Процесс горячего прессования - это специализированная технология производства, сочетающая тепло и давление для получения материалов высокой плотности, часто используемых в производстве керамики, металлов и композитов.Процесс включает в себя несколько последовательных этапов, начиная с подготовки порошкового материала, затем его загрузки в пресс, одновременного приложения тепла и давления для достижения плотности и, наконец, охлаждения материала для затвердевания его структуры.Этот метод выгоден тем, что сокращает время, необходимое для фазовых изменений и образования сплавов, по сравнению с традиционными методами спекания.Этапы процесса разработаны таким образом, чтобы обеспечить удаление примесей, надлежащее сцепление частиц и создание плотного, однородного конечного продукта.
Объяснение ключевых моментов:
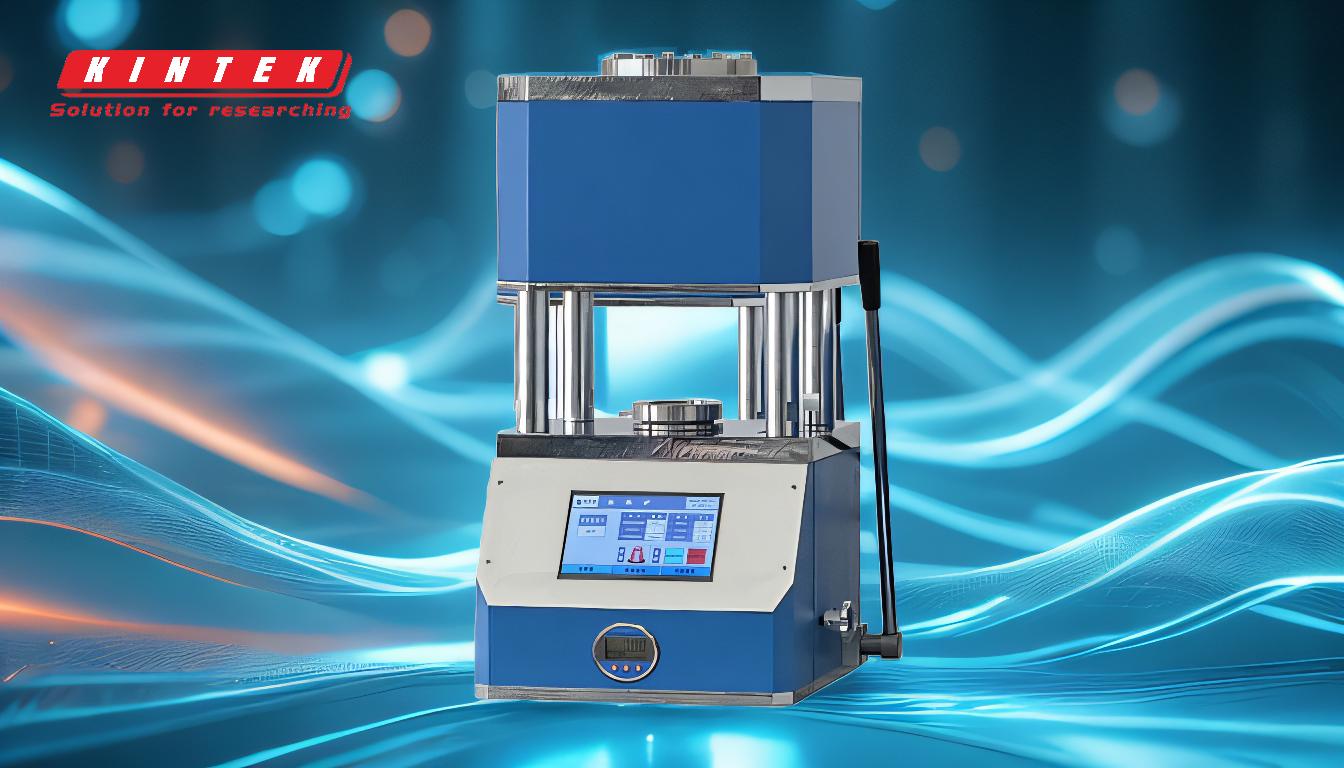
-
Подготовка порошка:
- Распыление или фрезерование:Процесс начинается с получения мелких частиц порошка с помощью таких методов, как распыление (разбиение расплавленного металла на мелкие капли) или измельчение (измельчение твердых материалов в порошок).Этот этап гарантирует, что порошок будет иметь желаемый размер и распределение частиц.
- Смешивание и перемешивание:Затем порошки смешиваются и перемешиваются до получения однородной смеси.Это очень важно для обеспечения однородных свойств конечного продукта.На этом этапе также могут быть включены добавки или связующие вещества для улучшения текучести или сжимаемости порошка.
-
Зарядка:
- Загрузка пороха:Подготовленный порошок загружается в графитовую форму или матрицу, которая затем помещается в печь горячего прессования.Форма предназначена для того, чтобы выдерживать высокие температуры и давление, сохраняя при этом желаемую форму конечного продукта.
-
Вакуумирование:
- Удаление газов и примесей:Из печи откачивают воздух, чтобы создать вакуум, который помогает удалить из порошка все застрявшие газы, влагу и примеси.Этот этап очень важен для предотвращения дефектов, таких как пористость или окисление, на этапах нагрева и прессования.
-
Нагрев:
- Повышение температуры:Печь нагревается до определенной температуры, обычно близкой или превышающей температуру плавления порошкового материала.Тепло размягчает частицы порошка, позволяя им более эффективно соединяться под давлением.Температуру необходимо тщательно контролировать, чтобы избежать перегрева или недогрева, которые могут нарушить целостность материала.
-
Разгерметизация:
- Оказание давления:Одновременно с нагревом к порошку прикладывается давление с помощью гидравлических или механических средств.Это давление способствует уплотнению материала, заставляя частицы сближаться, уменьшая пустоты и способствуя сцеплению частиц.Сочетание тепла и давления ускоряет процесс спекания, что приводит к ускоренной плотности и более однородной структуре.
-
Охлаждение:
- Постепенное охлаждение:После достижения необходимой плотности и сцепления материал постепенно охлаждается до комнатной температуры.Контролируемое охлаждение необходимо для предотвращения термических напряжений или растрескивания в конечном продукте.Скорость охлаждения может варьироваться в зависимости от материала и его предполагаемого применения.
-
Дополнительные вторичные процессы:
- Инфильтрация или отделка:В некоторых случаях для улучшения свойств или внешнего вида конечного продукта могут быть проведены дополнительные процессы, такие как инфильтрация (заполнение пор вторичным материалом) или обработка поверхности (полировка, нанесение покрытия).Эти этапы являются необязательными и зависят от конкретных требований к применению.
При соблюдении этих этапов процесс горячего прессования позволяет получить материалы с высокой плотностью, отличными механическими свойствами и однородной микроструктурой, что делает его предпочтительным методом для производства современных материалов в таких отраслях, как аэрокосмическая, автомобильная и электронная промышленность.
Сводная таблица:
Шаг | Описание |
---|---|
Подготовка порошка | Распыление или измельчение для получения тонкого порошка; смешивание для придания однородности. |
Зарядка | Загрузка порошка в графитовую форму, рассчитанную на высокую температуру и давление. |
Вакуумирование | Вакуумирование печи для удаления газов и примесей, предотвращающее появление дефектов. |
Нагрев | Повышение температуры для размягчения частиц для эффективного сцепления. |
Нагнетание давления | Прикладывание давления для уплотнения материала и уменьшения пустот. |
Охлаждение | Постепенное охлаждение для затвердевания структуры и предотвращения теплового напряжения. |
Вторичные процессы | Дополнительные операции, такие как инфильтрация или финишная обработка для улучшения свойств материала. |
Узнайте, как процесс горячего прессования может повысить эффективность производства ваших материалов. свяжитесь с нами сегодня для получения квалифицированных рекомендаций!