Продолжительность процесса спекания значительно варьируется в зависимости от материалов, технологий и специфических требований к конечному продукту.Как правило, спекание может занимать от нескольких миллисекунд до более 24 часов.Сам процесс может занимать всего несколько секунд, но этапы спекания после формы могут увеличить общее время до нескольких часов.Такие факторы, как температура, скорость нагрева, давление, размер частиц, состав и атмосфера спекания (например, воздух, вакуум или инертные газы), играют решающую роль в определении времени спекания.Высокотемпературное спекание позволяет улучшить такие свойства материала, как прочность на разрыв и энергия удара, но при этом требуется точный контроль над средой спекания.Для многих применений процесс спекания обычно составляет от 15 до 20 часов, в зависимости от материала и желаемой плотности конечной детали.
Объяснение ключевых моментов:
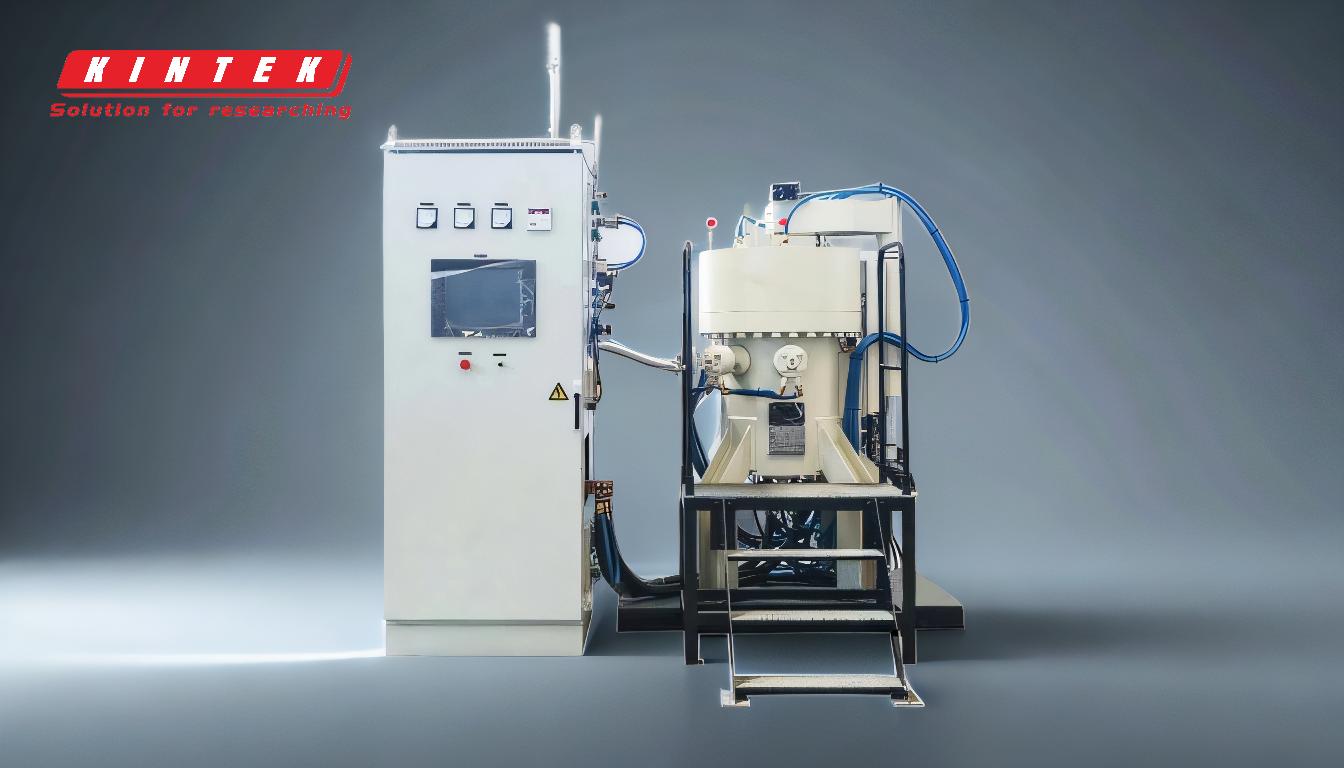
-
Диапазон времени спекания:
- Спекание может занимать от нескольких миллисекунд до более 24 часов.
- Сам процесс может занимать всего несколько секунд, но этапы спекания после изготовления формы могут увеличить общее время до нескольких часов.
-
Факторы, влияющие на время спекания:
- Температура:Определяет кинетику спекания и свойства материала.Более высокие температуры могут ускорить процесс, но должны тщательно контролироваться во избежание разрушения материала.
- Скорость нагрева:Влияет на плотность.Более высокая скорость нагрева позволяет сократить время спекания, но может привести к неравномерному уплотнению.
- Давление:Усиливает перегруппировку частиц и устраняет пористость, что позволяет сократить время спекания.
- Размер и состав частиц:Более мелкие частицы и однородный состав способствуют лучшему уплотнению, что потенциально сокращает время спекания.
-
Атмосфера спекания:
- Атмосфера (например, воздух, вакуум или аргон/азот) может существенно повлиять на процесс спекания.Инертная атмосфера часто используется для предотвращения окисления и других нежелательных реакций, которые могут повлиять на время спекания и конечные свойства материала.
-
Требования к материалу и плотности:
- Температура и время спекания в печи зависят от используемого материала и требуемой плотности конечной детали.Различные материалы имеют разные требования к спеканию, и для достижения более высокой плотности может потребоваться более длительное время спекания.
-
Типичная продолжительность спекания:
- Для многих промышленных применений процесс спекания обычно занимает от 15 до 20 часов.Эта продолжительность может варьироваться в зависимости от конкретного материала, желаемых свойств и типа используемой печи для спекания (например, ленточный конвейер, толкатель или печь периодического действия).
-
Спекание после формования:
- В то время как начальный процесс спекания может быть быстрым, этапы спекания после изготовления формы могут занимать несколько часов.Эти этапы имеют решающее значение для достижения конечных желаемых свойств и размеров спеченной детали.
-
Влияние на свойства материала:
- Высокотемпературное спекание позволяет повысить прочность на растяжение, усталостную прочность при изгибе и энергию удара.Однако достижение этих свойств часто требует точного контроля над средой спекания и может увеличить общее время спекания.
В целом, время спекания очень изменчиво и зависит от множества факторов, включая свойства материала, желаемые результаты и условия процесса.Понимание этих факторов имеет решающее значение для оптимизации процесса спекания с целью эффективного достижения желаемых свойств материала.
Сводная таблица:
Фактор | Влияние на время спекания |
---|---|
Температура | Более высокие температуры ускоряют спекание, но требуют точного контроля, чтобы избежать разрушения материала. |
Скорость нагрева | Более быстрый нагрев сокращает время, но может привести к неравномерному уплотнению. |
Давление | Усиливает перегруппировку частиц, сокращая время спекания. |
Размер частиц | Более мелкие частицы способствуют более быстрому уплотнению. |
Атмосфера для спекания | Инертные газы предотвращают окисление, влияющее на время и конечные свойства. |
Материал/плотность | Более плотные материалы или требования к высокой плотности увеличивают время спекания. |
Типичная продолжительность | 15-20 часов для многих промышленных применений, в зависимости от материала и типа печи. |
Нужна помощь в оптимизации процесса спекания? Свяжитесь с нашими специалистами сегодня для получения индивидуальных решений!