SPS (Spark Plasma Sintering) - это передовая технология производства материалов, сочетающая принципы горячего прессования и импульсного электрического тока для достижения быстрого и эффективного спекания материалов.Этот процесс характеризуется способностью создавать материалы с уникальными микроструктурами и свойствами благодаря точному контролю температуры, давления и скорости нагрева.SPS работает в вакууме или контролируемой атмосфере для предотвращения окисления и обеспечения чистоты материала.Процесс включает четыре основных этапа: удаление газа и создание вакуума, создание давления, резистивный нагрев и охлаждение.Эффект искровой плазмы, создаваемый импульсными токами, препятствует росту частиц и позволяет создавать материалы с заданными составом и свойствами.SPS широко используется в научных исследованиях и промышленности, в частности для синтеза передовых материалов, таких как сверхвысокотемпературная керамика.
Ключевые моменты:
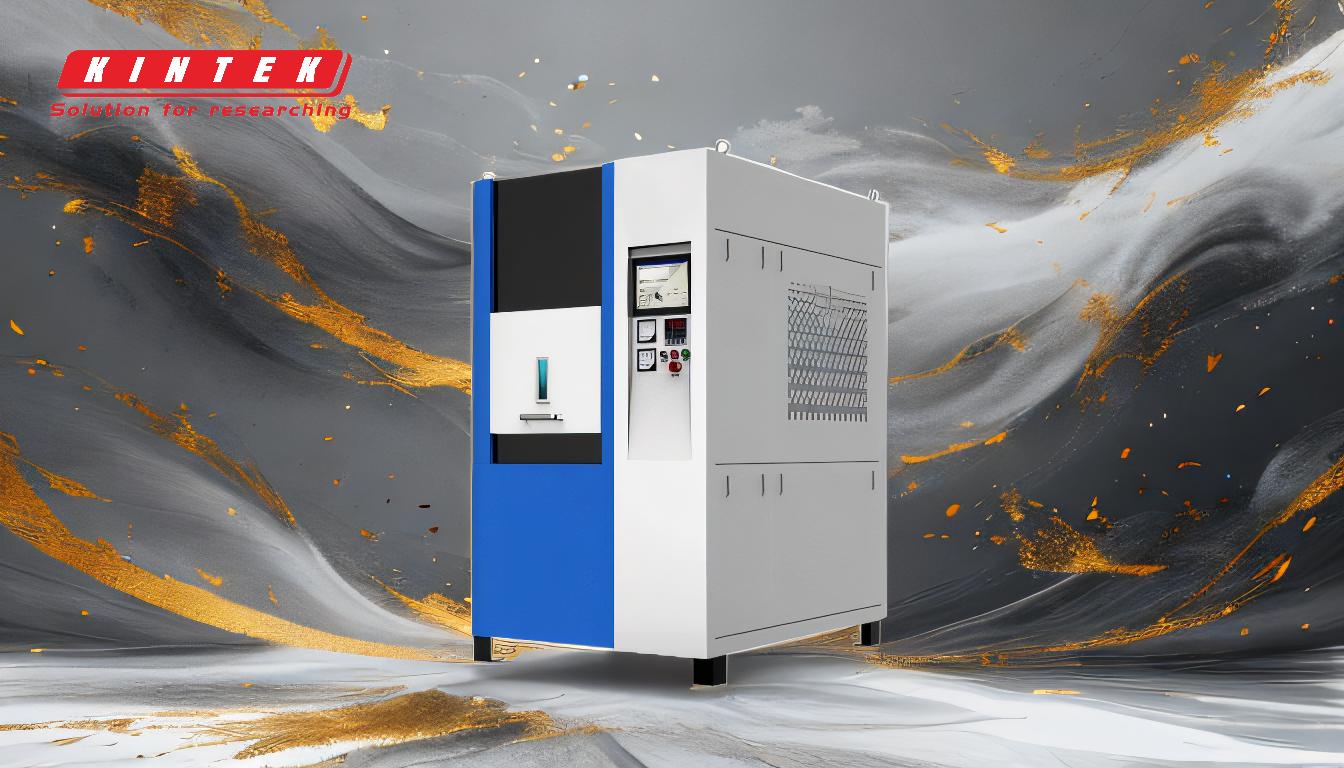
-
Определение и цель обработки SPS:
- SPS, или искровое плазменное спекание, - это технология изготовления материалов, сочетающая горячее прессование с импульсными электрическими токами для эффективного спекания материалов.
- Она предназначена для получения материалов с уникальной микроструктурой и свойствами, таких как керамика высокой плотности, наноматериалы и композиты, которые трудно получить обычными методами.
-
Основной механизм:Эффект искровой плазмы:
- Процесс основан на \"эффекте искровой плазмы"\, когда импульсные электрические токи создают локальные высокие температуры на поверхности частиц.
- Этот эффект приводит к испарению, плавлению и образованию пустот между частицами, что приводит к быстрому уплотнению и спеканию.
- Эффект искровой плазмы также препятствует росту частиц, что позволяет создавать мелкозернистые материалы с улучшенными механическими и термическими свойствами.
-
Основные этапы процесса SPS:
-
Этап 1: Удаление газа и создание вакуума:
- Из камеры удаляются газы и создается вакуум, предотвращающий окисление и обеспечивающий чистоту материала.
-
Этап 2: применение давления:
- К порошку прикладывается одноосное давление, способствующее перегруппировке и уплотнению частиц.
-
Стадия 3: Резистивный нагрев:
- Импульсные электрические токи проходят через графитовую матрицу и образец, выделяя тепло за счет резистивного нагрева.
-
Этап 4: Охлаждение:
- После спекания образец охлаждается в контролируемых условиях для сохранения желаемой микроструктуры и свойств.
-
Этап 1: Удаление газа и создание вакуума:
-
Преимущества SPS-обработки:
-
Высокая скорость нагрева и короткое время обработки:
- SPS достигает скорости нагрева до сотен градусов в минуту, что значительно сокращает время обработки по сравнению с традиционными методами спекания.
-
Низкие температуры спекания:
- Процесс протекает при более низких температурах, чем традиционное спекание, что сводит к минимуму рост зерен и сохраняет тонкие микроструктуры.
-
Точный контроль:
- Можно точно контролировать температуру, давление и скорость нагрева, что позволяет изготавливать материалы с индивидуальными свойствами.
-
Универсальность:
- SPS подходит для широкого спектра материалов, включая керамику, металлы, композиты и наноматериалы.
-
Высокая скорость нагрева и короткое время обработки:
-
Области применения технологии SPS:
-
Синтез перспективных материалов:
- SPS используется для производства сверхвысокотемпературной керамики (например, ZrC), наноматериалов и функционально-градиентных материалов.
-
Исследования и разработки:
- Этот метод широко используется в исследованиях в области материаловедения для изучения новых составов и свойств.
-
Промышленное производство:
- SPS применяется в отраслях, где требуются высокоэффективные материалы, таких как аэрокосмическая, автомобильная и электронная промышленность.
-
Синтез перспективных материалов:
-
Оборудование и управление технологическими процессами:
-
Графитовые штампы:
- Графит обычно используется для изготовления пресс-формы благодаря своей высокой тепло- и электропроводности.
-
Интерфейс сенсорного экрана:
- Управление и программирование процесса осуществляется с помощью сенсорного экрана, что позволяет точно настраивать параметры и осуществлять мониторинг в режиме реального времени.
-
Вакуум или контролируемая атмосфера:
- Процесс проводится в вакууме или в среде инертного газа для предотвращения загрязнения и обеспечения чистоты материала.
-
Графитовые штампы:
-
Сравнение с традиционными методами:
- SPS обладает значительными преимуществами по сравнению с традиционными методами спекания, такими как более быстрое время обработки, меньшее потребление энергии и возможность получения материалов с уникальными свойствами.
- Традиционные методы часто требуют более высоких температур и длительного времени обработки, что приводит к росту зерен и снижению характеристик материала.
Таким образом, SPS-обработка - это передовая технология, позволяющая быстро и точно изготавливать современные материалы.Уникальное сочетание импульсных электрических токов, контролируемого давления и высокой скорости нагрева делает ее мощным инструментом для материаловедов и инженеров.Как для научных исследований, так и для промышленного применения SPS предлагает беспрецедентный контроль и универсальность, что делает ее ключевой технологией в разработке материалов нового поколения.
Сводная таблица:
Аспект | Подробности |
---|---|
Определение | Сочетает горячее прессование и импульсные электрические токи для эффективного спекания. |
Основной механизм | Эффект искровой плазмы обеспечивает быстрое уплотнение и получение мелкозернистых материалов. |
Основные этапы | Удаление газа, создание давления, резистивный нагрев и контролируемое охлаждение. |
Преимущества | Высокая скорость нагрева, низкие температуры спекания, точный контроль, универсальность. |
Области применения | Синтез керамики, наноматериалов и промышленных высокоэффективных материалов. |
Оборудование | Графитовые матрицы, сенсорный интерфейс, вакуум/контролируемая атмосфера. |
Сравнение | Быстрота, низкое энергопотребление и лучшие свойства материалов по сравнению с традиционными методами. |
Раскройте потенциал передовых материалов с помощью технологии SPS. свяжитесь с нашими специалистами сегодня чтобы узнать больше!