Тонкие пленки, осажденные испарением, - это тип слоя материала, созданного путем нагревания исходного материала в вакууме до испарения, после чего пары конденсируются на подложке, образуя тонкий однородный слой.Этот метод широко используется в различных отраслях промышленности, включая электронику, оптику и покрытия, благодаря его способности создавать высокочистые пленки с точным контролем толщины.Процесс включает в себя несколько этапов, в том числе создание вакуума, нагрев материала, испарение и осаждение.Полученные пленки могут быть адаптированы для конкретных применений путем изменения таких параметров, как температура, давление и материал подложки.Этот метод особенно ценится за простоту, масштабируемость и возможность осаждения широкого спектра материалов.
Ключевые моменты объяснены:
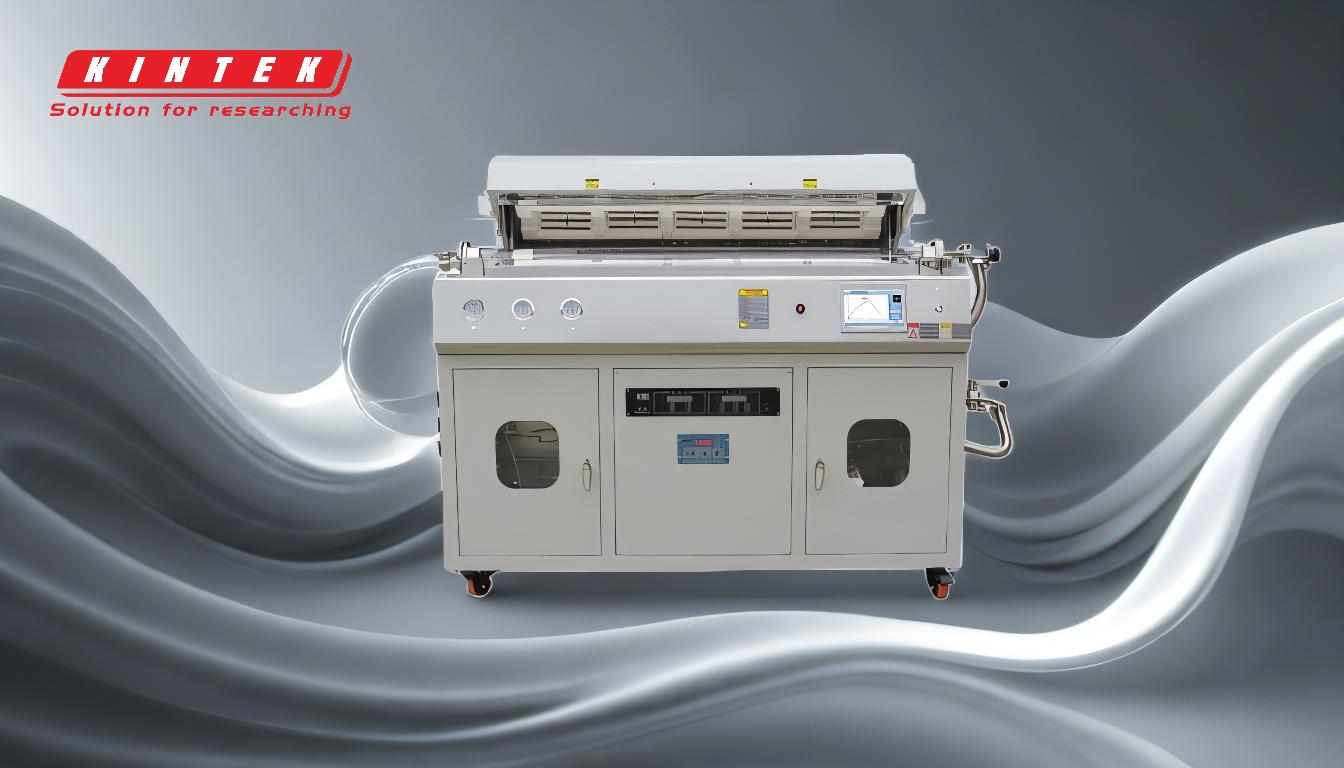
-
Определение тонких пленок, осажденных испарением:
- Тонкие пленки, нанесенные методом испарения, представляют собой сверхтонкие слои материала, созданные в результате процесса, при котором исходный материал нагревается в вакууме до тех пор, пока он не испарится.Затем пар конденсируется на подложке, образуя однородную пленку.Эта техника незаменима в отраслях, где требуются точные слои материала, например, в производстве полупроводников и оптических покрытий.
-
Процесс испарения:
- Процесс начинается с создания вакуумной среды для минимизации загрязнений и обеспечения чистоты поверхности осаждения.Затем исходный материал нагревается с помощью таких методов, как резистивный нагрев, нагрев электронным лучом или лазерная абляция.По мере испарения материала он проходит через вакуум и конденсируется на подложке, образуя тонкую пленку.Толщину и однородность пленки можно контролировать, регулируя скорость испарения и температуру подложки.
-
Виды техники испарения:
- Термическое испарение:Предполагает нагрев исходного материала с помощью резистивного нагревателя.Этот метод прост и экономически эффективен, но ограничен материалами с низкой температурой плавления.
- Электронно-лучевое испарение:Использует сфокусированный электронный луч для нагрева исходного материала, что позволяет осаждать материалы с высокой температурой плавления.Эта технология позволяет лучше контролировать скорость осаждения и чистоту пленки.
- Лазерная абляция:Использует высокоэнергетический лазер для испарения исходного материала.Этот метод подходит для сложных материалов и многослойных структур.
-
Применение тонких пленок, осажденных испарением:
- Электроника:Используется при изготовлении полупроводников, солнечных батарей и тонкопленочных транзисторов.Высокая чистота и точный контроль толщины делают его идеальным для этих целей.
- Оптика:Применяется в антибликовых покрытиях, зеркалах и оптических фильтрах.Способность осаждать однородные пленки с определенными оптическими свойствами имеет решающее значение в этой области.
- Покрытия:Используется для нанесения защитных и декоративных покрытий на различные поверхности, включая металлы, стекло и пластик.Пленки повышают долговечность, коррозионную стойкость и эстетическую привлекательность.
-
Преимущества испарительного осаждения:
- Высокая чистота:Вакуумная среда минимизирует загрязнение, что позволяет получать пленки высокой чистоты.
- Точный контроль толщины:Скорость и время осаждения могут быть точно настроены для достижения желаемой толщины пленки.
- Универсальность:С помощью этого метода можно осаждать широкий спектр материалов, включая металлы, полупроводники и изоляторы.
- Масштабируемость:Процесс может быть масштабирован для промышленного производства, что делает его пригодным для крупномасштабного применения.
-
Проблемы и ограничения:
- Материальные ограничения:Некоторые материалы могут разлагаться или вступать в реакцию в процессе нагрева, что ограничивает их использование при осаждении испарением.
- Проблемы с равномерностью:Достижение равномерной толщины пленки на больших площадях может быть сложной задачей, особенно при сложной геометрии.
- Стоимость:Высоковакуумные системы и специализированное оборудование могут быть дорогими, особенно для электронно-лучевых и лазерных методов абляции.
-
Будущие тенденции и инновации:
- Передовые материалы:Ведутся исследования по разработке новых материалов и композитов, которые могут быть осаждены с помощью методов испарения, что расширяет спектр их применения.
- Оптимизация процессов:Ожидается, что усовершенствование вакуумной технологии, методов нагрева и контроля осаждения повысит эффективность и качество тонких пленок.
- Интеграция с другими методами:Сочетание осаждения испарением с другими методами осаждения тонких пленок, такими как напыление или химическое осаждение из паровой фазы, может привести к разработке гибридных процессов с расширенными возможностями.
В целом, тонкие пленки, осажденные методом испарения, являются критически важной технологией в современном производстве и исследованиях.Этот процесс отличается высокой чистотой, точным контролем и универсальностью, что делает его незаменимым в таких областях, как электроника, оптика и покрытия.Несмотря на существующие трудности, постоянный прогресс в области материалов и технологий продолжает расширять возможности применения и эффективность этого метода.
Сводная таблица:
Аспект | Подробности |
---|---|
Определение | Сверхтонкие слои, созданные путем испарения исходного материала в вакууме. |
Процесс | Создание вакуума, нагрев материала, испарение и осаждение. |
Методы | Термическое, электронно-лучевое и лазерное абляционное испарение. |
Области применения | Электроника, оптика, защитные/декоративные покрытия. |
Преимущества | Высокая чистота, точный контроль толщины, универсальность и масштабируемость. |
Проблемы | Ограничения по материалу, проблемы с однородностью и высокая стоимость оборудования. |
Тенденции будущего | Передовые материалы, оптимизация процессов и гибридные методы осаждения. |
Узнайте, как тонкие пленки, осажденные методом испарения, могут улучшить ваши проекты. свяжитесь с нашими экспертами сегодня !