Пористость в порошковой металлургии является критическим фактором, влияющим на механические свойства и характеристики конечного продукта.Уменьшение пористости может быть достигнуто путем оптимизации нескольких ключевых параметров в процессе производства.К ним относятся увеличение давления уплотнения, температуры спекания и времени спекания, которые в совокупности помогают уменьшить видимую пористость и увеличить насыпную плотность.Кроме того, очень важно контролировать размер частиц, поскольку крупные частицы, как правило, увеличивают пористость.Тщательно контролируя эти факторы, производители могут создавать компоненты с высокой плотностью, низкой пористостью и улучшенными механическими свойствами.
Ключевые моменты:
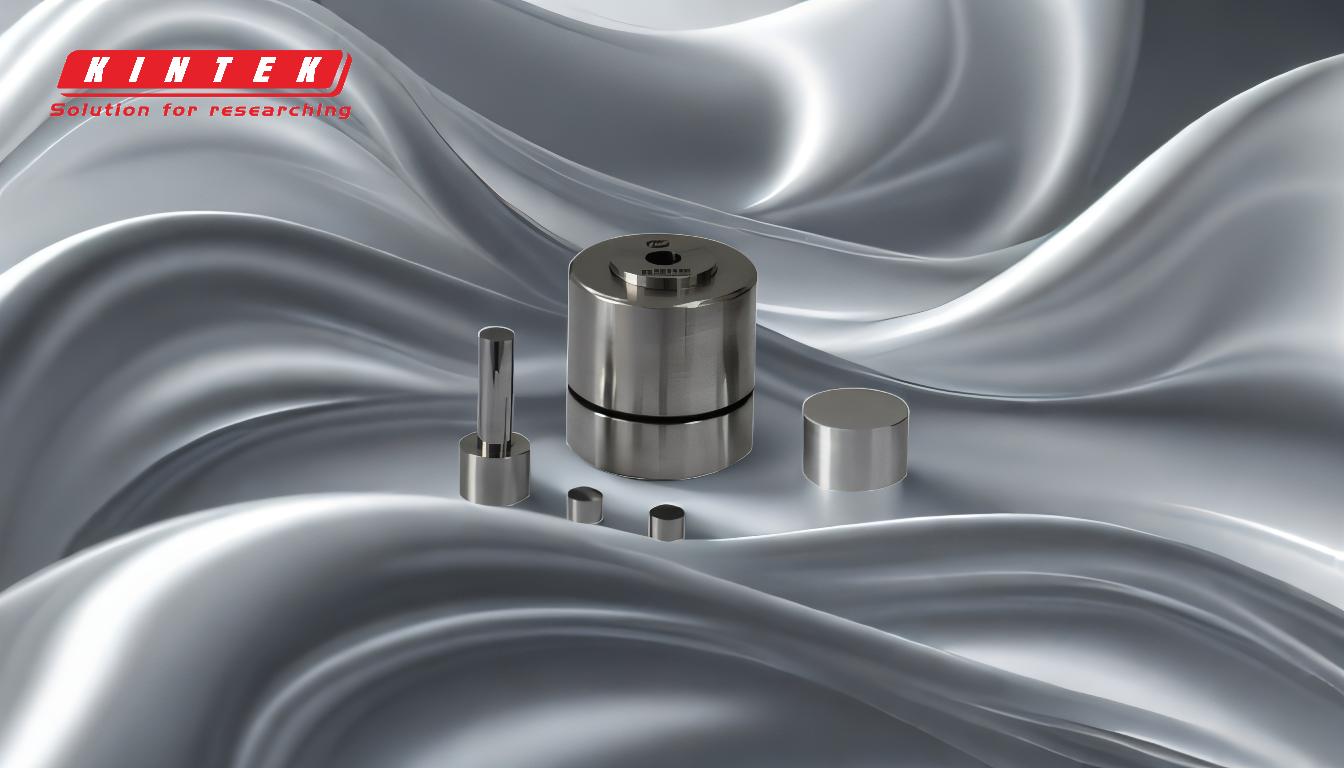
-
Увеличение давления уплотнения:
- Удар:Повышенное давление уплотнения уменьшает зазоры между частицами порошка, что приводит к образованию более плотного компакта с меньшей пористостью.
- Механизм:Когда давление прикладывается на этапе уплотнения, частицы сближаются, минимизируя пустоты и увеличивая насыпную плотность зеленого компакта.
- Практическое рассмотрение:Хотя повышение давления выгодно, оно должно быть сбалансировано с риском повреждения фильеры или неравномерного распределения плотности в детали.
-
Оптимизация температуры и времени спекания:
- Удар:Более высокие температуры спекания и более длительное время спекания способствуют лучшему сцеплению и диффузии частиц, уменьшая пористость и повышая плотность.
- Механизм:Спекание включает в себя нагрев спрессованного порошка ниже температуры плавления, что позволяет атомам диффундировать через границы частиц, что закрывает поры и укрепляет материал.
- Практическое рассмотрение:Чрезмерно высокая температура или время могут привести к росту зерен или деформации, поэтому необходима тщательная оптимизация.
-
Контроль размера частиц:
- Удар:Меньшие размеры частиц обычно приводят к меньшей пористости, поскольку они более эффективно упаковываются, оставляя меньше пустот.
- Механизм:Мелкие частицы имеют более высокое отношение площади поверхности к объему, что улучшает спекание и сцепление.Крупные частицы, с другой стороны, создают больше зазоров и увеличивают пористость.
- Практическое рассмотрение:Хотя более мелкие частицы предпочтительнее, они также могут увеличить риск агломерации, что необходимо контролировать в процессе обработки.
-
Методы производства порошка:
- Удар:Метод, используемый для производства металлических порошков, влияет на их размер, форму и распределение, что, в свою очередь, влияет на пористость.
- Механизм:Такие методы, как распыление, позволяют получать порошки с контролируемым диапазоном размеров, которые могут быть подобраны таким образом, чтобы минимизировать пористость.Дробление и измельчение могут привести к образованию частиц неправильной формы, которые упаковываются менее эффективно.
- Практическое рассмотрение:Выбор подходящего метода производства порошка очень важен для достижения желаемых характеристик частиц и минимизации пористости.
-
Выбор материала:
- Удар:Выбор материала основы (например, медной или железной основы) может влиять на пористость из-за различий в форме, размере частиц и поведении при спекании.
- Механизм:Некоторые материалы спекаются легче, чем другие, что приводит к лучшей плотности и меньшей пористости.
- Практическое рассмотрение:Выбор материала должен соответствовать предполагаемому применению и желаемым механическим свойствам.
Учитывая эти ключевые факторы, производители могут эффективно уменьшить пористость в порошковой металлургии, что приведет к созданию компонентов с улучшенными прочностью, долговечностью и эксплуатационными характеристиками.
Сводная таблица:
Ключевой фактор | Воздействие | Механизм | Практическое рассмотрение |
---|---|---|---|
Увеличение давления уплотнения | Уменьшает зазоры между частицами, что приводит к получению более плотного компакта с меньшей пористостью. | Давление сближает частицы, минимизируя пустоты и увеличивая насыпную плотность. | Сбалансируйте давление, чтобы избежать повреждения матрицы или неравномерного распределения плотности. |
Оптимизация температуры и времени спекания | Способствует сцеплению частиц, уменьшает пористость и повышает плотность. | Нагрев ниже температуры плавления обеспечивает диффузию атомов, закрывая поры и укрепляя материал. | Избегайте чрезмерных температур и времени, чтобы предотвратить рост зерен или деформацию. |
Контроль размера частиц | Мелкие частицы эффективно упаковываются, уменьшая пористость. | Мелкие частицы имеют более высокое отношение площади поверхности к объему, что улучшает спекание и склеивание. | Управляйте риском агломерации с помощью более мелких частиц. |
Методы производства порошков | Влияет на размер, форму и распределение частиц, влияет на пористость. | Распыление позволяет получить контролируемый диапазон размеров; дробление/измельчение может привести к образованию частиц неправильной формы. | Выберите правильный метод для достижения желаемых характеристик частиц. |
Выбор материала | Основной материал влияет на пористость из-за различий в поведении при спекании. | Некоторые материалы спекаются легче, что приводит к лучшему уплотнению и меньшей пористости. | Согласуйте выбор материала с областью применения и желаемыми механическими свойствами. |
Готовы оптимизировать процесс порошковой металлургии? Свяжитесь с нашими экспертами сегодня для получения индивидуальных решений!