Физическое осаждение из паровой фазы (PVD) и химическое осаждение из паровой фазы (CVD) - это передовые технологии нанесения покрытий, используемые для улучшения свойств поверхности материалов, таких как твердость, износостойкость и коррозионная стойкость.PVD подразумевает испарение твердого материала в вакууме и нанесение его на подложку, а CVD использует химические реакции газообразных прекурсоров для формирования покрытия.Оба процесса имеют свои этапы, преимущества и области применения.PVD быстрее и работает при более низких температурах, что делает его подходящим для более широкого спектра материалов, в то время как CVD позволяет получать более плотные и однородные покрытия, но требует более высоких температур и более длительного времени обработки.
Ключевые моменты:
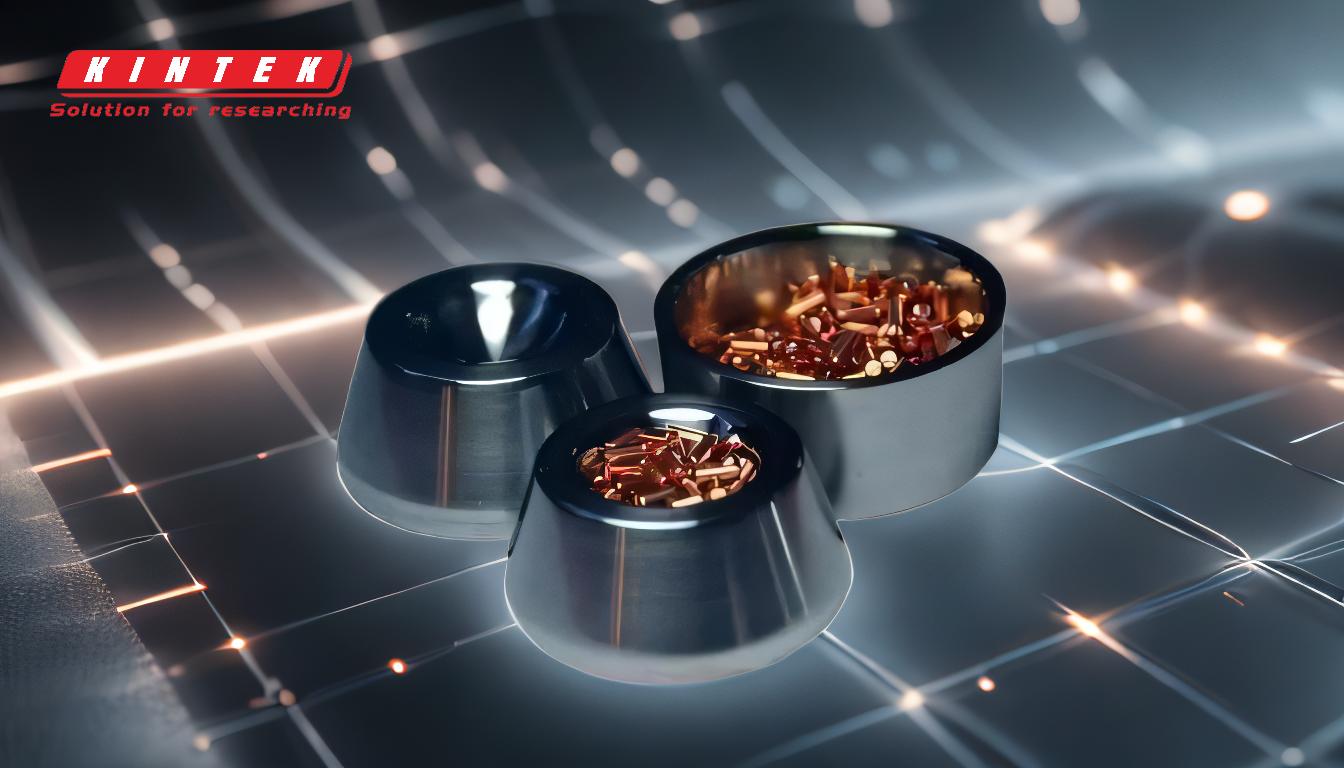
-
Обзор процессов нанесения покрытий PVD и CVD:
- PVD:Испарение твердого материала в вакууме и нанесение его на подложку.Это физический процесс, который работает при низких температурах (около 500 °C) и подходит для металлов, сплавов и керамики.
- CVD:Использует химические реакции газообразных прекурсоров при высоких температурах (800~1000 °C) для нанесения покрытия.Обычно он применяется только к керамике и полимерам и позволяет получать более толстые, плотные и однородные покрытия.
-
Этапы процесса нанесения покрытий методом PVD:
- Шаг 1: Очистка субстрата:Подложка очищается для удаления загрязнений, что обеспечивает лучшую адгезию покрытия.
- Шаг 2: предварительная обработка:Подложка подвергается предварительной обработке для улучшения адгезии покрытия, часто включающей активацию поверхности или травление.
- Шаг 3: нанесение покрытия:Материал мишени испаряется с помощью таких методов, как электронный луч, ионная бомбардировка или катодная дуга.Затем испаренный материал переносится на подложку и осаждается в виде тонкой пленки.
- Шаг 4: Контроль качества:Покрытая основа проверяется на соответствие покрытия установленным стандартам, таким как толщина, однородность и адгезия.
- Шаг 5: Финишная обработка:Для улучшения внешнего вида или характеристик покрытия могут применяться дополнительные виды обработки, такие как полировка или отжиг.
-
Этапы процесса нанесения CVD-покрытий:
- Шаг 1: Введение прекурсоров:Газообразные прекурсоры вводятся в реакционную камеру.
- Шаг 2: Химическая реакция:Прекурсоры вступают в реакцию при высоких температурах (800~1000 °C), образуя желаемый материал покрытия.
- Шаг 3: Осаждение:Продукты реакции осаждаются на подложку, образуя плотное и равномерное покрытие.
- Шаг 4: последующая обработка:Подложка с покрытием может подвергаться дополнительной обработке, такой как отжиг или финишная обработка поверхности, для улучшения ее свойств.
-
Основные различия между PVD и CVD:
- Температура:PVD работает при более низких температурах (около 500 °C), в то время как CVD требует высоких температур (800~1000 °C).
- Толщина покрытия:PVD позволяет получать более тонкие покрытия (3~5 мкм), в то время как CVD приводит к более толстым покрытиям (10~20 мкм).
- Плотность и однородность покрытия:CVD-покрытия более плотные и однородные по сравнению с PVD-покрытиями.
- Совместимость материалов:PVD позволяет осаждать более широкий спектр материалов, включая металлы, сплавы и керамику, в то время как CVD обычно ограничивается керамикой и полимерами.
- Время обработки:PVD быстрее, что делает его подходящим для приложений, требующих быстрого выполнения заказа, в то время как CVD занимает больше времени из-за химических реакций.
-
Области применения PVD и CVD:
- PVD:Обычно используется в областях, требующих высокой износостойкости, таких как режущие инструменты, декоративные покрытия и аэрокосмические компоненты.Оно также подходит для прерывистых процессов резания, таких как фрезерование.
- CVD:Идеально подходит для применения в областях, требующих толстых, плотных и однородных покрытий, таких как производство полупроводников, износостойких покрытий для непрерывных процессов резания, таких как токарная обработка, и высокотемпературных применений.
-
Преимущества и ограничения:
- Преимущества PVD:Более быстрая обработка, низкие рабочие температуры и совместимость с широким спектром материалов.
- Ограничения PVD:Менее плотные и менее равномерные покрытия по сравнению с CVD.
- Преимущества CVD:Более плотные и однородные покрытия, пригодные для использования при высоких температурах.
- Ограничения CVD:Более высокие температуры обработки, более длительное время обработки и ограниченная совместимость материалов.
Понимая подробные этапы и различия между процессами нанесения покрытий PVD и CVD, покупатели оборудования и расходных материалов могут принимать обоснованные решения, основываясь на специфических требованиях своих приложений, таких как желаемые свойства покрытия, совместимость материалов и ограничения на обработку.
Сводная таблица:
Аспект | PVD | CVD |
---|---|---|
Температура | Низкая (около 500 °C) | Выше (800~1000 °C) |
Толщина покрытия | Тоньше (3~5 мкм) | Толще (10~20 мкм) |
Плотность покрытия | Менее плотный | Более плотный и однородный |
Совместимость материалов | Металлы, сплавы, керамика | Керамика, полимеры |
Время обработки | Быстрее | Дольше |
Области применения | Режущие инструменты, декоративные покрытия, аэрокосмические компоненты | Производство полупроводников, износостойкие покрытия, высокотемпературные приложения |
Нужна помощь в выборе правильного процесса нанесения покрытий для вашей области применения? Свяжитесь с нашими экспертами сегодня !