Спекание - важнейший процесс в производстве керамики, превращающий порошкообразные материалы в плотные, долговечные и прочные керамические изделия.Он включает в себя нагрев материала до высоких температур ниже температуры плавления, что позволяет частицам соединяться и консолидироваться в структуру с низкой пористостью.Процесс обычно включает в себя такие этапы, как подготовка порошка, формование (прессование), удаление связующего и высокотемпературное спекание, за которым следует дополнительная обработка и сборка.Спекание уменьшает пористость, улучшает механические свойства и необходимо для создания сложных керамических компонентов, используемых в различных отраслях промышленности.
Ключевые моменты:
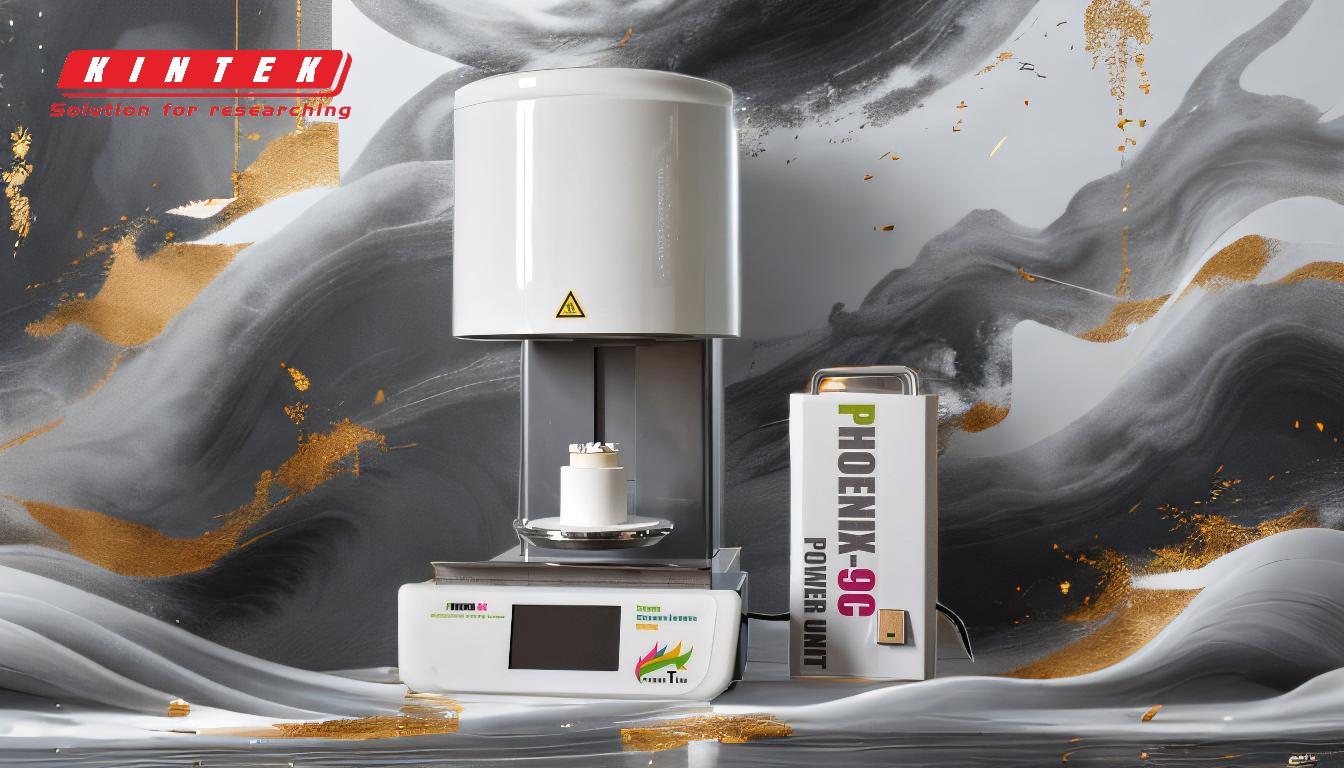
-
Подготовка и смешивание порошка:
- Процесс начинается с подготовки керамических порошков, которые могут включать первичные материалы, связующие и соединительные вещества.Эти компоненты смешиваются до образования однородной суспензии.
- Назначение:Обеспечивает однородность состава, что очень важно для получения стабильных результатов спекания.
- Пример:Смешивание воды, связующего, дефлокулянта и керамического порошка для получения суспензии для распылительной сушки.
-
Формование (прессование):
- Смешанный порошок прессуется в определенную форму с помощью инструментов или форм.В результате образуется \"зеленое тело"\, которое представляет собой целостную, но хрупкую структуру.
- Цель:Создает начальную форму керамической детали перед спеканием.
- Пример:Вдавливание высушенного распылением порошка в форму для получения зеленого тела.
-
Удаление связующего (дебиндинг):
- Зеленое тело нагревается при низких температурах, чтобы сжечь связующие и летучие компоненты.Этот этап очень важен для предотвращения дефектов при высокотемпературном спекании.
- Назначение:Удаляет органические материалы, которые в противном случае могли бы вызвать трещины или пористость.
- Пример:Нагрев зеленого тела при низких температурах для удаления связующих веществ.
-
Высокотемпературное спекание:
- Зеленое тело нагревается до высоких температур (ниже точки плавления) в контролируемой атмосфере.Это приводит к диффузии и сцеплению частиц, уменьшению пористости и увеличению плотности.
- Назначение:Консолидирует керамические частицы в прочную, долговечную массу.
- Пример:Нагрев керамики при высоких температурах для сплавления частиц и формирования твердой структуры.
-
Диффузия и уплотнение частиц:
- Во время спекания атомы диффундируют через границы частиц, что приводит к их слиянию и уплотнению.Этот процесс можно ускорить с помощью таких технологий, как жидкофазное спекание (LPS).
- Назначение:Улучшает механические свойства за счет снижения пористости и улучшения сцепления частиц.
- Пример:Использование LPS для облегчения слияния и уплотнения частиц.
-
Охлаждение и затвердевание:
- После спекания материал медленно охлаждают, чтобы он затвердел в единую массу.Этот этап обеспечивает сохранение структурной целостности керамики.
- Назначение:Стабилизирует спеченную керамику и предотвращает термический стресс.
- Пример:Контролируемое охлаждение для затвердевания керамики в конечный продукт.
-
Процессы после спекания:
- Спеченная керамика может проходить дополнительные этапы, такие как механическая обработка (с использованием алмазных инструментов или ультразвука) и сборка (металлизация и пайка) для достижения желаемых конечных характеристик.
- Назначение:Улучшает форму и повышает функциональность для конкретных целей.
- Пример:Обработка спеченных деталей алмазными инструментами для прецизионных компонентов.
-
Применение и преимущества:
- Спекание широко используется в отраслях, где требуется высокопроизводительная керамика, таких как электроника, аэрокосмическая промышленность и медицинское оборудование.
- Преимущества:Производит керамику с высокой прочностью, низкой пористостью и отличными тепловыми и электрическими свойствами.
- Пример:Производство керамических компонентов для электронных подложек или режущих инструментов.
Следуя этим этапам, спекание превращает керамические порошки в высокоэффективные материалы, подходящие для широкого спектра применений.Этот процесс очень настраиваемый, что позволяет производителям изменять свойства конечного продукта в соответствии с конкретными требованиями.
Сводная таблица:
Шаг | Цель | Пример |
---|---|---|
Подготовка порошка | Обеспечивает однородность состава для равномерного спекания. | Смешивание воды, связующего и керамического порошка для получения суспензии. |
Формирование (прессование) | Создает первоначальную форму керамической детали перед спеканием. | Вдавливание высушенного распылением порошка в форму для формирования зеленого тела. |
Удаление связующего (дебиндинг) | Удаление органических материалов для предотвращения дефектов во время высокотемпературного спекания. | Нагрев зеленого тела при низких температурах для удаления связующих веществ. |
Высокотемпературное спекание | Консолидирует керамические частицы в прочную, долговечную массу. | Нагрев керамики при высоких температурах для сплавления частиц. |
Диффузия частиц | Улучшает механические свойства за счет снижения пористости и улучшения сцепления. | Использование жидкофазного спекания (LPS) для облегчения слияния частиц. |
Охлаждение и затвердевание | Стабилизация керамики и предотвращение теплового напряжения. | Контролируемое охлаждение для затвердевания керамики в конечный продукт. |
Процессы после спекания | Уточнение формы и повышение функциональности для конкретных применений. | Обработка спеченных деталей алмазными инструментами для изготовления прецизионных компонентов. |
Узнайте, как спекание может повысить эффективность вашего керамического производства. свяжитесь с нашими специалистами сегодня !