Процесс спекания зависит от нескольких критических переменных, которые определяют конечные свойства спеченного материала.Эти переменные включают температуру, скорость нагрева, давление, размер частиц, состав и атмосферу спекания (например, воздух, вакуум или инертные газы, такие как аргон/азот).Каждый из этих факторов играет уникальную роль в кинетике спекания, уплотнении и общем поведении материала.Например, более высокие температуры и более мелкие размеры частиц обычно повышают плотность, а выбор атмосферы может повлиять на окисление или загрязнение.Понимание и оптимизация этих переменных очень важны для достижения желаемых свойств материала, таких как прочность на разрыв, усталостная прочность при изгибе и энергия удара.
Объяснение ключевых моментов:
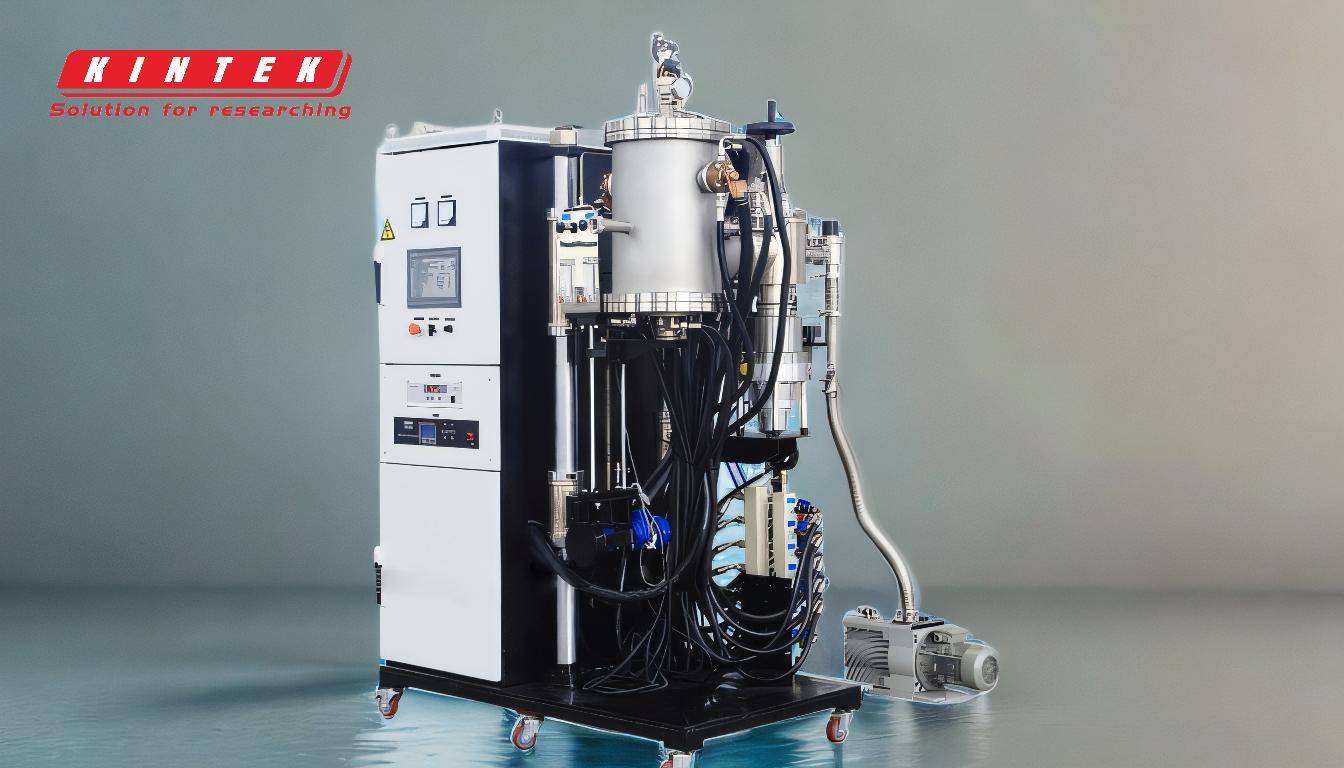
-
Температура:
- Температура является одной из наиболее важных переменных при спекании.Она напрямую влияет на кинетику спекания и конечные свойства материала.
- Более высокие температуры обычно ускоряют диффузию атомов, что приводит к лучшему сцеплению частиц и уплотнению.
- Однако слишком высокие температуры могут вызвать нежелательный рост зерен или плавление, что может нарушить целостность материала.
-
Скорость нагрева:
- Скорость нагрева определяет, как быстро материал достигает температуры спекания.
- Контролируемая скорость нагрева необходима для предотвращения теплового удара, который может привести к растрескиванию или неравномерному уплотнению.
- Более высокая скорость нагрева иногда повышает производительность, но при этом необходимо соизмерять ее с риском возникновения дефектов.
-
Применяемое давление:
- Давление усиливает перегруппировку частиц и помогает устранить пористость во время спекания.
- Более высокое давление может привести к более равномерному уплотнению и улучшению механических свойств.
- Для получения материалов высокой плотности часто используются методы спекания под давлением, такие как горячее прессование или искровое плазменное спекание.
-
Размер частиц:
- Меньшие размеры частиц обычно способствуют лучшему уплотнению из-за увеличения площади поверхности и более высокой движущей силы для спекания.
- Мелкие порошки могут приводить к более однородным микроструктурам и улучшать механические свойства.
- Однако слишком мелкие частицы могут агломерироваться, что требует осторожного обращения и обработки.
-
Состав:
- Химический состав материала влияет на его поведение при спекании и конечные свойства.
- Однородные составы, как правило, спекаются более равномерно, в то время как неоднородные составы могут приводить к неравномерному уплотнению или разделению фаз.
- Присутствие добавок или легирующих элементов также может влиять на кинетику спекания и характеристики материала.
-
Атмосфера спекания:
- Выбор атмосферы для спекания (например, воздух, вакуум или инертные газы, такие как аргон/азот) может существенно повлиять на конечные свойства материала.
- Инертная атмосфера предотвращает окисление и загрязнение, что особенно важно для реактивных материалов.
- Вакуумное спекание может помочь удалить летучие примеси и уменьшить пористость, но для этого может потребоваться специальное оборудование.
-
Скорость охлаждения:
- Скорость охлаждения после спекания влияет на микроструктуру и механические свойства материала.
- Контролируемое охлаждение помогает достичь желаемых фазовых превращений и минимизировать остаточные напряжения.
- Быстрое охлаждение может привести к созданию более мелкозернистой структуры, но при этом могут возникнуть термические напряжения.
-
Контроль жидкой фазы:
- В некоторых процессах спекания может образовываться жидкая фаза, которая может повысить плотность, но должна тщательно контролироваться.
- Избыток жидкой фазы может привести к ослаблению границ зерен или разделению фаз, что ухудшит свойства материала.
- Количество жидкой фазы часто оптимизируется в зависимости от желаемой микроструктуры и механических характеристик.
Тщательно контролируя эти переменные, производители могут адаптировать процесс спекания для достижения определенных свойств материала, таких как повышенная прочность на разрыв, усталостная прочность при изгибе и энергия удара.Каждая переменная взаимодействует с другими, поэтому при оптимизации процесса необходимо учитывать всю систему спекания.
Сводная таблица:
Переменная | Роль в спекании | Основные соображения |
---|---|---|
Температура | Влияет на кинетику спекания и плотность. | Более высокие температуры улучшают сцепление; при чрезмерных температурах возникает риск роста зерен или плавления. |
Скорость нагрева | Определяет скорость достижения температуры спекания | Контролируемая скорость предотвращает тепловой удар; более высокая скорость повышает производительность, но создает риск дефектов. |
Применяемое давление | Усиливает перегруппировку частиц и устранение пористости | Повышенное давление улучшает плотность; для получения результатов высокой плотности используются такие методы, как горячее прессование. |
Размер частиц | Более мелкие частицы способствуют лучшему уплотнению | Тонкие порошки улучшают микроструктуру; чрезмерная тонкость может привести к агломерации. |
Состав | Влияет на поведение при спекании и конечные свойства | Однородные композиции спекаются равномерно; добавки или легирующие вещества влияют на характеристики. |
Атмосфера спекания | Влияет на окисление, загрязнение и пористость. | Инертные газы предотвращают окисление; вакуум уменьшает количество примесей, но требует специального оборудования. |
Скорость охлаждения | Влияет на микроструктуру и механические свойства | Контролируемое охлаждение сводит к минимуму напряжения; быстрое охлаждение может улучшить структуру зерна, но создает напряжения. |
Контроль жидкой фазы | Повышает плотность, но должна контролироваться | Избыток жидкой фазы может ослабить границы зерен; оптимизация является ключевым фактором для получения желаемых свойств. |
Оптимизируйте процесс спекания для получения превосходных свойств материала. свяжитесь с нашими специалистами сегодня !