Спекание в порошковой металлургии - это критический процесс термообработки, который превращает спрессованные металлические порошки в прочные, долговечные и функциональные компоненты.Нагревая компактный порошок до температуры ниже температуры плавления основного материала, спекание соединяет частицы вместе, повышая механическую прочность, плотность и структурную целостность.Этот процесс необходим для создания деталей конечного использования с точными формами и свойствами, что делает его краеугольным камнем современных технологий производства.
Объяснение ключевых моментов:
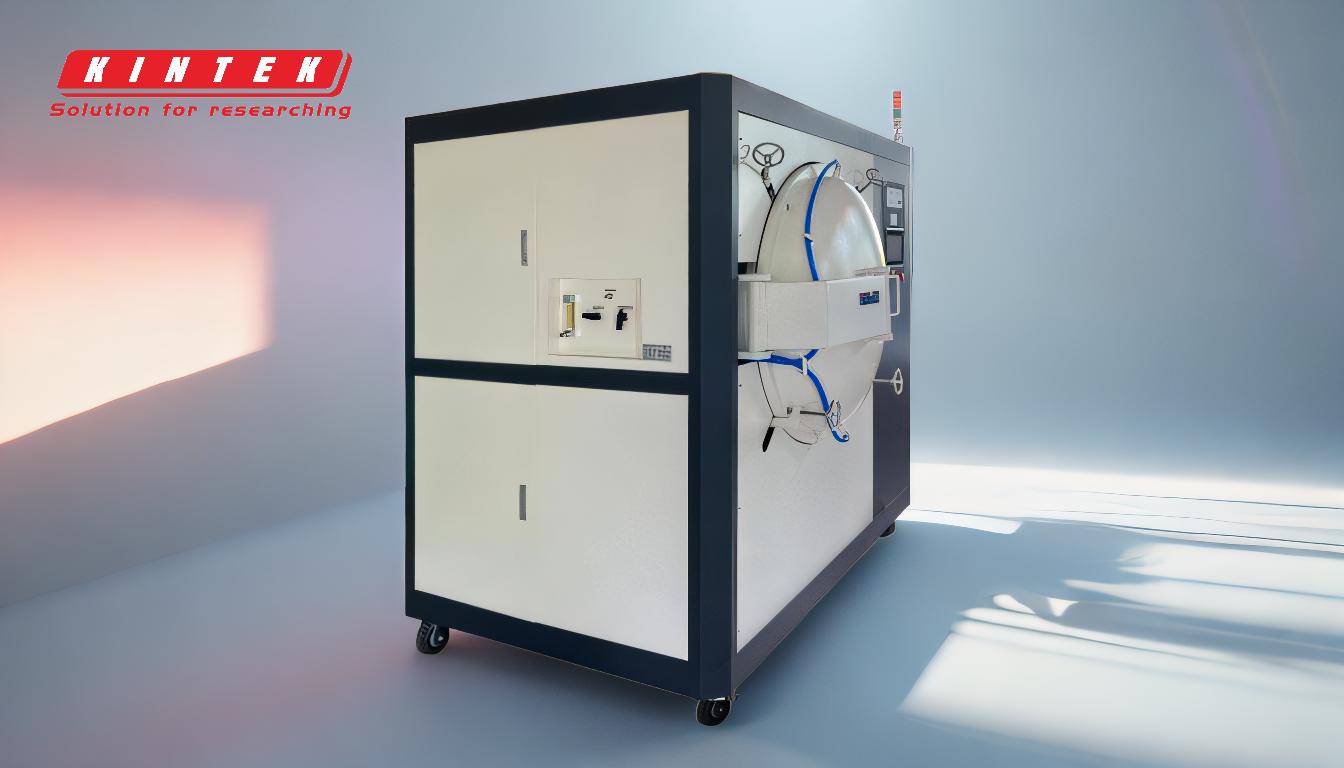
-
Определение спекания:
- Спекание - это процесс термической обработки, используемый в порошковой металлургии для соединения частиц металла вместе без расплавления основного материала.В результате из спрессованного порошка образуется твердая, сплошная структура.
- Процесс включает в себя нагрев прессованного порошка до температуры чуть ниже температуры плавления основного компонента, что позволяет частицам свариться вместе и образовать плотный, прочный материал.
-
Назначение спекания:
- Механическая прочность:Спекание значительно повышает прочность материала за счет скрепления частиц между собой, что делает конечный продукт пригодным для использования в конструкциях.
- Улучшение плотности:Процесс уменьшает пористость, повышая плотность и долговечность компонентов.
- Стабильность размеров:Спекание обеспечивает сохранение формы и размера детали, что очень важно для точного машиностроения.
- Прозрачность и качество поверхности:В некоторых случаях спекание может улучшить прозрачность и качество поверхности материала.
-
Этапы процесса спекания:
- Уплотнение:Металлические порошки сначала прессуются в определенную форму с помощью штампа и гидравлического пресса.
- Нагрев:Спрессованная деталь затем нагревается в печь для спекания до температуры ниже температуры плавления основного материала.Это позволяет частицам соединиться за счет диффузии и образования границ зерен.
- Охлаждение:После спекания деталь постепенно охлаждается для предотвращения растрескивания или деформации, что обеспечивает сохранение ее структурной целостности.
-
Области применения спекания:
- Спекание широко используется в таких отраслях промышленности, как автомобильная, аэрокосмическая и электронная, для производства таких компонентов, как шестерни, подшипники и фильтры.
- Оно также используется в производстве керамики, композитов и современных материалов, где требуется точный контроль свойств материала.
-
Преимущества спекания:
- Экономически эффективный:Спекание позволяет изготавливать сложные формы с минимальными отходами материала, снижая производственные затраты.
- Универсальность материалов:Может применяться для широкого спектра материалов, включая металлы, керамику и композиты.
- Высокая точность:Процесс позволяет создавать детали с жесткими допусками и неизменным качеством.
-
Проблемы и соображения:
- Контроль температуры:Точный контроль температуры спекания имеет решающее значение для предотвращения расплавления или неполного склеивания.
- Выбор материала:Свойства порошка, такие как размер частиц и состав, должны быть тщательно подобраны для достижения желаемых результатов.
- Требования к оборудованию:Высококачественные печи для спекания необходимы для достижения стабильных и надежных результатов.
Понимая принципы и области применения спекания, производители могут оптимизировать свои процессы для эффективного и рентабельного производства высококачественных компонентов.
Сводная таблица:
Аспект | Подробности |
---|---|
Определение | Процесс термической обработки, при котором частицы металла соединяются без расплавления. |
Назначение | Повышает прочность, плотность и стабильность размеров. |
Этапы | Уплотнение → нагрев → охлаждение. |
Области применения | Автомобильная, аэрокосмическая промышленность, электроника, керамика и композиты. |
Преимущества | Экономичность, универсальность и высокая точность. |
Проблемы | Требуется точный температурный контроль, выбор материала и качественное оборудование. |
Узнайте, как спекание может революционизировать ваш производственный процесс. свяжитесь с нашими специалистами сегодня !