Вакуумное литье — это производственный процесс, используемый для создания высококачественных детализированных деталей путем заливки жидкого материала в форму в условиях вакуума. Этот процесс особенно полезен для производства небольших партий деталей сложной конструкции, поскольку он сводит к минимуму количество пузырьков воздуха и обеспечивает высокий уровень детализации. Процесс вакуумного литья обычно включает в себя несколько ключевых этапов, включая подготовку формы, смешивание материалов, применение вакуума, заливку, отверждение и извлечение из формы. Каждый шаг необходимо тщательно контролировать для достижения желаемых результатов. Ниже мы разбиваем процесс на подробные этапы и объясняем критические аспекты каждого этапа.
Объяснение ключевых моментов:
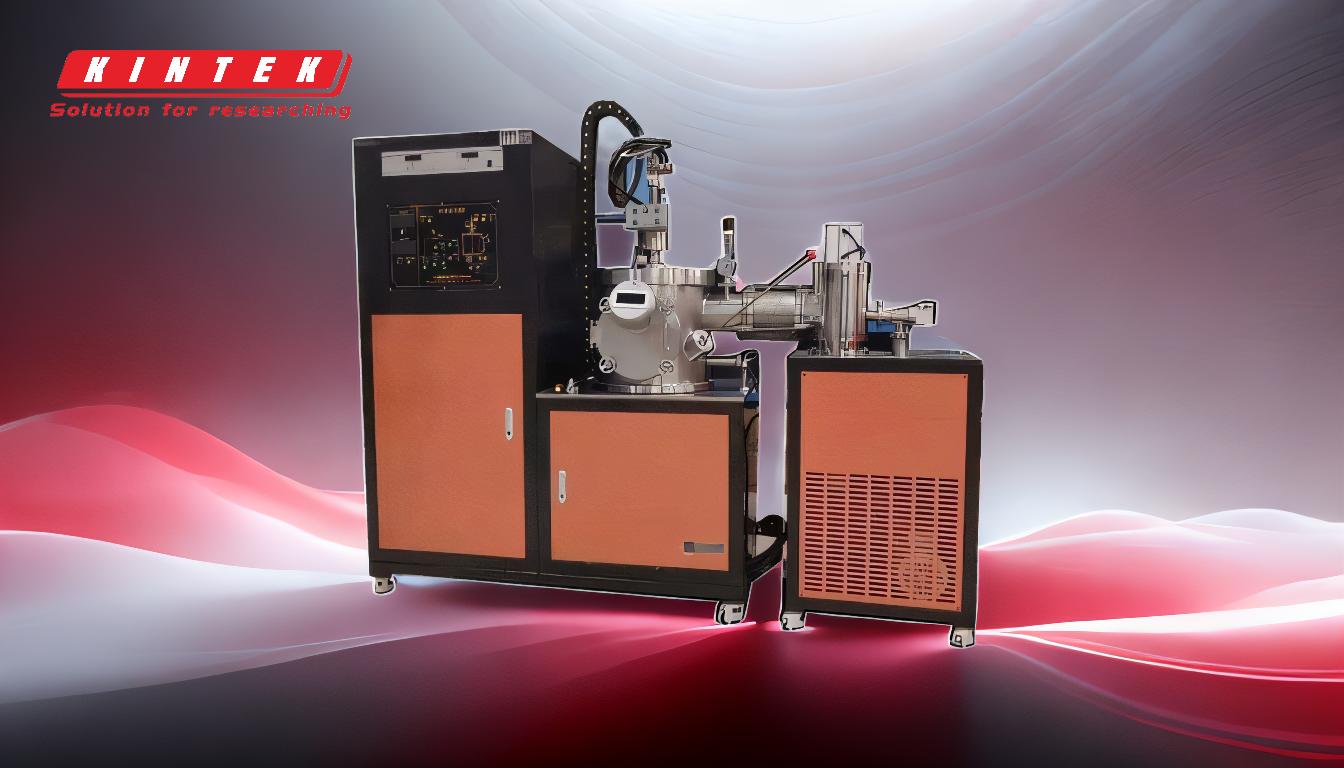
-
Подготовка формы:
- Первым этапом вакуумного литья является подготовка формы. Это включает в себя создание мастер-модели, обычно с использованием 3D-печати или обработки на станке с ЧПУ, которая затем используется для изготовления силиконовой формы.
- Силиконовая форма создается путем заливки мастер-модели жидким силиконом и ее затвердевания. После затвердевания форму разрезают, чтобы удалить мастер-модель, оставляя полость, соответствующую форме желаемой детали.
- Перед использованием форму необходимо очистить и проверить на наличие дефектов, чтобы гарантировать качество конечной детали.
-
Смешивание материалов:
- Материал, используемый для вакуумного литья, обычно представляет собой двухкомпонентную полиуретановую смолу. Смола и отвердитель смешиваются в точных пропорциях, чтобы обеспечить правильное отверждение и свойства материала.
- Смешивание производится под вакуумом, чтобы удалить из смолы пузырьки воздуха, которые в противном случае могли бы привести к дефектам конечной детали.
- Затем смешанная смола дополнительно дегазируется в вакуумной камере, чтобы гарантировать отсутствие захваченного воздуха.
-
Вакуумное применение:
- Форма помещается в вакуумную камеру, и камера герметизируется. Вакуумный насос используется для удаления воздуха из камеры, создавая среду низкого давления.
- Вакуум помогает втягивать жидкую смолу в полости формы, обеспечивая полное заполнение даже сложных деталей.
- Вакуум также помогает удалить оставшиеся пузырьки воздуха в смоле, в результате чего поверхность становится гладкой и без дефектов.
-
Заливка и отверждение:
- После применения вакуума дегазированная смола заливается в форму. Вакуум обеспечивает равномерное растекание смолы и заполнение всех частей формы.
- После заливки форму оставляют застывать. Время отверждения зависит от используемой смолы и размера детали. Некоторым смолам для отверждения требуется тепло, а другие отверждаются при комнатной температуре.
- В процессе отверждения смола затвердевает и принимает форму формы. Важно следить за процессом отверждения, чтобы гарантировать, что деталь достигнет желаемых механических свойств.
-
Демонтаж и отделка:
- После полного затвердевания смолы форму открывают и осторожно вынимают деталь. Извлечение из формы следует производить осторожно, чтобы не повредить деталь или форму.
- Деталь может потребовать последующей обработки, такой как обрезка лишнего материала, шлифовка или покраска, чтобы добиться окончательного желаемого внешнего вида и функциональности.
- Силиконовую форму часто можно использовать повторно несколько раз, что делает вакуумное литье экономически эффективным методом мелкосерийного производства.
-
Оборудование и соображения безопасности:
- Вакуумное литье требует специального оборудования, включая вакуумную камеру, вакуумный насос и смесительные инструменты. Правильное обслуживание этого оборудования имеет важное значение для обеспечения стабильных результатов.
- Необходимо соблюдать меры безопасности при работе со смолами и вакуумным оборудованием. Это включает в себя ношение защитной одежды, обеспечение надлежащей вентиляции и соблюдение рекомендаций производителя по обращению с материалами.
-
Преимущества вакуумного литья:
- Высокий уровень детализации и обработки поверхности.
- Возможность производства небольших партий деталей с минимальными затратами.
- Универсальность в выборе материалов: широкий ассортимент смол, имитирующих различные свойства (например, АБС-пластик, резиноподобные или прозрачные материалы).
- Многоразовые формы снижают общие производственные затраты при небольших тиражах.
-
Ограничения вакуумного литья:
- Не подходит для крупномасштабного производства из-за трудоемкости процесса.
- Ограничено долговечностью силиконовых форм, которые могут деградировать после многократного использования.
- Свойства материала литых деталей могут не соответствовать свойствам деталей, отлитых под давлением, в зависимости от используемой смолы.
Если следовать этим шагам и соображениям, вакуумное литье может стать высокоэффективным методом производства детализированных высококачественных деталей. Этот процесс требует пристального внимания к деталям и надлежащего оборудования, но результаты зачастую оправдывают затраченные усилия, особенно при создании прототипов или мелкосерийном производстве.
Сводная таблица:
Шаг | Ключевые детали |
---|---|
Подготовка формы | Создайте мастер-модель (3D-печать/ЧПУ), изготовьте силиконовую форму, очистите и проверьте. |
Смешивание материалов | Смешайте двухкомпонентную полиуретановую смолу в вакууме, чтобы удалить пузырьки воздуха. |
Вакуумное применение | Поместите форму в вакуумную камеру, чтобы смола заполнила сложные детали. |
Заливка и отверждение | Залейте смолу в форму, отверждайте в контролируемых условиях для достижения оптимальных результатов. |
Демонтаж/Отделка | Аккуратно снимите деталь, выполните постобработку (обрезку, шлифовку, покраску). |
Преимущества | Высокая детализация, экономичность небольших партий, универсальные материалы, многоразовые формы. |
Ограничения | Не для крупносерийного производства, долговечности пресс-формы, ограничений свойств материала. |
Готовы производить высококачественные детали методом вакуумного литья? Свяжитесь с нашими экспертами сегодня чтобы начать!