Конечная температура спекания имеет решающее значение, поскольку она напрямую влияет на микроструктуру, механические свойства и общее качество спеченного материала. Он определяет степень уплотнения, роста зерен и фазовых превращений, которые необходимы для достижения желаемых свойств материала, таких как прочность, долговечность и эксплуатационные характеристики. Точный контроль конечной температуры спекания обеспечивает оптимальную кинетику спекания, сводит к минимуму дефекты и согласовывает конечный продукт с требованиями предполагаемого применения.
Объяснение ключевых моментов:
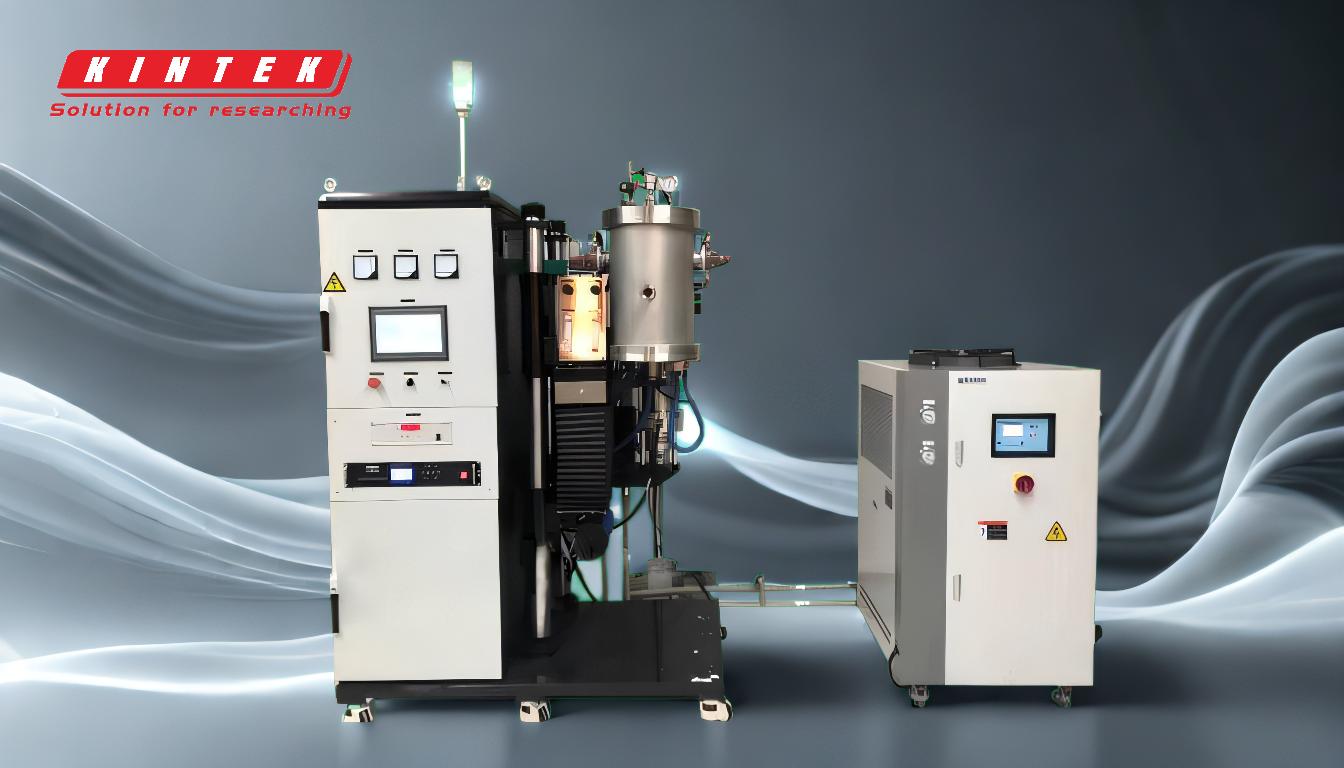
-
Влияние на уплотнение и микроструктуру:
- Конечная температура спекания определяет степень уплотнения, то есть процесса уменьшения пористости и увеличения плотности материала. Более высокие температуры усиливают механизмы связывания и диффузии частиц, что приводит к более компактной и однородной микроструктуре.
- На рост зерна также влияет температура. Чрезмерные температуры могут привести к неконтролируемому росту зерен, что может привести к ухудшению механических свойств, а недостаточные температуры могут привести к неполному спеканию и остаточной пористости.
-
Механические свойства:
- Высокотемпературное спекание улучшает ключевые механические свойства, такие как прочность на растяжение, усталостная прочность на изгиб и энергия удара. Эти свойства имеют решающее значение для материалов, используемых в требовательных приложениях, таких как аэрокосмическая, автомобильная и медицинская техника.
- Конечная температура гарантирует, что материал достигнет желаемой твердости, ударной вязкости и износостойкости, которые необходимы для долгосрочной эксплуатации.
-
Фазовые превращения и материальный состав:
- Конечная температура спекания может вызвать фазовые превращения, такие как образование новых кристаллических фаз или стабилизация определенных микроструктур. Эти преобразования существенно влияют на тепловые, электрические и механические свойства материала.
- Для материалов сложного состава конечную температуру необходимо тщательно выбирать, чтобы обеспечить равномерное распределение фаз и предотвратить нежелательные реакции или сегрегацию.
-
Кинетика спекания и механизмы диффузии.:
- Температура является основной движущей силой кинетики спекания, влияя на такие процессы, как диффузия по границам зерен и объемная диффузия. Эти механизмы отвечают за связывание и уплотнение частиц.
- Более высокие температуры ускоряют диффузию, обеспечивая более быстрое спекание и лучшую перегруппировку частиц. Однако скорость нагрева и охлаждения также необходимо контролировать, чтобы избежать термических напряжений или неравномерного спекания.
-
Контроль пористости и дефектов:
- Конечная температура спекания играет решающую роль в минимизации пористости и устранении дефектов. Правильный контроль температуры гарантирует, что материал достигнет своей теоретической плотности без образования трещин и пустот.
- Неполное спекание из-за недостаточной температуры может привести к появлению остаточной пористости, которая ослабляет материал и снижает его эксплуатационные характеристики в критических применениях.
-
Влияние среды спекания:
- Атмосфера спекания (например, воздух, вакуум или инертные газы) взаимодействует с конечной температурой, влияя на свойства материала. Например, вакуумная среда может предотвратить окисление и повысить уплотнение при высоких температурах.
- Выбор печи для спекания и однородность ее температуры также имеют решающее значение для достижения стабильных результатов по всему материалу.
-
Требования к конкретному приложению:
- Конечная температура спекания должна соответствовать предполагаемому применению материала. Например, материалы, используемые в высокотемпературных средах, могут потребовать спекания при повышенных температурах, чтобы обеспечить стабильность и производительность в условиях эксплуатации.
- Температура часто подбирается для достижения определенных свойств, таких как теплопроводность, удельное электрическое сопротивление или коррозионная стойкость, в зависимости от применения.
-
Оптимизация и согласованность процессов:
- Точный контроль конечной температуры спекания обеспечивает повторяемость и постоянство процесса, которые необходимы для промышленного производства. Колебания температуры могут привести к несоответствию между партиями, влияя на качество и надежность продукции.
- Передовые методы спекания, такие как искровое плазменное спекание или горячее изостатическое прессование, основаны на точном контроле температуры для достижения превосходных свойств материала.
Таким образом, конечная температура спекания является критическим параметром, который напрямую влияет на микроструктуру материала, механические свойства и общие характеристики. Его необходимо тщательно выбирать и контролировать, чтобы он соответствовал конкретным требованиям материала и его предполагаемого применения, обеспечивая оптимальные результаты и стабильное качество.
Сводная таблица:
Аспект | Влияние конечной температуры спекания |
---|---|
Уплотнение и микроструктура | Управляет уменьшением пористости, связыванием частиц и ростом зерен. Более высокие температуры повышают однородность. |
Механические свойства | Повышает прочность на разрыв, твердость, ударную вязкость и износостойкость для требовательных применений. |
Фазовые превращения | Вызывает образование новых фаз, влияющих на тепловые, электрические и механические свойства. |
Кинетика спекания | Ускоряет механизмы диффузии для более быстрого спекания и лучшей перегруппировки частиц. |
Пористость и дефекты | Минимизирует пористость и дефекты, обеспечивая материалу теоретическую плотность. |
Спекание окружающей среды | Взаимодействует с атмосферой (например, вакуумом) для усиления уплотнения и предотвращения окисления. |
Требования к приложению | Выравнивает температуру в соответствии с назначением материала, обеспечивая стабильность и производительность. |
Согласованность процесса | Обеспечивает повторяемость и последовательность в промышленном производстве, избегая изменений от партии к партии. |
Нужна помощь в оптимизации процесса спекания? Свяжитесь с нашими экспертами сегодня для индивидуальных решений!