Нормальная температура спекания зависит от обрабатываемого материала и желаемых свойств конечного продукта. Для диоксида циркония спекание обычно происходит при температуре ближе к 1 500°C, хотя превращение из моноклинной в политетрагональную структуру происходит при температуре от 1 100°C до 1 200°C. При более высоких температурах цирконий становится плотнее, часто достигая 99 % от теоретической максимальной плотности. Для керамических композитов температура спекания колеблется между 900°C и 1250°C. В стоматологии печи для спекания обычно работают при высоких температурах, как правило, от 1200°C до 1400°C. Процесс спекания очень важен, и такие факторы, как скорость темпа, постоянство температуры в течение времени выдержки и скорость охлаждения, имеют большое значение для достижения оптимальных результатов.
Ключевые моменты объяснены:
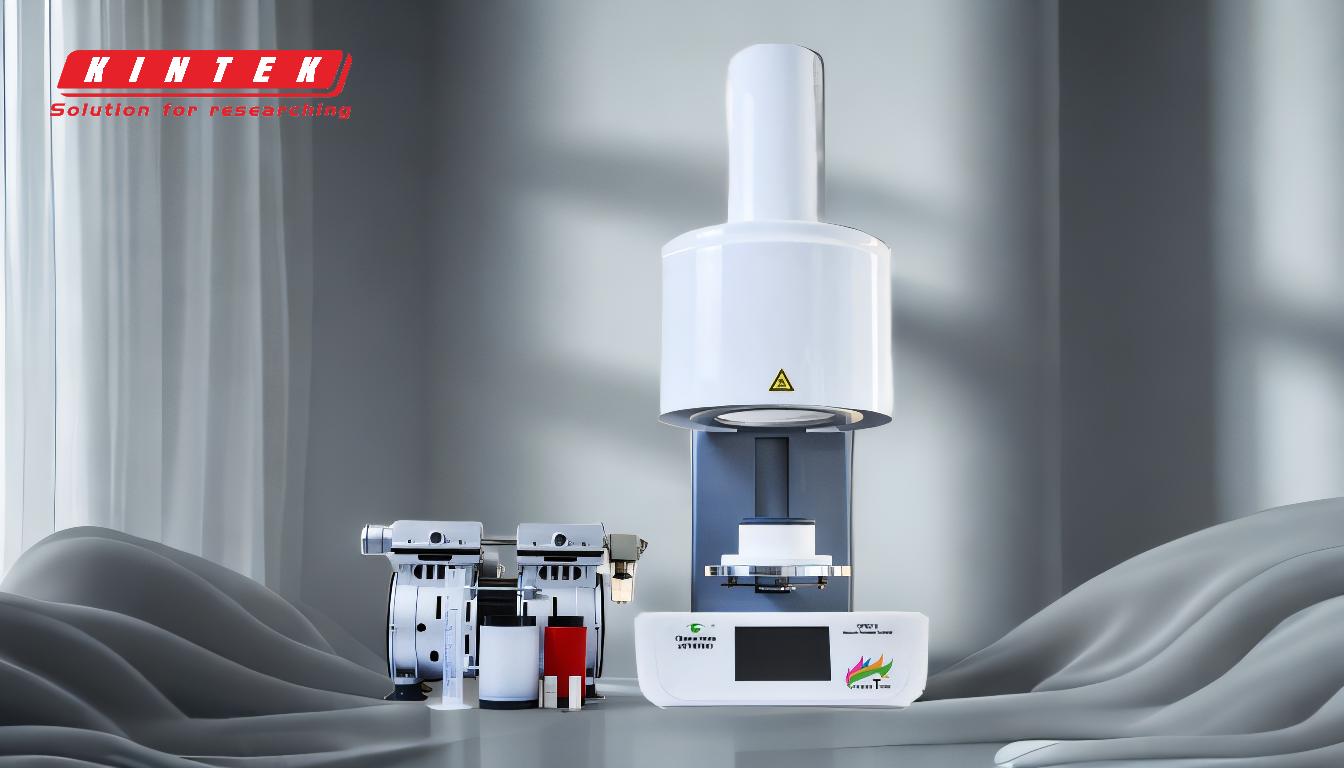
-
Диапазон температур для спекания диоксида циркония:
- Спекание диоксида циркония обычно происходит при температурах, близких к 1 500°C.
- Превращение моноклинной структуры в политетрагональную происходит при температуре от 1100 до 1200 °C.
- Более высокие температуры спекания приводят к повышению плотности диоксида циркония, часто достигающей 99% от теоретической максимальной плотности.
-
Температурный диапазон для керамических композитов:
- Спекание керамических композитов проводится при температурах от 900°C (1650°F) до 1250°C (2300°F).
- Этот диапазон обеспечивает достижение требуемых механических свойств и плотности материала.
-
Печи для спекания зубов:
- Печи для спекания стоматологических материалов обычно требуют высоких температур, как правило, от 1200°C до 1400°C.
- Эти температуры необходимы для достижения требуемой прочности и эстетики зубных протезов.
-
Общий процесс спекания:
- Процесс спекания происходит при повышенных температурах, обычно выше 1800°F (982°C), в зависимости от области применения.
- Процесс может происходить в инертной, восстановительной или окислительной атмосфере, в зависимости от материала и желаемых характеристик.
-
Критические факторы при спекании:
- Скорость нарастания: Скорость повышения температуры от 900°C до верхней температуры является критической.
- Постоянство температуры: Поддержание постоянной температуры в течение времени выдержки необходимо для равномерного спекания.
- Скорость охлаждения: Скорость охлаждения до температуры около 900°C имеет решающее значение для предотвращения дефектов и обеспечения целостности материала.
-
Стандартные печи для спекания:
- Стандартные печи для спекания могут работать при максимальной температуре от 1400°C до 1700°C.
- Эти печи предназначены для работы при высоких температурах, необходимых для спекания различных материалов.
-
Спекание в контролируемой атмосфере:
- Спекание часто проводится в печах непрерывного действия при контролируемой скорости и в атмосфере с контролируемым химическим составом.
- Температура обычно составляет от 750°C до 1300°C, в зависимости от материала и желаемых характеристик.
Понимая эти ключевые моменты, можно лучше оценить сложность и критические факторы процесса спекания, обеспечивающие производство высококачественных материалов с требуемыми свойствами.
Сводная таблица:
Материал/Применение | Диапазон температур (°C) | Основные характеристики |
---|---|---|
Спекание диоксида циркония | ~1,500°C | Более плотный диоксид циркония, ~99% теоретической плотности |
Керамические композиты | 900°C - 1 250°C | Желаемые механические свойства и плотность |
Печи для спекания зубов | 1 200 °C - 1 400 °C | Необходимая прочность и эстетика для зубных реставраций |
Общий процесс спекания | >982°C (1 800°F) | Инертная, восстановительная или окислительная атмосфера |
Критические факторы | Скорость нарастания, консистенция, скорость охлаждения | Обеспечивает равномерное спекание и целостность материала |
Стандартные печи для спекания | 1 400 °C - 1 700 °C | Работает при высоких температурах для различных материалов |
Контролируемая атмосфера | 750°C - 1 300°C | Контролируемая скорость и химический состав |
Нужна помощь в оптимизации процесса спекания? Свяжитесь с нашими экспертами сегодня для индивидуальных решений!