Искровое плазменное спекание (SPS) - это передовая технология спекания, которая обладает значительными преимуществами по сравнению с традиционными методами, особенно для полимеров и других материалов.Он сочетает в себе активацию плазмой, горячее прессование и резистивный нагрев для достижения быстрого спекания при более низких температурах, сохраняя микроструктуру и улучшая свойства материала.Этот метод энергоэффективен, экономит время и позволяет получать материалы с однородным зерном, высокой плотностью и отличными механическими свойствами.SPS широко используется для спекания металлов, керамики и композитов, что делает его ценным инструментом в исследованиях и производстве современных материалов.
Объяснение ключевых моментов:
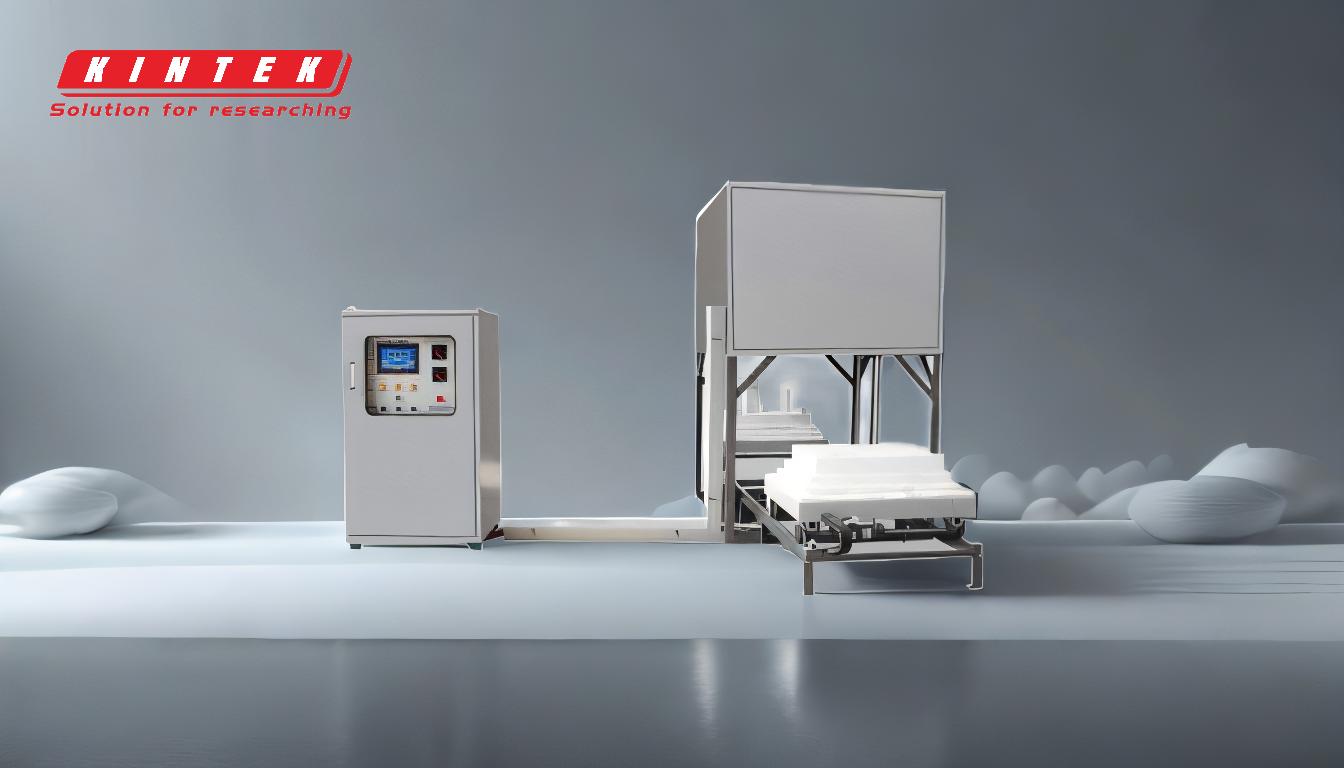
-
Что такое искровое плазменное спекание (SPS)?
- SPS - это современная технология спекания, объединяющая плазменную активацию, горячее прессование и резистивный нагрев.В ней используется постоянное импульсное напряжение для выделения тепла Джоуля, вызывающего пластическую деформацию и разряд между частицами порошка.Эта уникальная комбинация механизмов позволяет быстро спекать материалы при более низких температурах по сравнению с традиционными методами.
-
Преимущества SPS для полимеров и других материалов:
- Высокая скорость нагрева: SPS обеспечивает быстрый нагрев, значительно сокращая время, необходимое для спекания.
- Более низкая температура спекания: Процесс протекает при более низких температурах, что особенно полезно для термочувствительных материалов, таких как полимеры.
- Равномерный нагрев: Обеспечивает стабильные свойства материала по всему спеченному телу.
- Энергоэффективность: SPS потребляет меньше энергии благодаря сокращению времени обработки и более низким температурам.
- Улучшенные свойства материалов: Полученные в результате спекания материалы имеют мелкозернистую, однородную структуру, высокую плотность и улучшенные механические свойства.
-
Механизмы, участвующие в SPS:
- Джоулево нагревание: Основной источник тепла в SPS, возникающий за счет сопротивления материала электрическому току.
- Пластическая деформация: Давление, приложенное во время спекания, заставляет частицы деформироваться и более эффективно скрепляться.
- Разряд между частицами: Электрический разряд между частицами помогает активировать их поверхности, способствуя лучшему сцеплению и уплотнению.
-
Области применения SPS:
- Металлы и керамика: SPS широко используется для спекания этих материалов, позволяя получать высокоплотные, мелкозернистые изделия.
- Композитные материалы: Эффективны для создания композитов с улучшенными свойствами.
- Наноматериалы: SPS особенно полезна для получения наноматериалов с сохранением их утонченной микроструктуры.
- Объемные аморфные сплавы и градиентные функциональные материалы: Эти передовые материалы выигрывают от точного контроля и быстрой обработки SPS.
-
Преимущества спекания полимеров:
- Сохранение микроструктуры: SPS позволяет консолидировать полимерные порошки при более низких температурах и за более короткое время, сохраняя микроструктуру, достигнутую в ходе таких процессов, как криогенное измельчение.
- Улучшенные механические свойства: Равномерная структура зерен и высокая плотность, достигаемые благодаря SPS, приводят к полимерам с повышенной механической прочностью и долговечностью.
-
Сравнение с традиционными методами спекания:
- Эффективность по времени: SPS значительно сокращает время спекания, что делает его более эффективным для крупномасштабного производства.
- Экономия энергии: Более низкие рабочие температуры и сокращение времени обработки приводят к снижению энергопотребления.
- Качество материала: Мелкая, однородная зернистая структура и высокая плотность материалов, спеченных с помощью SPS, часто превосходят материалы, полученные традиционными методами.
Таким образом, искровое плазменное спекание - это высокоэффективный и действенный метод спекания полимеров и других материалов, обладающий многочисленными преимуществами по сравнению с традиционными технологиями.Способность получать высококачественные материалы с улучшенными свойствами делает его ценным инструментом в материаловедении и промышленности.
Сводная таблица:
Аспект | Подробности |
---|---|
Что такое SPS? | Сочетание плазменной активации, горячего прессования и резистивного нагрева для быстрого спекания. |
Преимущества | Быстрый нагрев, более низкие температуры, равномерный нагрев, энергоэффективность, улучшение свойств. |
Механизмы | Джоулевский нагрев, пластическая деформация, разряд между частицами. |
Области применения | Металлы, керамика, композиты, наноматериалы, объемные аморфные сплавы. |
Преимущества полимеров | Сохраняет микроструктуру, улучшает механические свойства. |
По сравнению с традиционными методами | Быстрота, энергоэффективность, превосходное качество материалов. |
Узнайте, как искровое плазменное спекание может революционизировать ваше производство материалов. свяжитесь с нами сегодня !