Закалка - это специализированный процесс термообработки, используемый для повышения твердости внешней поверхности металлической детали при сохранении более мягкой и вязкой сердцевины.Этот процесс особенно полезен для деталей, которые требуют высокой износостойкости на поверхности, но должны сохранять вязкость и гибкость в сердцевине, таких как шестерни, валы и подшипники.Поэтапный процесс закалки включает в себя несколько стадий, каждая из которых важна для достижения желаемых свойств металла.
Объяснение ключевых моментов:
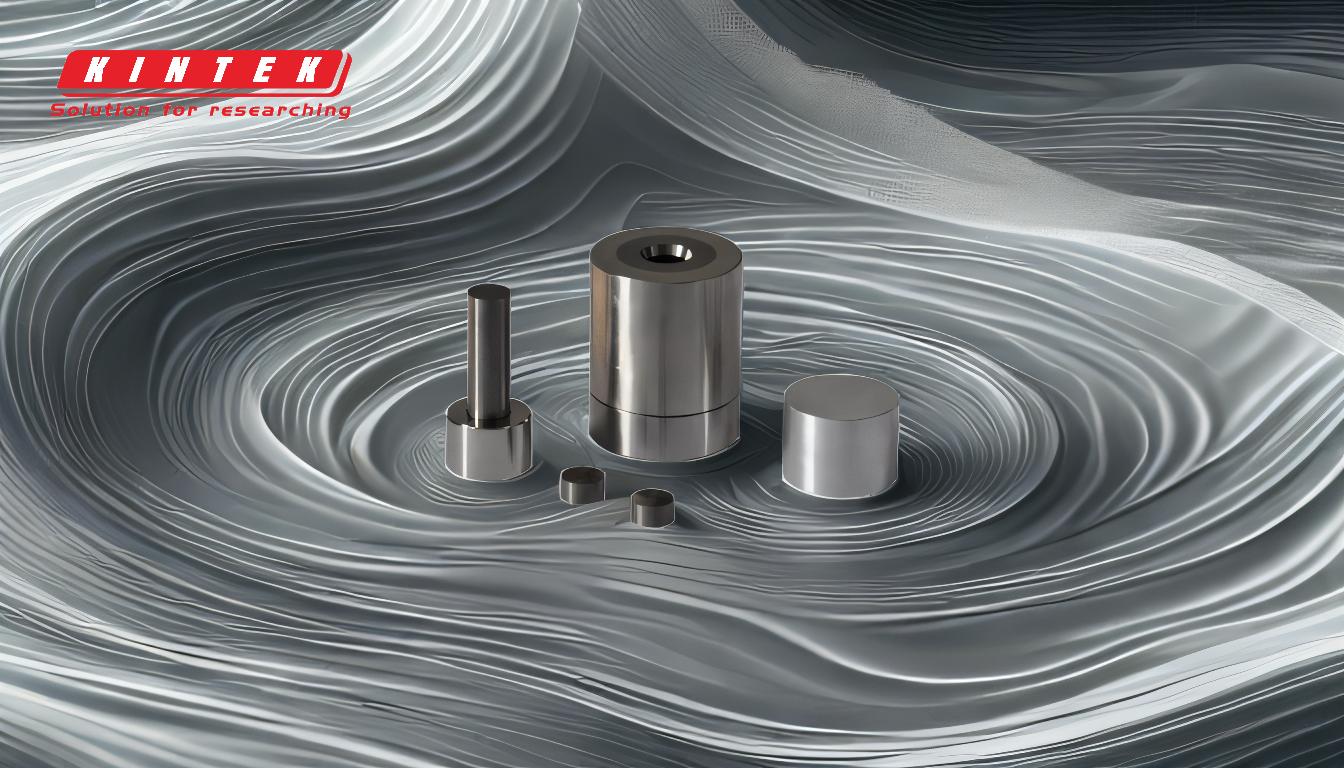
-
Выбор материала:
- Первым шагом в закалке корпуса является выбор подходящего материала.Обычно выбирают низкоуглеродистые стали или сплавы железа, поскольку они могут эффективно поглощать углерод или азот в процессе закалки.Эти материалы позволяют добиться значительной разницы в твердости между поверхностью и сердцевиной.
-
Очистка и подготовка поверхности:
- Перед началом процесса закалки металлическая деталь должна быть тщательно очищена от грязи, масла и окислов.Это обеспечит равномерное проникновение закалочных агентов (углерода или азота) в поверхность.Подготовка поверхности может включать механическую (например, пескоструйную) или химическую (например, с использованием растворителей или кислот) очистку.
-
Нагрев металла:
- Металл нагревается до определенной температуры, обычно от 850 до 950°C (1562-1742°F), в зависимости от материала и желаемой твердости.Этот этап очень важен, поскольку позволяет металлу достичь состояния, в котором он может эффективно поглощать углерод или азот.Процесс нагрева обычно проводится в контролируемой среде, например в печи, для обеспечения равномерного распределения температуры.
-
Введение упрочняющих агентов (науглероживание или азотирование):
-
После того как металл достигает нужной температуры, его подвергают воздействию среды, богатой углеродом или азотом.Этот этап известен как науглероживание или азотирование, соответственно.
- Науглероживание:В этом процессе металл помещается в атмосферу, богатую углеродом, например, в газ или жидкость, содержащую углеродные соединения.Углерод диффундирует в поверхность металла, увеличивая содержание углерода и, соответственно, твердость.
- Азотирование:В этом процессе металл подвергается воздействию богатой азотом среды, часто в виде газообразного аммиака.Атомы азота диффундируют в поверхность, образуя твердые нитриды, которые повышают твердость поверхности.
-
После того как металл достигает нужной температуры, его подвергают воздействию среды, богатой углеродом или азотом.Этот этап известен как науглероживание или азотирование, соответственно.
-
Замачивание:
- После введения закалочных агентов металл выдерживается при высокой температуре в течение определенного времени, называемого временем выдержки.Это позволяет углероду или азоту проникнуть глубже в металл, создавая закаленный корпус нужной толщины.Время выдержки может составлять от нескольких минут до нескольких часов, в зависимости от материала и требуемой глубины корпуса.
-
Закалка:
- После завершения периода выдержки металл быстро охлаждают, или закаливают, чтобы зафиксировать закаленную поверхность.Закалка обычно осуществляется путем погружения металла в охлаждающую среду, такую как вода, масло или воздух.Быстрое охлаждение вызывает значительную закалку поверхности, в то время как сердцевина остается относительно мягкой и вязкой.
-
Отпуск:
- После закалки металл может быть подвергнут отпуску для снижения хрупкости и повышения вязкости.Отпуск подразумевает повторный нагрев металла до более низкой температуры (обычно от 150 до 650 °C или от 302 до 1202 °F) и последующее медленное охлаждение.Этот этап помогает снять внутренние напряжения и достичь баланса между твердостью и вязкостью.
-
Окончательная отделка:
- Заключительным этапом процесса закалки является финишная обработка металлической детали.Она может включать шлифовку, полировку или нанесение покрытия для достижения требуемой чистоты поверхности и точности размеров.Финишная обработка также обеспечивает соответствие детали требуемым техническим характеристикам для ее применения по назначению.
Следуя этим этапам, закалка позволяет значительно повысить долговечность и износостойкость металлических деталей, сохраняя при этом их структурную целостность.Это делает ее незаменимой в отраслях, где требуются высокопроизводительные материалы.
Сводная таблица:
Шаг | Описание |
---|---|
1.Выбор материала | Выбирайте низкоуглеродистые стали или сплавы железа для эффективного поглощения углерода/азота. |
2.Очистка и подготовка | Удалите грязь, масло или окислы, чтобы обеспечить равномерное проникновение упрочняющих веществ. |
3.Нагрев металла | Нагрейте до 850°C-950°C (1562°F-1742°F) для оптимального поглощения углерода/азота. |
4.Упрочняющие агенты | Ввод углерода (науглероживание) или азота (азотирование) для повышения твердости поверхности. |
5.Замачивание | Выдержите при высокой температуре, чтобы обеспечить диффузию упрочняющих веществ в металл. |
6.Закалка | Быстрое охлаждение для фиксации закаленной поверхности при сохранении вязкости сердцевины. |
7.Отпуск | Повторный нагрев для снижения хрупкости и повышения вязкости. |
8.Окончательная отделка | Шлифовка, полировка или нанесение покрытия для достижения желаемой чистоты и точности поверхности. |
Нужна помощь в закалке металлических деталей? Свяжитесь с нашими специалистами сегодня для получения индивидуальных решений!