Спекание - важнейший процесс в порошковой металлургии и производстве керамики, при котором порошкообразные материалы превращаются в плотные твердые тела под воздействием тепла и давления, обычно ниже температуры плавления материала.Этот процесс включает в себя несколько этапов, в том числе формирование зеленой детали, удаление связующего вещества и собственно спекание, когда частицы сплавляются вместе.Машина для спекания играет важную роль в управлении температурой, атмосферой и давлением, чтобы обеспечить достижение желаемых свойств материала.Ключевыми компонентами процесса спекания являются такие сырьевые материалы, как железосодержащие порошки, плавители и топливо, которые должны соответствовать определенным критериям для эффективного спекания.
Ключевые моменты объяснены:
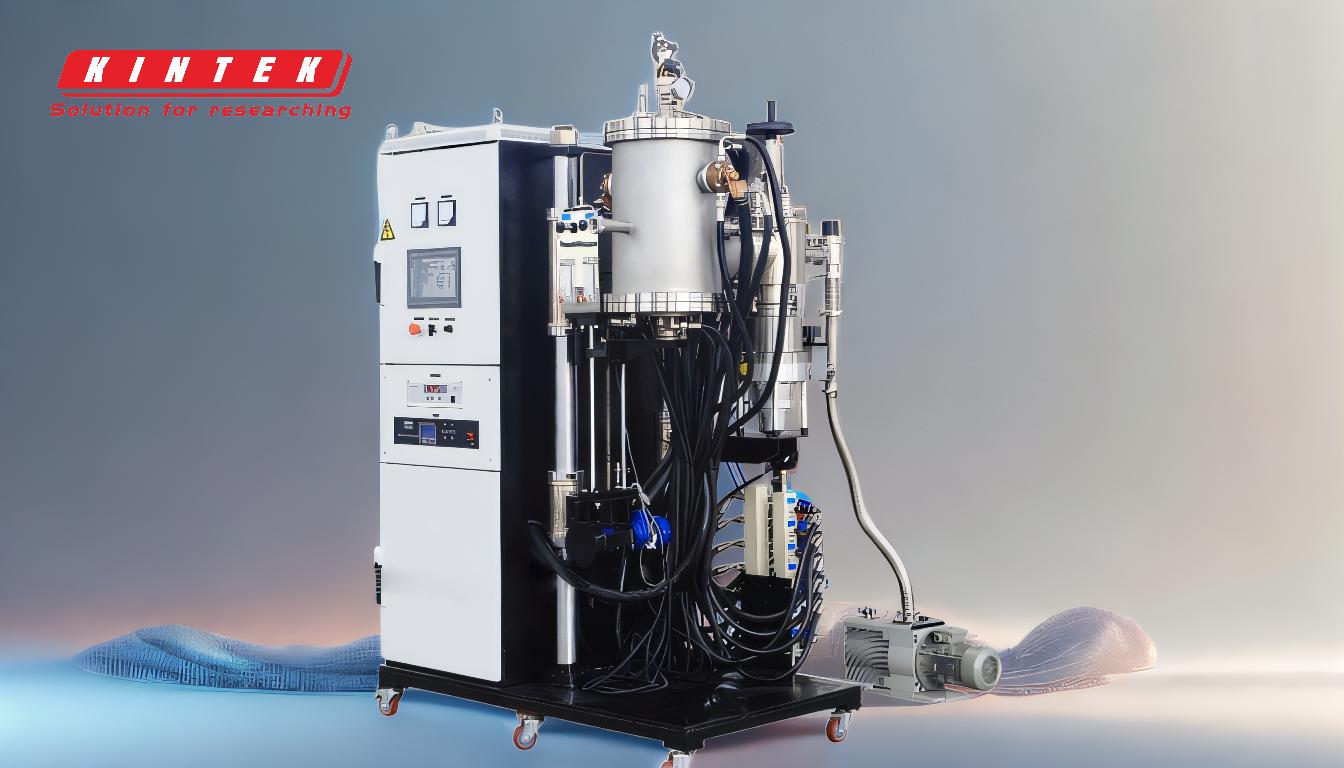
-
Определение и назначение спекания:
- Спекание - это процесс уплотнения и формирования твердой массы материала путем воздействия тепла или давления без достижения температуры плавления материала.
- Он используется для создания плотных, высокопрочных материалов из порошкообразных форм, как правило, в порошковой металлургии и производстве керамики.
-
Этапы процесса спекания:
- Формирование зеленой детали: Смесь первичного порошка и связующего вещества (например, воска или полимера) формируется в нужную форму.
- Удаление связующего вещества: Во время нагрева связующее вещество испаряется или сгорает.
- Спекание: Температура повышается до такой степени, что частицы начинают сплавляться на своих поверхностях либо путем частичного плавления, либо через промежуточное связующее вещество.
-
Компоненты сырья для спекания:
- Железосодержащее сырье: К ним относятся порошок руды с высоким содержанием железа, железный концентрат и другие материалы с высоким содержанием железа.
- Плавильные агенты: Они должны иметь высокое содержание CaO, низкое содержание примесей, удельное содержание воды и размер частиц.
- Топливо: Обычно включает коксовый порошок и бездымный уголь, которые должны иметь высокое содержание фиксированного углерода, низкую зольность и низкое содержание серы.
-
Основные этапы операции спекания:
- Ткань: Укладка дна и перемешивание материалов на агломерационной машине.
- Зажигание: Поверхность отсека на тележке поджигается и поддерживается при соответствующей высокой температуре.
- Спекание: Требуется точный контроль объема воздуха, вакуума, толщины слоя, скорости и конечной точки спекания для обеспечения оптимальных результатов.
-
Атмосферная печь для спекания:
- Этот тип печей контролирует атмосферу (например, азот или аргон) для оптимизации условий спекания.
- Он включает в себя нагревательные устройства, механизмы давления, камеры спекания и системы контроля газа.
- Контролируемая атмосфера обеспечивает миграцию материала, перемещение границ зерен, ликвидацию пор и усадку, в результате чего образуется плотное керамическое тело с определенными прочностными характеристиками.
-
Преимущества спекания:
- Получение материалов с улучшенными механическими свойствами, такими как повышенная прочность и долговечность.
- Позволяет создавать сложные формы и структуры, которые трудно достичь с помощью традиционных процессов плавления и литья.
- Подходит для материалов с очень высокой температурой плавления, таких как вольфрам и молибден.
Понимая эти ключевые моменты, можно оценить сложность и точность, необходимые в процессе спекания, а также критическую роль, которую играют спекательные машины в достижении желаемых свойств материала.
Сводная таблица:
Аспект | Подробности |
---|---|
Определение | Прессование порошкообразных материалов с использованием тепла/давления ниже температуры плавления. |
Этапы | Формирование зеленой детали, удаление связующего вещества и сплавление частиц. |
Ключевые компоненты | Железосодержащие порошки, плавители и топливо. |
Операция спекания | Ткань, зажигание и точный контроль воздуха, вакуума и температуры. |
Спекание в атмосфере | Контролируемая среда для миграции материала, устранения пор и усадки. |
Преимущества | Повышенная прочность, сложные формы и возможность использования высокоплавких материалов. |
Узнайте, как спекание может изменить ваш производственный процесс. свяжитесь с нашими специалистами сегодня !