Оглавление
- Обзор холодного изостатического прессования
- Типы холодного изостатического прессования
- Преимущества холодного изостатического прессования по сравнению с одноосным прессованием
- Холодное изостатическое прессование в производстве компонентов сложной формы
- Процесс холодного изостатического прессования
- Преимущества холодного изостатического прессования для алюмооксидной керамики
- Недостатки холодного изостатического прессования керамики
- Области применения холодного изостатического прессования
- Альтернативные технологии сжатия
- Заключение
Холодное изостатическое прессование (ХИП)это широко используемый производственный процесс в различных отраслях промышленности, включая керамику, металлообработку и фармацевтику. Он предполагает приложение одинакового давления со всех сторон к материалу, помещенному в гибкую форму или мешок. Этот процесс помогает достичь равномерной плотности и сформировать сложные компоненты с замысловатой геометрией. CIP имеет ряд преимуществ по сравнению с традиционным одноосным прессованием, например, возможность формирования более сложных форм и уменьшение искажений и растрескивания за счет равномерной упаковки частиц. В этой статье блога мы рассмотрим применение, преимущества и ограничения холодного изостатического прессования.
Обзор холодного изостатического прессования
Объяснение холодного изостатического прессования
Холодное изостатическое прессование (ХИП) - это метод обработки материалов, при котором к порошковому материалу прикладывается одинаковое давление во всех направлениях. Этот процесс используется для сжатия порошка в твердую массу, создавая сырую деталь с достаточной прочностью для обработки и дальнейшей переработки.
Различие между изостатическим прессованием в мокром и сухом мешках
Одной из разновидностей холодного изостатического прессования является технология "мокрого мешка". В этом случае порошок засыпается в пресс-форму и плотно закрывается снаружи сосуда под давлением. Затем форма погружается в жидкость под высоким давлением внутри сосуда, и изостатическое давление прикладывается для сжатия порошка в форму. Технология "мокрого мешка" идеально подходит для производства нескольких форм и малых и больших партий.
С другой стороны, изостатическое прессование в сухом мешке предполагает создание интегрированной формы в самом сосуде под давлением. Порошок добавляется в форму, форма герметизируется, и давление прикладывается для сжатия порошка. Этот процесс исключает необходимость погружения пресс-формы в отдельную жидкость, что упрощает автоматизацию.
Роль качества порошка и конструкции оснастки в процессе
Качество порошка, используемого при холодном изостатическом прессовании, играет решающую роль в конечном продукте. Порошок должен обладать надлежащим гранулометрическим составом, текучестью и плотностью, чтобы обеспечить эффективное и равномерное сжатие. Кроме того, конструкция оснастки, включая используемую пресс-форму или мешок, должна быть тщательно разработана с учетом специфических требований к материалу порошка и желаемой форме.
Правильная конструкция оснастки и качество порошка необходимы для достижения желаемой плотности и прочности конечного продукта. Это особенно важно в таких отраслях, как аэрокосмическая, автомобильная и медицинская, где качественные и надежные компоненты имеют решающее значение.
В целом, холодное изостатическое прессование - это универсальная технология обработки материалов, которая позволяет сжимать порошковые материалы в твердые детали. Выбор между технологией "мокрого мешка" и "сухого мешка" зависит от конкретных производственных требований. Кроме того, качество порошка и конструкция оснастки играют важную роль в обеспечении желаемых результатов в конечном продукте.
Виды холодного изостатического прессования
Подробное описание техники мокрого прессования
При холодном изостатическом прессовании методом мокрого мешка порошковый материал засыпается в форму и плотно закрывается снаружи сосуда под давлением. Затем заполненная форма погружается в жидкость под давлением внутри сосуда под давлением. Изостатическое давление прикладывается к внешней поверхности формы, сжимая порошок в твердую массу.
Этот метод не так распространен, как другой тип холодного изостатического прессования, но во всем мире используется более 3000 прессов для мокрых мешков. Мокрые мешки бывают разных размеров, от 50 мм до 2000 мм в диаметре.
Обработка материала с помощью технологии мокрых мешков может занимать от 5 до 30 минут, что делает этот процесс относительно медленным. Однако использование насосов большого объема и усовершенствованных механизмов загрузки позволяет ускорить процесс.
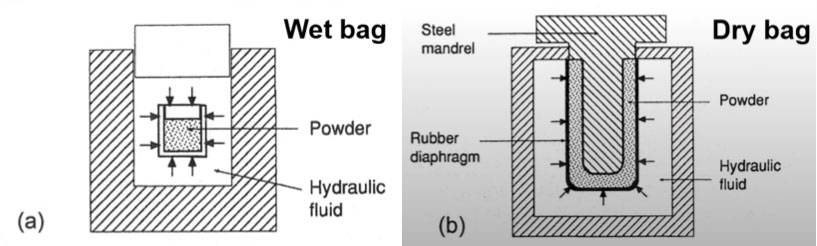
Изостатическое прессование в мокром мешке
Образец предварительно формируется, загружается в мягкий мешок, (вакуум) и погружается в гидравлическую жидкость, прикладывается высокое давление " Используется для образцов сложной формы и большого размера".
Объяснение техники прессования в сухом мешке
Метод прессования в сухом мешке, с другой стороны, предполагает создание формы, встроенной в сосуд под давлением. В этом случае порошок добавляется в форму, которая затем герметично закрывается. Применяется давление, и полученная деталь выталкивается.
По сравнению с методом "мокрого мешка", процесс "сухого мешка" поддается автоматизации и подходит для прессования длинных партий компактов при высокой производительности. Интеграция пресс-формы в емкость под давлением устраняет необходимость в погружении, что делает этот метод более эффективным.
Сравнение областей применения обоих методов
Выбор между технологиями "мокрый мешок" и "сухой мешок" зависит от конкретных требований к применению. Технология "мокрый мешок" идеально подходит для производства нескольких форм и малых и больших партий, а также для прессования крупных изделий. Она позволяет создавать сложные формы и достигать высокой плотности зеленого цвета.
С другой стороны, прессование в сухих мешках больше подходит для автоматизации и высоких темпов производства. Оно легче интегрируется в производственный процесс и исключает этап погружения, что позволяет сократить время производства.
Таким образом, и метод "мокрого мешка", и метод "сухого мешка" имеют свои преимущества и используются в разных областях. Выбор между ними зависит от таких факторов, как желаемая форма, объем производства и необходимый уровень автоматизации.
Преимущества холодного изостатического прессования по сравнению с одноосным прессованием
Возможность формирования более сложных форм
Преимущество холодного изостатического прессования (CIP) заключается в возможности формирования более сложных форм по сравнению с одноосным прессованием. При использовании CIP давление прикладывается равномерно по всей поверхности пресс-формы, что позволяет уплотнять сложные и детализированные формы. Это особенно полезно при изготовлении деталей со сложной геометрией или дизайном, которых трудно достичь с помощью одноосного прессования.

Уменьшение деформаций и трещин благодаря равномерной упаковке частиц
Одним из основных преимуществ холодного изостатического прессования по сравнению с одноосным прессованием является уменьшение деформаций и трещин в конечном продукте. При СИП давление прикладывается равномерно, что приводит к более равномерной упаковке частиц и уменьшению градиента давления. Это приводит к более однородному распределению плотности и снижает вероятность появления деформаций и трещин в готовом изделии. Это преимущество особенно важно при работе с компонентами сложной формы.
Согласно техническим соображениям, CIP обеспечивает повышенную и более равномерную плотность при заданном давлении уплотнения, что делает его особенно подходящим для хрупких или тонких порошков. Кроме того, отсутствие трения о стенки матрицы при СИП устраняет проблемы, связанные с удалением смазки, и позволяет добиться более высокой плотности прессования.
Кроме того, СИП дает преимущество более равномерной усадки во время спекания благодаря однородной зеленой плотности. Это очень важно для поддержания хорошего контроля формы и достижения однородных свойств конечного продукта. Кроме того, CIP не требует воскового связующего, как одноосное прессование, что устраняет необходимость в операциях депарафинизации.
В целом, преимущества холодного изостатического прессования по сравнению с одноосным прессованием включают возможность формирования более сложных форм и уменьшение деформаций и растрескивания благодаря равномерной упаковке частиц. Эти преимущества делают ХИП предпочтительным методом для производства компонентов со сложной геометрией и получения высококачественных, однородных изделий.
Холодное изостатическое прессование в производстве компонентов сложной формы
Сравнение СИП и литья под давлением при крупносерийном производстве
Когда требуются компоненты сложной формы, выходящие за пределы возможностей одноосного прессования, и необходима крупносерийная продукция, используются два основных варианта - СИП и литье под давлением. CIP был первым высокотехнологичным методом производства алюмооксидной керамики, о котором в литературе сообщалось в 1934 году Даубенмайером. Действительно, изоляторы свечей зажигания, вероятно, являются крупнейшим в мире керамическим компонентом, изготавливаемым методом СИП. Значительная часть из 3 миллиардов свечных изоляторов, производимых ежегодно, подвергается СИП. Как и в случае одноосного прессования, сырьем для СИП обычно служит простой измельченный глинозем Байера, измельченный и высушенный распылением глинозем Байера или, в редких случаях, высокотехнологичные высушенные распылением нанопорошки SolGel. Однако в целом СИП не так распространен в промышленности, как литье под давлением. СИП обычно используется только в тех случаях, когда требуются очень сложные формы, а литье под давлением по каким-либо причинам нецелесообразно.
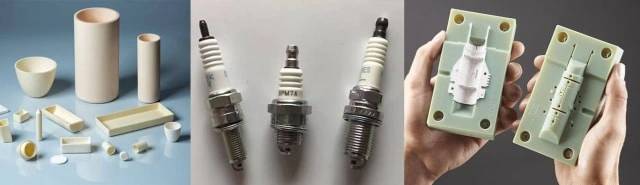
Исторический обзор использования СИП в производстве глиноземистой керамики
Холодно-изостатическое прессование (ХИП) - это технология производства металлических и керамических деталей на основе порошка, близкая к сетчатой форме. ХИП широко используется для обработки керамики, но не так широко - для металлов. Однако последние разработки в области технологических возможностей и порошковой металлургии позволили все шире использовать CIP для производства высокопроизводительных металлических деталей. Такие преимущества, как твердофазная обработка, однородная микроструктура, сложность формы, низкая стоимость инструмента и масштабируемость процесса, сделали CIP жизнеспособным способом обработки металлов. Кроме того, потенциал производства деталей практически чистой формы с минимальными отходами материала сделал этот процесс более приемлемым в таких нишевых областях, как аэрокосмическая и автомобильная промышленность.
Использование ХИП в производстве изоляторов свечей зажигания
Холодное изостатическое прессование (CIP) уже несколько десятилетий успешно используется производителями по всему миру. CIP используется для уплотнения металлических и керамических порошков с целью получения "зеленой" детали, которую можно подвергать дальнейшей обработке, например, прокатке, механической обработке или спеканию.
При типичном давлении от 1 035 до 4 138 бар (от 15 000 до 60 000 фунтов на квадратный дюйм) и температуре окружающей среды до 93°C (200°F) CIP позволяет достичь 95 % теоретической плотности керамики.
Проверенный процесс для высокопроизводительных деталей Общие области применения холодного изостатического прессования включают консолидацию керамических порошков, прессование графита, огнеупоров и электроизоляторов, а также другой тонкой керамики для стоматологии и медицины.
Технология расширяется и на новые области применения, такие как прессование мишеней для напыления, нанесение покрытий на детали клапанов в двигателе для минимизации износа головок цилиндров, телекоммуникации, электроника, аэрокосмическая и автомобильная промышленность.
Холодные изостатические прессы
Холодные изостатические прессы (CIP) используются для получения неспеченных или уплотненных зеленым красителем деталей из металлического порошка на этапе предварительного уплотнения перед прокаткой, механической обработкой или спеканием. Наши системы CIP используются компаниями по всему миру для эффективного производства безупречных компонентов для аэрокосмической, военной, промышленной и медицинской промышленности. Технологические лидеры во всем мире знают, что наши холодные изостатические прессы сконструированы таким образом, что детали легко извлекаются с достаточной прочностью для дальнейшей обработки и спекания.
Холодное изостатическое прессование
Холодное изостатическое прессование имеет преимущество при производстве деталей, когда высокая первоначальная стоимость прессовочных матриц не может быть оправдана или когда требуются очень большие или сложные компактные изделия. В промышленных масштабах изостатическому прессованию поддаются различные порошки, включая металлы, керамику, пластмассы и композиты. Давление, необходимое для прессования, варьируется от менее 5 000 до более 100 000 фунтов на квадратный дюйм (от 34,5 до 690 МПа). Порошки уплотняются в эластомерных формах мокрым или сухим способом.
При выборе услуг холодного изостатического прессования важно учитывать возможности материала. Алюминиевые и магниевые сплавы, твердые сплавы и режущие инструменты, углерод и графит, керамика и композиты - вот лишь некоторые из материалов и компонентов, которые производятся с помощью ХИП. Некоторые службы холодного изостатического прессования специализируются на нанесении покрытий и термического напыления, медных сплавов или алмазов и алмазоподобных материалов. Другие работают с электронными или электрическими материалами, взрывчатыми веществами или пиротехникой, а также со специальными и запатентованными материалами.
Процесс холодного изостатического прессования
Объяснение процесса CIP
Холодное изостатическое прессование (ХИП) - это метод обработки материалов, который заключается в уплотнении порошков путем заключения их в форму из эластомера. Форма изготавливается из таких материалов, как уретан, резина или поливинилхлорид, которые обладают низкой устойчивостью к деформации. Затем на форму равномерно подается давление жидкости, чтобы сжать ее. Этот процесс основан на законе Паскаля, который гласит, что давление, оказываемое в замкнутой жидкости, передается во всех направлениях без изменения величины.
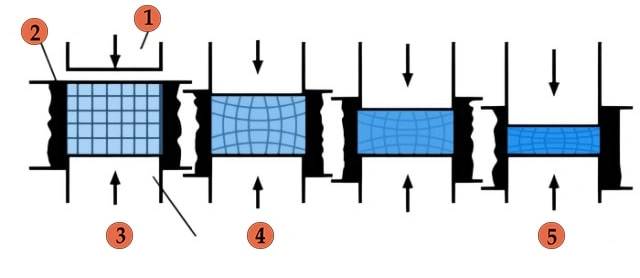
CIP может использоваться для различных материалов, таких как пластмассы, графит, порошковая металлургия, керамика и мишени для напыления. Обычно он используется для получения "сырой" детали с достаточной для обработки прочностью, которая затем может быть подвергнута дальнейшему спеканию для достижения окончательной прочности.
Автоматизация процесса CIP
Процесс CIP можно автоматизировать с помощью специализированного оборудования. Материал, подлежащий обработке, запечатывается в форму из эластомера и помещается в камеру давления. Жидкая среда, например вода или масло, закачивается в камеру, и форма равномерно подвергается высокому давлению со всех сторон. Такая автоматизация обеспечивает последовательное и точное приложение давления, что приводит к получению высококачественных готовых изделий.
Автоматизация процесса CIP дает несколько преимуществ. Она повышает эффективность, сокращая ручной труд и увеличивая производительность. Она также обеспечивает равномерное распределение давления, что повышает общее качество и надежность готовой продукции. Кроме того, автоматизация позволяет лучше контролировать и отслеживать параметры процесса, что ведет к оптимизации процесса и экономии средств.
Циклы опрессовки и разгерметизации в CIP
Процесс безразборной мойки включает в себя циклы нагнетания и разгерметизации для достижения требуемого уплотнения порошков. Во время цикла прессования жидкая среда закачивается в камеру давления, оказывая равномерное давление на форму из эластомера. Под этим давлением порошки уплотняются и образуют высококомпактное твердое вещество.
После достижения требуемого уплотнения начинается цикл разгерметизации. Давление в камере постепенно снижается, что позволяет пресс-форме расслабиться и удалить уплотненный материал. Этот цикл обеспечивает легкое извлечение уплотненного материала из формы без деформации или повреждения.
Циклы сжатия и разгерметизации тщательно контролируются для достижения желаемой плотности и прочности уплотненного материала. Параметры, такие как величина, продолжительность и скорость изменения давления, могут быть отрегулированы в соответствии с конкретными требованиями обрабатываемого материала.
Преимущества холодного изостатического прессования для алюмооксидной керамики
Сравнение ХИП с одноосным прессованием и другими методами формования керамики
Холодное изостатическое прессование (ХИП) - это технология производства металлических и керамических деталей на основе порошка, близкая к сетчатой форме. CIP широко используется для обработки керамики, но не так широко применяется для металлов. Однако последние разработки в области технологических возможностей и порошковой металлургии позволили все шире использовать CIP для производства высокопроизводительных металлических деталей. Такие преимущества, как твердофазная обработка, однородная микроструктура, сложность формы, низкая стоимость оснастки и масштабируемость процесса, сделали СИП жизнеспособным способом обработки металлов.
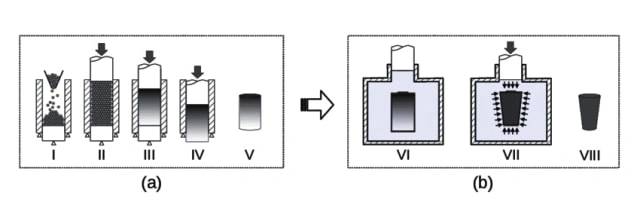
Некоторые из ключевых преимуществ СИП для алюмооксидной керамики по сравнению с одноосным прессованием заключаются в следующем:
-
Возможность получения более сложных форм: СИП позволяет изготавливать изделия более сложной формы по сравнению с одноосным прессованием. Это связано с тем, что в CIP используются гибкие пресс-формы, в которых можно создавать сложные конструкции и формы.
-
Значительное снижение градиентов давления прессования: CIP значительно снижает градиенты давления прессования, что помогает минимизировать искажения и трещины в процессе формования. Это гарантирует, что конечные керамические компоненты обладают повышенной точностью размеров и структурной целостностью.
Преимущества CIP для сложных деталей с небольшим объемом производства
CIP предлагает ряд преимуществ для производства сложных деталей с небольшими партиями. К этим преимуществам относятся:
-
Низкая стоимость пресс-формы: CIP требует низкой стоимости пресс-формы, что делает его идеальным для производства сложных деталей с небольшим тиражом. В отличие от других методов керамического формования, CIP не требует дорогостоящих форм, что позволяет снизить производственные затраты.
-
Отсутствие затрат на пресс-формы после СИП: Помимо низкой стоимости пресс-форм, CIP также устраняет необходимость в пресс-формах для процессов после CIP. Это еще больше снижает производственные затраты и обеспечивает большую гибкость при изготовлении сложных деталей.
-
Отсутствие ограничений по размерам: CIP не имеет ограничений по размерам, за исключением пределов камеры прессования. Это делает ее пригодной для производства очень крупных деталей, особенно сложных форм. На самом деле с помощью CIP успешно изготавливались детали весом более 1 тонны.
-
Короткое время цикла обработки: CIP имеет короткое время цикла обработки, поскольку не требует сушки или выжигания связующего. Это означает, что сформированные керамические компоненты могут быть спечены быстрее по сравнению с другими методами, что приводит к повышению эффективности производства.
Несмотря на то что СИП обладает многочисленными преимуществами при производстве глиноземистой керамики, важно отметить некоторые его ограничения. К ним относятся ограниченный контроль размеров, сложность формы, уступающая литью под давлением (PIM), и требование к порошкам с отличной текучестью.
Недостатки холодного изостатического прессования для керамики
Проблемы с контролем размеров и сложностью формы
Холодное изостатическое прессование (ХИП) - это процесс уплотнения порошка, который используется для получения деталей, готовых к спеканию. Однако при использовании CIP для керамики возникают некоторые проблемы, связанные с контролем размеров и сложностью формы.
Более низкая точность прессованных поверхностей, прилегающих к гибкому пакету, по сравнению с механическим прессованием или экструзией часто требует последующей механической обработки. Это означает, что для достижения желаемых размеров и формы керамических деталей могут потребоваться дополнительные операции.
Требования к порошкам, используемым в CIP
Одним из недостатков холодного изостатического прессования является то, что для полностью автоматических прессов с сухими мешками обычно требуется относительно дорогой порошок, высушенный распылением. Это может увеличить общую стоимость процесса, поскольку необходимо использовать специализированные порошки.
Кроме того, производительность СИП ниже по сравнению с экструзией или прессованием под давлением. Это означает, что процесс может быть не столь эффективным с точки зрения объема производства.
Области применения холодного изостатического прессования
Широко распространенное применение СИП в массовом производстве современной керамики
Холодное изостатическое прессование (ХИП) - это технология обработки керамики на основе порошка, близкая к сетчатой форме, которая обычно используется для обработки керамики. Ее преимущество заключается в том, что она позволяет изготавливать детали, когда высокая первоначальная стоимость штампов для прессования не может быть оправдана или когда требуются очень большие или сложные компакты.
Изостатическому прессованию в промышленных масштабах поддаются различные порошки, включая металлы, керамику, пластмассы и композиты. Давление, необходимое для прессования, варьируется от менее чем 5 000 фунтов на квадратный дюйм до более чем 100 000 фунтов на квадратный дюйм. Порошки уплотняются в эластомерных формах мокрым или сухим способом.
CIP широко используется для уплотнения керамических порошков, графита, огнеупорных материалов, электрических изоляторов и сжатия усовершенствованной керамики. Такие материалы, как нитрид кремния, карбид кремния, нитрид бора, карбид бора, борид титана и шпинель, могут быть обработаны с помощью CIP.
Технология расширяет сферу применения, например, прессование мишеней для напыления, нанесение покрытий на компоненты клапанов, используемых для уменьшения износа цилиндров в двигателях, а также различные применения в телекоммуникациях, электронике, аэрокосмической и автомобильной промышленности.
Примеры компонентов, получаемых с помощью CIP
CIP обычно используется для консолидации керамических порошков, прессования графита, огнеупоров и электроизоляторов, а также другой тонкой керамики для стоматологии и медицины. Она также используется для прессования мишеней для напыления, нанесения покрытий на детали клапанов в двигателях для минимизации износа головок цилиндров, а также в различных областях телекоммуникаций, электроники, аэрокосмической и автомобильной промышленности.
Оборудование CIP используется для снижения производственных затрат и необходимо для получения готовой продукции из сырья. Процесс включает в себя заключение порошков в форму из эластомера, помещение формы в камеру давления, закачивание жидкой среды и равномерное воздействие на форму высокого давления со всех сторон. CIP может использоваться с порошковой металлургией, цементированными карбидами, огнеупорными материалами, графитом, керамикой, пластмассами и другими материалами.

При выборе услуг по холодному изостатическому прессованию важно учитывать возможности материала. Алюминиевые и магниевые сплавы, твердые сплавы и режущие инструменты, углерод и графит, керамика, композиты и другие материалы могут быть получены с помощью СИП. Некоторые службы холодного изостатического прессования специализируются на нанесении покрытий и термическом напылении, производстве медных сплавов, алмазов и алмазоподобных материалов, электронных или электротехнических материалов, взрывчатых веществ и пиротехники, а также специальных и запатентованных материалов.
Холодное изостатическое прессование выполняется при комнатной температуре и использует форму, изготовленную из эластомерного материала, такого как уретан, резина или поливинилхлорид. Жидкость, используемая при холодном изостатическом прессовании, обычно представляет собой масло или воду, а давление жидкости во время операции обычно составляет от 60 000 фунтов/дюйм2 до 150 000 фунтов/дюйм2. Недостатком этого производственного процесса является низкая геометрическая точность из-за гибкости пресс-формы.
Альтернативные технологии сжатия
Обзор других технологий сжатия
В сфере обработки материалов существует несколько мощных технологий сжатия. Два из них, холодное изостатическое прессование (CIP) и горячее изостатическое прессование (HIP), широко используются в различных отраслях промышленности. Хотя оба метода направлены на улучшение свойств материала, они отличаются условиями эксплуатации и обладают уникальными преимуществами.
Внедрение ударно-волнового уплотнения в качестве альтернативы
Хотя CIP и HIP являются эффективными методами уплотнения, для решения конкретных задач были разработаны альтернативные технологии. Одной из таких альтернатив является ударно-волновое уплотнение, также известное как ударное сжатие.
Ударно-волновое уплотнение предполагает создание короткой ударной волны высокого давления, которая может сильно деформировать частицы или даже вызвать локальное плавление. В результате этого процесса материал становится полностью плотным и компактным без значительного роста зерен. Ударные волны характеризуются очень высоким давлением, средней температурой, очень коротким временем реакции и очень высокой скоростью деформации.
Различные методы, такие как воздушные пушки и взрывные ударные волны, которые ранее использовались для сжатия порошков микронного размера, теперь используются для сжатия нанопорошков. Эти альтернативные технологии сжатия с очень коротким временем нагрева показали успешные результаты в получении полностью плотных и компактных материалов без огрубления нанозерна.
Одним из примеров ударно-волнового уплотнения является использование плоского устройства ударно-волнового уплотнения, оснащенного воздушной пушкой. Это устройство генерирует короткую ударную волну высокого давления, которая деформирует частицы и позволяет достичь полной плотности и уплотнения. Эти альтернативные технологии сжатия предлагают эффективный способ обработки материалов с минимальным ростом зерен и улучшенными свойствами материала.
В резиновой промышленности передовые прессы используются для эффективной вулканизации резины. Применяя контролируемое давление на резиновые материалы, эти машины проверяют физические характеристики резиновых изделий, такие как прочность, упругость и долговечность, обеспечивая их соответствие стандартам ASTM и высокое качество.
В целом, альтернативные технологии сжатия, такие как ударно-волновое уплотнение, предлагают инновационные решения для получения полностью плотных и компактных материалов с улучшенными свойствами. Эти технологии обладают уникальными преимуществами и могут быть использованы в различных отраслях промышленности для расширения возможностей обработки материалов.
Заключение
В заключение,холодное изостатическое прессование (ХИП) является весьма универсальной и эффективной технологией для производства компонентов сложной формы, особенно в производстве передовой керамики. В отличие от традиционного одноосного прессования, СИП позволяет формировать более сложные формы и снижает риск деформаций и растрескивания благодаря равномерной упаковке частиц. Несмотря на сложности с контролем размеров и требованиями к порошку, СИП обладает значительными преимуществами при небольших объемах производства и широко используется в массовом производстве современной керамики. В качестве альтернативы СИП для некоторых видов прессования стоит рассмотреть ударно-волновое уплотнение.
СВЯЖИТЕСЬ С НАМИ ДЛЯ БЕСПЛАТНОЙ КОНСУЛЬТАЦИИ
Продукты и услуги KINTEK LAB SOLUTION получили признание клиентов по всему миру. Наши сотрудники будут рады помочь с любым вашим запросом. Свяжитесь с нами для бесплатной консультации и поговорите со специалистом по продукту, чтобы найти наиболее подходящее решение для ваших задач!