Термическое испарение - широко распространенный метод физического осаждения из паровой фазы (PVD), особенно для осаждения металлов с низкой температурой плавления.Несмотря на простоту и надежность, этот метод имеет ряд недостатков.К ним относятся ограниченная совместимость материалов, риск загрязнения, низкая однородность пленки и сложности с контролем состава пленки.Кроме того, термическое испарение менее подходит для высокотемпературных материалов, а такие проблемы, как растрескивание лодки и тепловой удар, могут повлиять на процесс.Несмотря на полезность этого метода в таких приложениях, как OLED и тонкопленочные транзисторы, эти недостатки делают его менее идеальным для осаждения некоторых современных материалов.
Ключевые моменты объяснены:
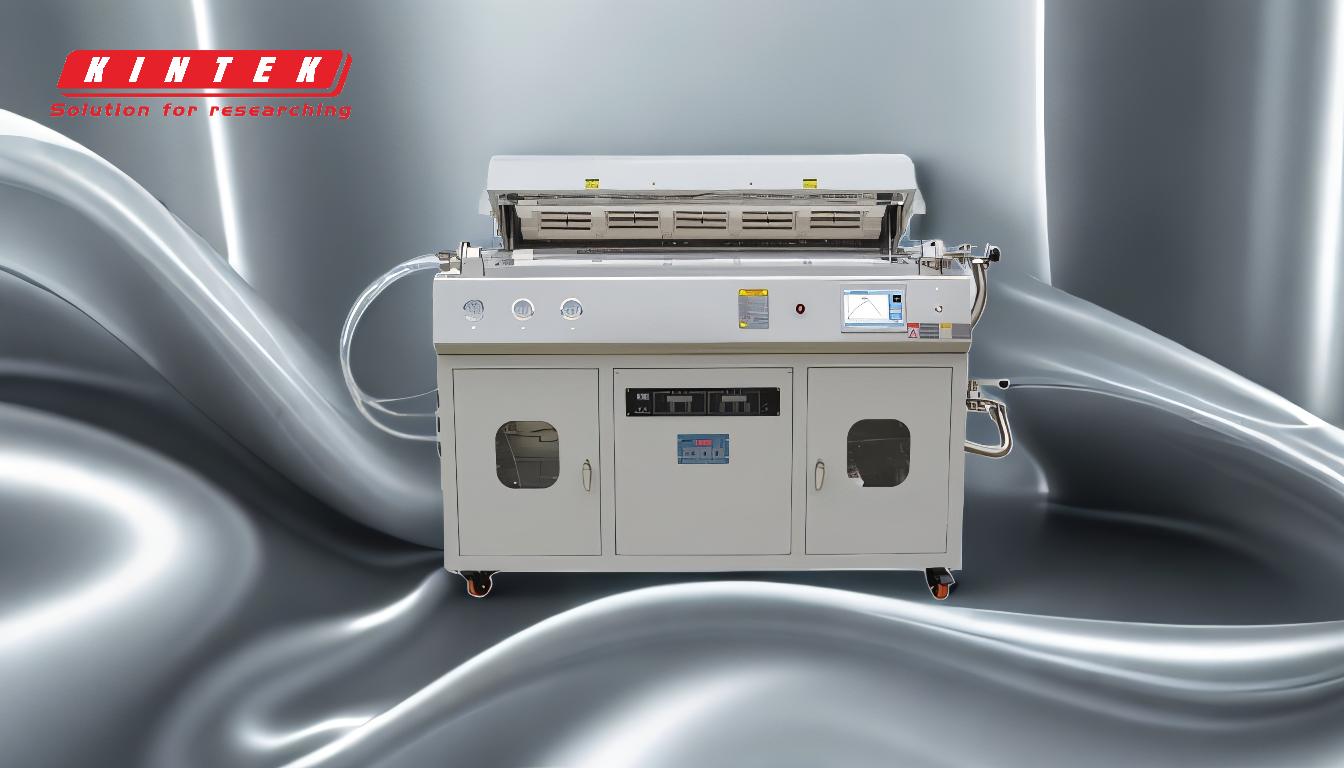
-
Ограниченная совместимость материалов
- Термическое испарение подходит в основном для материалов с относительно низкой температурой плавления.Тугоплавкие металлы или материалы, требующие очень высоких температур, не совместимы с этим методом.Это ограничивает его применение для осаждения современных материалов.
- Процесс основан на плавлении исходного материала, что делает его непригодным для материалов, которые разлагаются или реагируют при высоких температурах.
-
Высокие риски загрязнения
- Загрязнение тигля или лодочки является серьезной проблемой при термическом испарении.При высоких температурах может происходить сплавление между лодочкой и испаряемыми материалами, что приводит к появлению примесей в осажденной пленке.
- Если лодочка растрескивается из-за термического напряжения или легирования, ее приходится выбрасывать, что увеличивает эксплуатационные расходы и время простоя.
-
Плохая однородность пленки
- Добиться равномерной толщины пленки сложно без дополнительного оборудования, такого как планетарные держатели подложек или маски.Это ограничение влияет на качество и стабильность осажденных пленок.
- Шероховатые поверхности подложек могут усугублять неравномерность, что приводит к несовместимым свойствам пленки.
-
Сложность контроля состава пленки
- По сравнению с другими методами PVD, такими как напыление, термическое испарение обеспечивает меньший контроль над составом пленки.Это ограничение особенно критично для приложений, требующих точной стехиометрии.
- Снижение или разложение исходного материала во время испарения может еще больше усложнить контроль состава.
-
Невозможность очистки in situ
- Термическое испарение не позволяет очищать поверхности подложек in situ, что может привести к ухудшению адгезии и увеличению количества примесей в осажденных пленках.
-
Проблемы с покрытием ступеней
- Улучшение ступенчатого покрытия, особенно на сложных или неровных поверхностях, является более сложной задачей при термическом испарении по сравнению с другими методами PVD.
-
Рентгеновское повреждение при электронно-лучевом испарении
- При использовании электронно-лучевого испарения, разновидности термического испарения, существует риск повреждения подложки или окружающих компонентов рентгеновским излучением.
-
Тепловой удар и растрескивание лодки
- Быстрые циклы нагрева и охлаждения могут вызвать тепловой удар, приводящий к растрескиванию лодки.Эта проблема требует тщательной регулировки мощности для обеспечения равномерного нагрева и предотвращения повреждений.
-
Ограничения масштабируемости
- Термическое испарение менее масштабируемо по сравнению с другими методами PVD, что делает его менее подходящим для крупномасштабных промышленных применений.
-
Качество пленки с низкой плотностью
- Пленки, осажденные методом термического испарения, как правило, имеют более низкую плотность, хотя ее можно улучшить с помощью методов ионного усиления.
-
Умеренное напряжение пленки
- Получаемые пленки часто подвергаются умеренному напряжению, что может повлиять на их механические свойства и адгезию к подложкам.
-
Эксплуатационные проблемы
- Баланс между количеством материала в лодке или кармане и риском разрушения, взрыва или вредных реакций является постоянной проблемой.
В итоге, хотя термическое испарение является простым и эффективным методом для определенных применений, его недостатки, такие как риск загрязнения, плохая однородность и ограниченная совместимость материалов, делают его менее подходящим для современных или высокоточных осаждений.Для получения более подробной информации о термическом испарении вы можете изучить термическое испарение .
Сводная таблица:
Недостаток | Описание |
---|---|
Ограниченная совместимость с материалами | Подходит только для материалов с низкой температурой плавления; несовместим с тугоплавкими металлами. |
Высокие риски загрязнения | Легирование и растрескивание лодки приводят к образованию примесей и увеличению эксплуатационных расходов. |
Плохая однородность пленки | Требуется дополнительное оборудование для получения равномерной толщины; шероховатые подложки усугубляют проблему. |
Сложность контроля состава | Менее точная стехиометрия по сравнению с другими методами PVD. |
Невозможность очистки на месте | Очистка подложки невозможна, что приводит к плохой адгезии и загрязнениям. |
Проблемы со ступенчатым покрытием | Низкая производительность на сложных или неровных поверхностях. |
Повреждение рентгеновским излучением (электронный луч) | Риск повреждения подложек и компонентов рентгеновским излучением. |
Тепловой удар и растрескивание лодки | Быстрое нагревание/охлаждение вызывает растрескивание лодки, что требует осторожного наращивания мощности. |
Ограничения по масштабируемости | Менее подходит для крупномасштабных промышленных применений. |
Качество пленки низкой плотности | Пленки, как правило, имеют низкую плотность; улучшить качество можно с помощью методов ионной поддержки. |
Умеренное напряжение пленки | Пленки подвергаются умеренному напряжению, влияющему на механические свойства и адгезию. |
Производственные проблемы | Сбалансировать количество материала с риском разрушения или взрыва очень сложно. |
Вам нужно лучшее решение для осаждения материалов? Свяжитесь с нашими специалистами сегодня чтобы узнать о передовых альтернативах PVD!