Процесс физического осаждения из паровой фазы (PVD) - это сложный метод, используемый для нанесения тонких пленок материала на подложку.Он включает в себя превращение твердого материала в парообразную фазу, которая затем осаждается на подложку, образуя тонкое равномерное покрытие.Процесс обычно проводится в вакууме, чтобы обеспечить чистоту и контроль над осаждением.PVD широко используется в различных отраслях промышленности для таких целей, как повышение износостойкости, улучшение коррозионной стойкости и обеспечение декоративной отделки.Процесс включает в себя несколько основных этапов, в том числе испарение материала покрытия, миграцию испаренных частиц и осаждение на подложку.
Объяснение ключевых моментов:
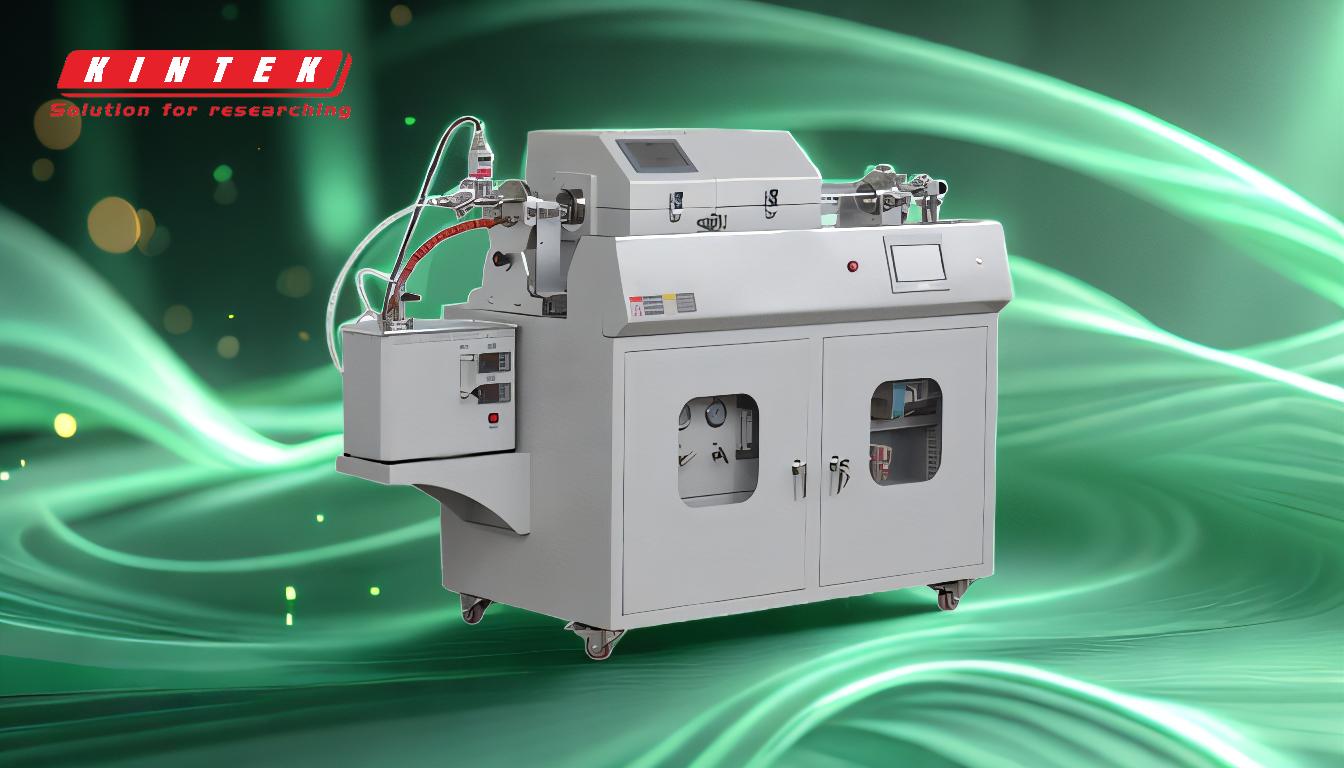
-
Испарение материала покрытия:
- Первым шагом в процессе PVD является испарение материала покрытия.Это может быть достигнуто несколькими методами, включая испарение, напыление или лазерную абляцию.
- Испарение:Материал нагревают до высокой температуры, пока он не испарится.Для этого часто используется электронный луч или резистивный нагрев.
- Напыление:Ионы высокой энергии используются для бомбардировки материала мишени, в результате чего атомы выбрасываются с поверхности и переходят в паровую фазу.
- Лазерная абляция:Мощный лазер используется для непосредственного испарения материала.
-
Миграция испаренных частиц:
- Когда материал находится в паровой фазе, частицы (атомы, молекулы или ионы) мигрируют через вакуумную камеру.На эту миграцию влияет вакуумная среда, которая минимизирует столкновения с другими частицами и обеспечивает чистоту осаждения.
- На этом этапе испарившиеся частицы могут вступать в реакции, особенно если в камеру поступают реактивные газы (например, азот или кислород).В результате этих реакций могут образовываться соединения, которые затем осаждаются на подложку.
-
Осаждение на подложку:
- Последний этап - осаждение испаренного материала на подложку.Это происходит, когда испаренные частицы конденсируются на более холодной поверхности подложки, образуя тонкую однородную пленку.
- Подложка обычно выдерживается при более низкой температуре по сравнению с испаряемым материалом, что способствует конденсации и адгезии покрытия.
- Толщину осаждаемой пленки можно точно контролировать с помощью таких методов, как мониторинг скорости кварцевого кристалла, который измеряет скорость осаждения и регулирует ее по мере необходимости.
-
Использование плазмы и реактивных газов:
- Во многих процессах PVD для улучшения процесса испарения и осаждения используется плазма.Плазма создается путем ионизации газа, часто с помощью источника индуктивно-связанной плазмы (ICP).
- Высокоэнергетическая плазма помогает диссоциировать молекулы газа на реактивные виды, которые затем могут реагировать с испаренным материалом, образуя соединения.Это особенно полезно для создания твердых, износостойких покрытий, таких как нитрид титана (TiN) или нитрид хрома (CrN).
- Введение реактивных газов (например, азота, кислорода) позволяет формировать комбинированные покрытия, которые могут обладать лучшими свойствами по сравнению с покрытиями из чистого металла.
-
Вакуумная среда:
-
Весь процесс PVD осуществляется в высоковакуумной среде.Это очень важно по нескольким причинам:
- Чистота:Вакуум минимизирует присутствие загрязнений, обеспечивая чистоту осаждения.
- Управление:Низкое давление позволяет точно контролировать процесс осаждения, включая скорость и равномерность покрытия.
- Контроль реакции:Вакуумная среда помогает контролировать реакции между испаренным материалом и любыми реактивными газами, обеспечивая стабильные свойства покрытия.
-
Весь процесс PVD осуществляется в высоковакуумной среде.Это очень важно по нескольким причинам:
-
Области применения PVD-покрытий:
-
Покрытия PVD используются в широком спектре областей применения, включая:
- Износостойкость:Покрытия, такие как TiN и CrN, используются для повышения износостойкости режущих инструментов, пресс-форм и других компонентов.
- Коррозионная стойкость:Покрытия PVD обеспечивают защиту от коррозии, продлевая срок службы компонентов, подвергающихся воздействию агрессивных сред.
- Декоративная отделка:PVD используется для создания декоративных покрытий с широким спектром цветов и отделки, часто встречающихся в бытовой электронике и ювелирных изделиях.
- Оптические покрытия:PVD используется для нанесения тонких пленок со специфическими оптическими свойствами, например, антибликовых покрытий на линзы.
-
Покрытия PVD используются в широком спектре областей применения, включая:
В целом, процесс PVD - это высококонтролируемый и универсальный метод нанесения тонких пленок материала на подложку.Он включает испарение материала покрытия, миграцию испаренных частиц и осаждение на подложку, причем все это происходит в вакуумной среде.Использование плазмы и реактивных газов позволяет создавать комбинированные покрытия с улучшенными свойствами, что делает PVD ценным методом в различных промышленных приложениях.
Сводная таблица:
Ключевые шаги | Описание |
---|---|
Испарение | Материал покрытия испаряется путем испарения, напыления или лазерной абляции. |
Миграция | Испаренные частицы перемещаются в вакууме, сводя к минимуму столкновения. |
Осаждение | Частицы конденсируются на подложке, образуя тонкую однородную пленку. |
Плазма и реактивные газы | Улучшает свойства покрытия, например, формирует TiN или CrN для повышения износостойкости. |
Вакуумная среда | Обеспечивает чистоту, контроль и постоянство реакции во время осаждения. |
Области применения | Износостойкость, защита от коррозии, декоративная отделка и оптические покрытия. |
Узнайте, как PVD-покрытия могут улучшить вашу продукцию. свяжитесь с нашими специалистами сегодня !