Вакуумная термообработка — это специализированный процесс, используемый для закалки металлов в контролируемой среде, при котором воздух удаляется из герметичной камеры с помощью вакуумного насоса. Этот метод гарантирует, что металл не подвергается окислению, обезуглероживанию или загрязнению, что приводит к превосходным механическим свойствам и высококачественным компонентам. Процесс предполагает точный контроль параметров нагрева и охлаждения, равномерное распределение температуры и минимальное искажение сложной геометрии. Вакуумная термообработка включает в себя различные методы, такие как вакуумное спекание, вакуумная пайка, вакуумная закалка и вакуумный отжиг, каждый из которых адаптирован к конкретному применению и требованиям к материалу. Преимущества этого метода включают улучшенную твердость поверхности, износостойкость и стабильные, повторяемые результаты, что делает его предпочтительным выбором для отраслей, требующих высокой точности и качества.
Объяснение ключевых моментов:
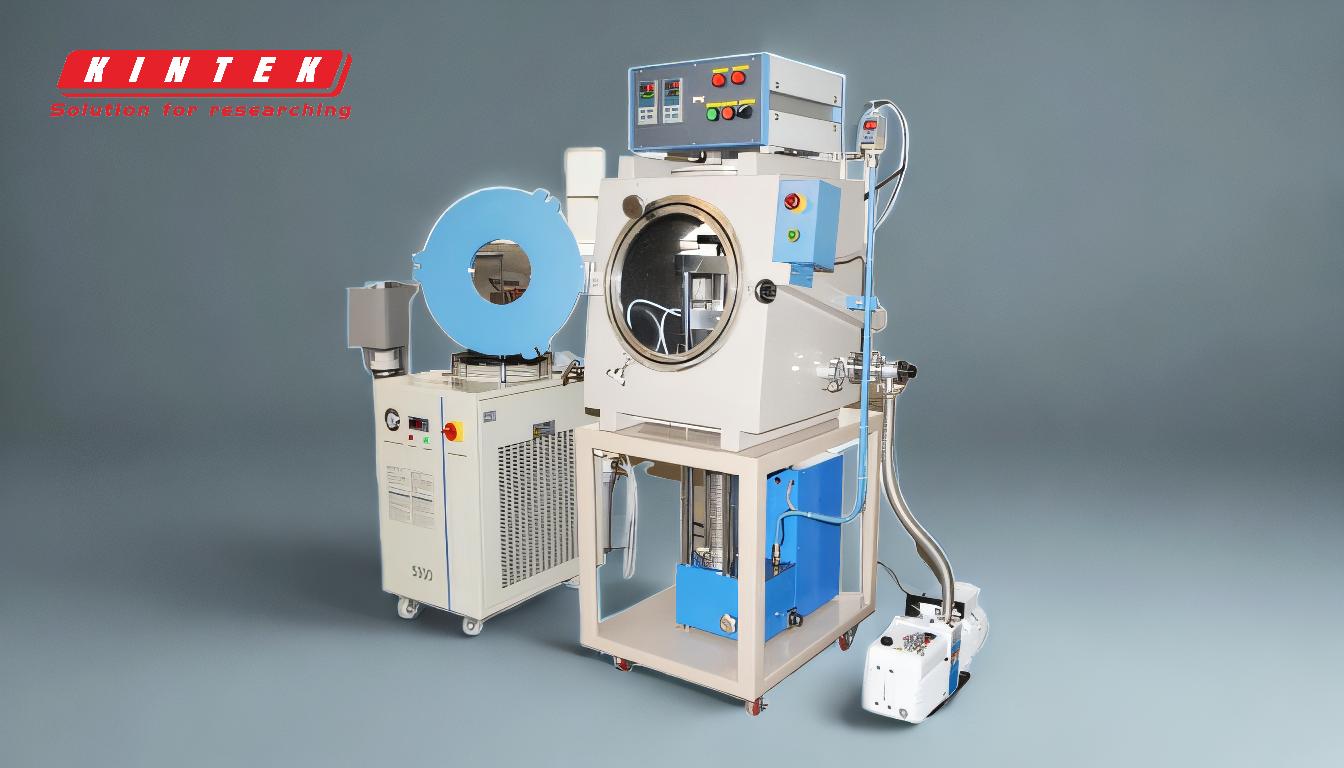
-
Принцип вакуумной термообработки:
- Вакуумная термообработка предполагает нагрев металлов в герметичной камере, из которой удаляется воздух с помощью вакуумного насоса. Это создает среду, свободную от кислорода и других химически активных газов, предотвращая окисление, обезуглероживание и загрязнение.
- Отсутствие воздуха гарантирует, что поверхность металла останется чистой и свободной от загрязнений, что приводит к улучшению механических свойств и улучшению качества поверхности.
-
Виды вакуумной термообработки:
- Вакуумное спекание: процесс, при котором порошкообразные металлы нагреваются ниже точки плавления с образованием твердой массы. Это обычно используется при производстве компонентов высокой плотности.
- Вакуумная пайка: соединяет два или более металлов путем нагревания их чуть ниже точки плавления и использования присадочного металла для создания гладкого соединения. Этот метод идеален для создания прочных, герметичных соединений в сложных узлах.
- Вакуумная закалка: Включает быстрое охлаждение нагретого металла для достижения высокой твердости и прочности. Вакуумная среда предотвращает окисление поверхности, обеспечивая чистую и однородную поверхность.
- Вакуумный отжиг: процесс, используемый для смягчения металлов, улучшения пластичности и снятия внутренних напряжений. Вакуумная среда предотвращает загрязнение поверхности, обеспечивая высококачественную отделку.
- Вакуумная закалка: Следует за закалкой для уменьшения хрупкости и повышения ударной вязкости. Вакуумная среда обеспечивает стабильные результаты и предотвращает деградацию поверхности.
-
Преимущества вакуумной термообработки:
- Расширенный контроль: Точный контроль параметров нагрева и охлаждения обеспечивает равномерное распределение температуры и минимальные искажения.
- Улучшенные свойства поверхности: Отсутствие окисления и загрязнений приводит к улучшению твердости поверхности, износостойкости и общих механических свойств.
- Стабильные результаты: Контролируемая среда обеспечивает стабильные и повторяемые результаты, что делает ее идеальной для высокоточных применений.
- Энергоэффективность: Вакуумная термообработка является энергоэффективной и экологически чистой, поскольку исключает необходимость создания защитной атмосферы или химической обработки.
-
Применение вакуумной термообработки:
- Аэрокосмическая промышленность: Используется для обработки критических компонентов, таких как лопатки турбин, детали двигателей и конструктивные элементы, требующие высокой прочности и устойчивости к износу.
- Медицинское оборудование: Обеспечивает производство высококачественных хирургических инструментов, имплантатов и других медицинских компонентов с превосходными механическими свойствами.
- Автомобильная промышленность: Применяется при производстве шестерен, валов и других компонентов, требующих высокой точности и долговечности.
- Производство инструментов и штампов: Повышает производительность и срок службы режущих инструментов, форм и штампов за счет повышения твердости и износостойкости.
-
Этапы процесса вакуумной термообработки:
- Загрузка: Металлические компоненты размещаются внутри вакуумной камеры.
- Эвакуация: Воздух удаляется из камеры с помощью вакуумного насоса для создания контролируемой среды.
- Обогрев: Компоненты нагреваются до желаемой температуры, обеспечивая равномерное распределение тепла.
- Холдинг: Температура поддерживается в течение определенного периода времени для достижения желаемых металлургических изменений.
- Охлаждение: Компоненты быстро или медленно охлаждаются, в зависимости от желаемых свойств.
- Разгрузка: Обработанные компоненты извлекаются из камеры и проверяются на качество.
-
Сравнение с другими методами термообработки:
- Индукционная термообработка: В отличие от вакуумной термообработки, индукционная термообработка использует электромагнитную индукцию для нагрева поверхности металла. Хотя этот процесс быстрее и более локализован, он не обеспечивает такого же уровня контроля и единообразия, как вакуумная термообработка.
- Атмосферная термообработка: Термическая обработка в открытой атмосфере может привести к окислению и загрязнению, что приводит к ухудшению качества поверхности и механических свойств по сравнению с вакуумной термообработкой.
В заключение, вакуумная термообработка Это высокоэффективный метод улучшения механических свойств металлов путем создания чистой и контролируемой среды. Его способность предотвращать окисление, обезуглероживание и загрязнение в сочетании с точным контролем нагрева и охлаждения делает его важным процессом в отраслях, требующих высокой точности и качества.
Сводная таблица:
Аспект | Подробности |
---|---|
Принцип | Нагрев металлов в вакуумной камере для предотвращения окисления и загрязнения. |
Ключевые преимущества | Улучшенная твердость поверхности, износостойкость и стабильные результаты. |
Общие методы | Вакуумное спекание, пайка, закалка, отжиг и отпуск. |
Приложения | Аэрокосмическая промышленность, медицинское оборудование, автомобилестроение и производство инструментов. |
Этапы процесса | Погрузка, эвакуация, нагрев, выдержка, охлаждение и разгрузка. |
Узнайте, как вакуумная термообработка может улучшить качество ваших металлических компонентов. свяжитесь с нашими экспертами сегодня !