Уменьшение пористости в процессе спекания - важнейшая задача при обработке материалов для получения более плотных, прочных и надежных изделий.Пористость спеченного материала зависит от нескольких факторов, включая исходную пористость зеленого компакта, температуру спекания, время спекания, атмосферу, размер частиц и приложенное давление.Оптимизируя эти переменные, можно минимизировать пористость и улучшить механические и физические свойства материала.Основные стратегии включают контроль пористости исходного зеленого компакта, выбор подходящих температур и времени спекания, использование частиц меньшего размера и применение внешнего давления во время спекания.Кроме того, атмосфера спекания и скорость нагрева играют важную роль в устранении пор и уплотнении.
Ключевые моменты:
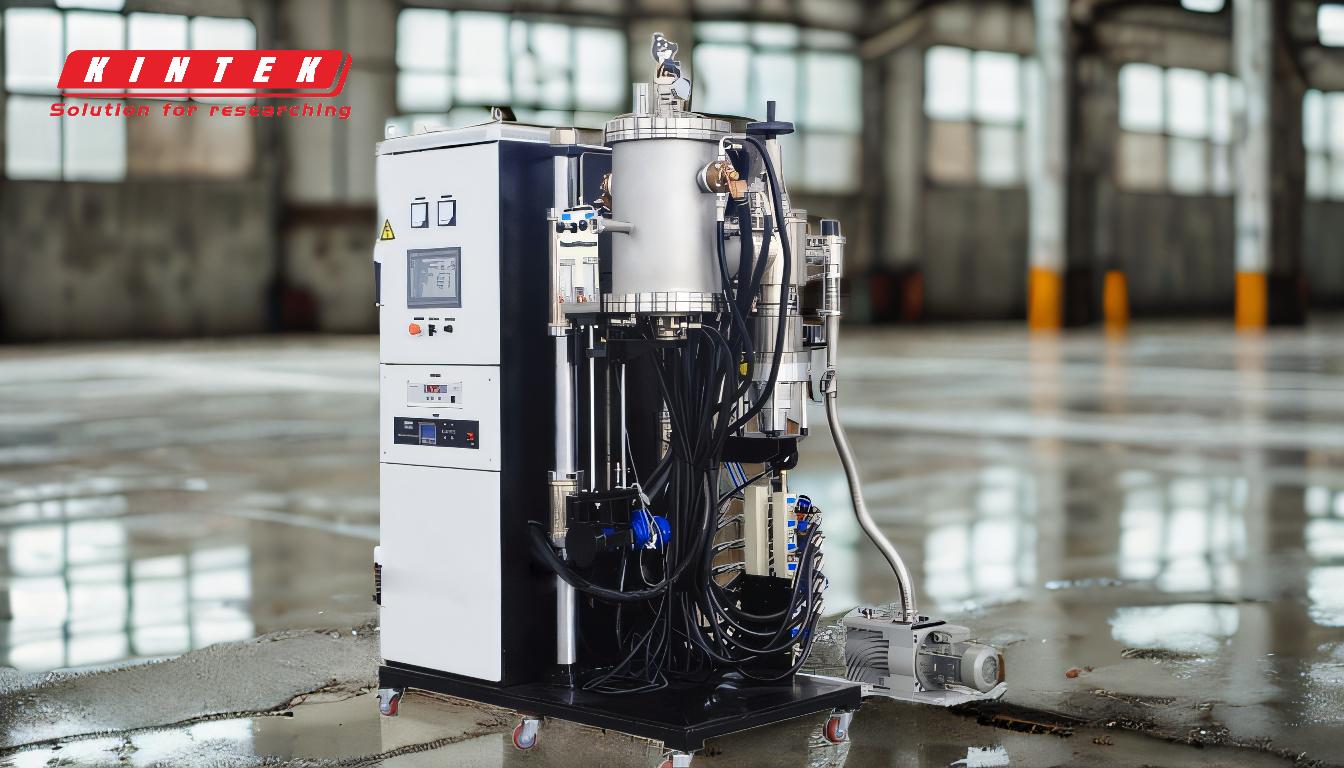
-
Контроль начальной пористости зеленого компакта:
- Начальная пористость зеленого компакта (неспеченного материала) является критическим фактором для определения конечной пористости после спекания.Более низкая начальная пористость обычно приводит к более плотному конечному продукту.
- Чтобы уменьшить начальную пористость, обеспечьте правильную технику уплотнения, например, используйте более высокое давление уплотнения или оптимизируйте распределение частиц по размерам в зеленом компакте.Равномерная упаковка частиц минимизирует крупные пустоты и способствует лучшему уплотнению во время спекания.
-
Оптимизация температуры спекания:
- Температура спекания существенно влияет на уменьшение пористости.Более высокие температуры усиливают атомную диффузию, что способствует устранению пор за счет сцепления частиц и роста зерен.
- Однако слишком высокие температуры могут привести к нежелательному росту зерен или распаду материала.Поэтому очень важно определить оптимальную температуру спекания для конкретного материала, чтобы сбалансировать уменьшение пористости и целостность материала.
-
Регулировка времени спекания:
- Более длительное время спекания позволяет увеличить время ликвидации пор за счет таких механизмов, как граничная и решеточная диффузия.Это особенно важно для материалов с высокой начальной пористостью или материалов, требующих твердотельной диффузии, таких как чистая оксидная керамика.
- Однако слишком длительное время спекания может привести к переспеканию, что может ухудшить свойства материала.Время спекания должно быть оптимизировано в зависимости от материала и желаемой конечной пористости.
-
Используйте частицы меньшего размера:
- Более мелкие частицы имеют более высокое отношение площади поверхности к объему, что увеличивает движущую силу спекания и повышает плотность.Меньшие частицы также сокращают диффузионные расстояния, что делает ликвидацию пор более эффективной.
- Обеспечьте равномерное распределение частиц по размерам, чтобы избежать локальных проблем с уплотнением и способствовать однородному спеканию.
-
Применить внешнее давление (горячее прессование или горячее изостатическое прессование):
- Приложение давления во время спекания (например, горячее прессование или горячее изостатическое прессование) может значительно уменьшить пористость за счет усиления перегруппировки частиц и устранения пустот.Спекание под давлением особенно эффективно для материалов, которые трудно уплотнить с помощью обычных методов спекания.
- Этот метод сокращает время спекания и снижает необходимую температуру спекания, что делает его мощным инструментом для получения материалов с низкой пористостью.
-
Управление атмосферой спекания:
- Атмосфера спекания (например, воздух, вакуум или инертные газы, такие как аргон или азот) влияет на кинетику спекания и конечную пористость.Например, вакуум или инертная атмосфера могут предотвратить окисление и способствовать лучшему уплотнению некоторых материалов.
- Выбор атмосферы зависит от реакционной способности материала и желаемых свойств конечного продукта.
-
Оптимизация скорости нагрева:
- Скорость нагрева влияет на процесс уплотнения.Более медленная скорость нагрева обеспечивает более равномерное распределение температуры и лучшее устранение пор, в то время как более высокая скорость нагрева может привести к возникновению тепловых градиентов и неполному уплотнению.
- Оптимальная скорость нагрева зависит от материала и используемого оборудования для спекания.
-
Улучшение состава и однородности:
- Однородный состав с минимальным количеством примесей способствует лучшему спеканию и уменьшает пористость.Примеси могут служить барьерами для диффузии и препятствовать устранению пор.
- Для улучшения спекания и уменьшения пористости иногда используются добавки или легирующие вещества.
Тщательно контролируя эти факторы, можно минимизировать пористость во время спекания и получить материалы с превосходными механическими, тепловыми и электрическими свойствами.Для достижения желаемых результатов в каждой материальной системе могут потребоваться особые настройки, но описанные выше принципы обеспечивают прочную основу для уменьшения пористости в спеченных материалах.
Сводная таблица:
Фактор | Влияние на уменьшение пористости |
---|---|
Начальная пористость | Более низкая начальная пористость в зеленом компакте приводит к повышению плотности конечного продукта. |
Температура спекания | Более высокие температуры усиливают атомную диффузию, но при этом необходимо избегать чрезмерного роста зерен. |
Время спекания | Более длительное время позволяет устранить поры, но избежать чрезмерного спекания. |
Размер частиц | Более мелкие частицы увеличивают плотность и уменьшают расстояние диффузии. |
Внешнее давление | Спекание под давлением (например, горячее прессование) значительно снижает пористость. |
Атмосфера спекания | Вакуум или инертные газы предотвращают окисление и способствуют уплотнению. |
Скорость нагрева | Более медленная скорость обеспечивает равномерное распределение температуры и лучшее устранение пор. |
Состав и однородность | Однородные материалы с минимальным количеством примесей улучшают спекание и уменьшают пористость. |
Готовы оптимизировать процесс спекания для получения более плотных и прочных материалов? Свяжитесь с нашими специалистами сегодня для получения индивидуальных решений!