физического осаждения из паровой фазы (PVD), является значительнаястоимость оборудования. Передовые системы PVD, например, использующие электронно-лучевое испарение или импульсное лазерное осаждение, требуют сложного оборудования и точных систем управления, которые могут быть непомерно дорогими для небольших предприятий. Кроме того, обслуживание и калибровка этих систем требуют специальных знаний, что еще больше увеличивает общую стоимость.
Еще одной критической проблемой являетсяскорость осаждения. Достижение оптимальной скорости осаждения имеет решающее значение для эффективного производства, но на нее может влиять множество факторов, включая давление газа, температуру подложки и тип используемого материала. Более низкие скорости осаждения могут привести к увеличению времени обработки, повышая эксплуатационные расходы и потенциально влияя на качество осажденной пленки. И наоборот, более высокие скорости осаждения могут привести к получению пленок с неоптимальными свойствами, такими как пониженная плотность или повышенная шероховатость.
Контроль толщины пленки также является значительным препятствием в процессах PVD. Обеспечение равномерной толщины пленки по всей подложке очень важно для производительности и надежности конечного продукта. Однако точный контроль толщины пленки может оказаться сложной задачей, особенно при работе со сложными геометрическими формами или подложками большой площади. Колебания толщины могут привести к несоответствию свойств пленки, таких как ее оптические, механические или электрические характеристики, что может негативно сказаться на предполагаемом применении.
Для решения этих проблем ведутся исследования и технологические разработки, направленные на создание более экономичного оборудования, оптимизацию параметров осаждения и совершенствование механизмов контроля толщины пленки. Эти усилия направлены на повышение эффективности и надежности процессов PVD, что делает их более доступными и эффективными в различных отраслях промышленности.
СВЯЖИТЕСЬ С НАМИ ДЛЯ БЕСПЛАТНОЙ КОНСУЛЬТАЦИИ
Продукты и услуги KINTEK LAB SOLUTION получили признание клиентов по всему миру. Наши сотрудники будут рады помочь с любым вашим запросом. Свяжитесь с нами для бесплатной консультации и поговорите со специалистом по продукту, чтобы найти наиболее подходящее решение для ваших задач!