Искровое плазменное спекание (SPS) и обычное спекание - два разных метода, используемых для плотного превращения порошкообразных материалов в твердые формы, но они существенно отличаются по механизмам, эффективности и результатам.В SPS используется импульсный постоянный ток для генерации плазмы и внутреннего нагрева материала, что обеспечивает быструю скорость нагрева, более короткое время обработки и более тонкие микроструктуры.В отличие от традиционного спекания, использующего внешний нагрев, для достижения аналогичных результатов часто требуется более длительное время и более высокие температуры.SPS также включает в себя давление, которое помогает разрушить оксидные слои на поверхности порошка и повысить плотность.Этот метод особенно выгоден для создания материалов с уникальными свойствами, поскольку он работает при более низких температурах и давлении по сравнению с традиционными технологиями.
Объяснение ключевых моментов:
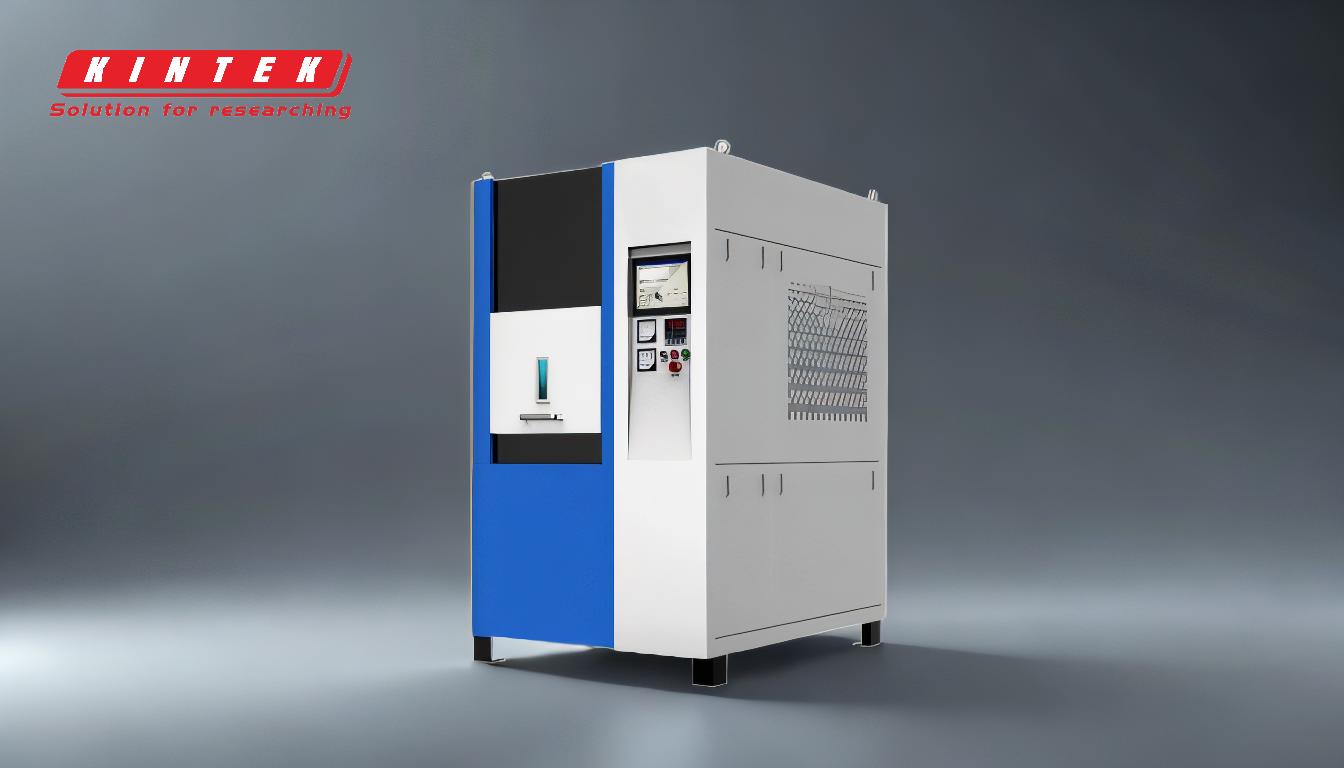
-
Механизм нагрева:
- Традиционное спекание:Использует внешние источники нагрева, такие как печи, для постепенного повышения температуры материала.Этот процесс более медленный и основан на передаче тепла от внешней поверхности материала к внутренней.
- Искровое плазменное спекание (SPS):Использует постоянный импульсный ток ON-OFF для генерации плазмы и внутреннего нагрева материала.Внутренний нагрев обеспечивает более быстрое и равномерное распределение температуры, что значительно сокращает время обработки.
-
Время обработки:
- Традиционное спекание:Может занимать несколько часов или даже дней, в зависимости от материала и желаемой плотности.Медленная скорость нагрева необходима, чтобы избежать термических напряжений и обеспечить равномерное уплотнение.
- Искровое плазменное спекание (SPS):Обычно завершается всего за несколько минут благодаря высокой скорости нагрева.Такая быстрая обработка достигается за счет прямого воздействия электрической энергии на частицы порошка.
-
Требования к температуре и давлению:
- Традиционное спекание:Часто требует более высоких температур и, в некоторых случаях, дополнительного давления для достижения плотности.Процесс также может включать более длительное время пребывания при повышенных температурах.
- Искровое плазменное спекание (SPS):Работает при более низких температурах и меньшем давлении в пресс-форме по сравнению с традиционными методами.Интеграция давления во время спекания помогает разрушить оксидные пленки на поверхности порошка, повышая плотность.
-
Микроструктура и свойства материала:
- Традиционное спекание:Может привести к увеличению размера зерен и образованию менее однородной микроструктуры из-за более низкой скорости нагрева и более длительного воздействия высоких температур.Это может повлиять на механические свойства конечного продукта.
- Искровое плазменное спекание (SPS):Создает более тонкие и однородные микроструктуры, что приводит к получению материалов с улучшенными механическими и термическими свойствами.Быстрые скорости нагрева и охлаждения предотвращают чрезмерный рост зерен, что приводит к улучшению характеристик материала.
-
Области применения и пригодность материалов:
- Традиционное спекание:Подходит для широкого спектра материалов, но может быть не идеальным для материалов, требующих точного контроля микроструктуры, или материалов, разрушающихся при высоких температурах.
- Искровое плазменное спекание (SPS):Особенно выгоден для современных материалов, таких как керамика, композиты и наноматериалы, где требуются тонкие микроструктуры и уникальные свойства.Она также позволяет спекать материалы, которые трудно обрабатывать обычными методами.
-
Энергоэффективность:
- Традиционное спекание:Как правило, менее энергоэффективны из-за более длительного времени обработки и более высокого потребления энергии.
- Искровое плазменное спекание (SPS):Более энергоэффективна, так как сокращает время и температуру, необходимые для спекания, что приводит к снижению общего потребления энергии.
В целом, искровое плазменное спекание обладает значительными преимуществами по сравнению с традиционным спеканием, включая более быстрое время обработки, более низкие требования к температуре и давлению, а также возможность получения материалов с превосходными микроструктурами и свойствами.Эти преимущества делают SPS предпочтительным методом изготовления современных материалов, особенно в тех областях, где точность и производительность имеют решающее значение.
Сводная таблица:
Аспект | Традиционное спекание | Искровое плазменное спекание (SPS) |
---|---|---|
Механизм нагрева | Внешние источники нагрева (например, печи); медленная теплопередача | Внутренний нагрев с помощью импульсного постоянного тока; быстрый и равномерный нагрев |
Время обработки | От нескольких часов до нескольких дней, в зависимости от материала и плотности | Минуты из-за высокой скорости нагрева |
Температура и давление | Требуются более высокие температура и давление | Более низкие температуры и давление в пресс-форме |
Микроструктура | Крупные зерна, менее однородные | Более мелкие, более однородные микроструктуры |
Области применения | Подходит для широкого спектра материалов | Идеально подходит для современных материалов (керамика, композиты, наноматериалы) |
Энергоэффективность | Менее энергоэффективно из-за более длительного времени обработки | Более энергоэффективный; снижает требования к времени и температуре |
Готовы узнать, как искровое плазменное спекание может произвести революцию в производстве материалов? Свяжитесь с нашими специалистами сегодня !