Графит — универсальный материал, широко используемый в различных отраслях промышленности, в том числе в печных камерах, благодаря своим уникальным свойствам, таким как низкая плотность, высокая теплопроводность и отличная излучательная способность. Процесс производства графита включает в себя несколько важных этапов, каждый из которых влияет на конечное качество и характеристики материала. Ниже приводится подробное объяснение этапов производства графита с упором на его применение в печных камерах.
Объяснение ключевых моментов:
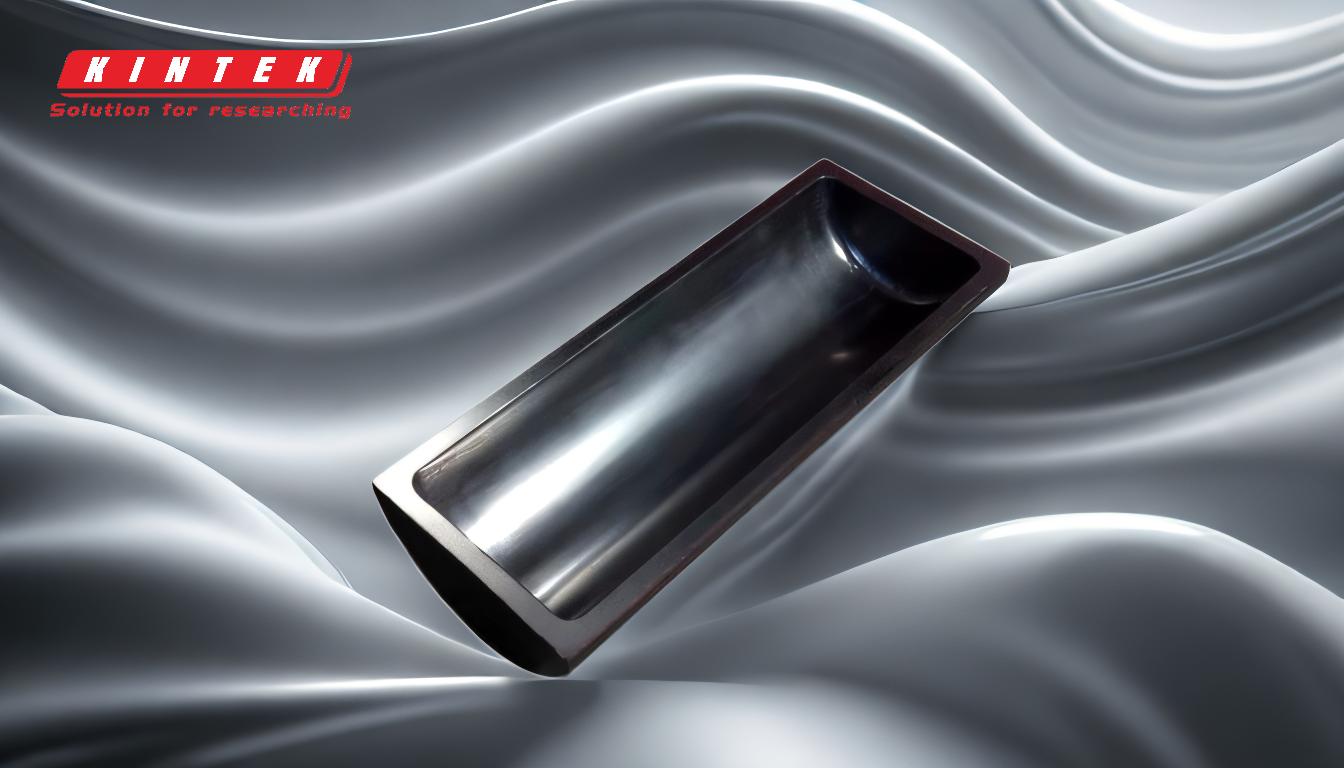
-
Выбор сырья:
- Первым шагом в производстве графита является выбор высококачественного сырья. Обычно в качестве основного источника углерода используют нефтяной кокс или каменноугольный пек. Эти материалы выбраны из-за высокого содержания углерода и чистоты, которые необходимы для производства высокопроизводительного графита.
-
Кальцинирование:
- Отобранное сырье подвергается кальцинированию — процессу, при котором оно нагревается до высоких температур (около 1200–1400 °C) в отсутствие кислорода. На этом этапе удаляются летучие компоненты и влага, в результате чего получается более стабильный и чистый углеродный материал. Кальцинирование имеет решающее значение для обеспечения структурной целостности и термической стабильности конечного графитового продукта.
-
Смешивание и формование:
- После прокаливания углеродный материал смешивают со связующим, обычно каменноугольным пеком, до образования гомогенной смеси. Затем этой смеси придают желаемую форму с использованием различных методов, таких как экструзия, формование или изостатическое прессование. Процесс формования имеет решающее значение для достижения необходимой плотности и механической прочности графита.
-
Выпечка:
- Сформированные углеродные формы запекаются в графитовая печь при температуре от 800°С до 1000°С. Обжиг помогает карбонизировать связующее, превращая его в твердую углеродную матрицу, которая связывает частицы углерода вместе. Этот шаг важен для развития исходных структурных свойств графита.
-
Пропитка:
- Для повышения плотности и механических свойств обожженные углеродные формы часто пропитывают дополнительными углеродистыми материалами. Это включает в себя замачивание форм в жидкой смоле или смоле, а затем повторное запекание. Пропитку можно повторять несколько раз для достижения желаемых свойств.
-
Графитизация:
- Последним и наиболее важным этапом является графитизация, при которой углеродные формы нагреваются до чрезвычайно высоких температур (до 3000°C) в инертной атмосфере. Этот процесс превращает аморфный углерод в кристаллический графит, значительно улучшая его тепло- и электропроводность, а также механическую прочность. Графитизация придает графиту его уникальные свойства, что делает его идеальным для использования в печных камерах.
-
Обработка и отделка:
- После графитации графитовые блоки обрабатываются до точных размеров, необходимых для их конкретного применения. Сюда входит резка, сверление и чистовая обработка поверхности, чтобы обеспечить идеальную посадку и оптимальную производительность в печных камерах.
-
Контроль качества и тестирование:
- Последний этап включает строгий контроль качества и тестирование, чтобы убедиться, что графит соответствует требуемым спецификациям. Сюда входят испытания на плотность, пористость, теплопроводность и механическую прочность. Только после прохождения этих испытаний графит считается готовым к использованию в печных камерах.
Следуя этим шагам, производители могут производить высококачественный графит, который хорошо подходит для использования в печных камерах, предлагая отличные тепловые характеристики, долговечность и простоту ремонта. Уникальные свойства графита, такие как его низкая плотность и высокая излучательная способность, делают его идеальным материалом для создания эффективных и долговечных печных камер.
Сводная таблица:
Шаг | Описание |
---|---|
Выбор сырья | Высококачественный нефтяной кокс или каменноугольный пек выбирают из-за высокого содержания углерода. |
Кальцинирование | Нагревание сырья до 1200–1400°С для удаления летучих веществ и влаги. |
Смешивание и формование | Углеродный материал смешивают со связующим и формуют с помощью экструзии или формования. |
Выпечка | Формы обжигают при температуре 800–1000°С для карбонизации связующего. |
Пропитка | Формы пропитываются смолой/смолой и повторно обжигаются для повышения плотности. |
Графитизация | Нагревается до 3000°C для превращения аморфного углерода в кристаллический графит. |
Обработка и отделка | Блоки разрезаются, сверлятся и доводятся до точных размеров. |
Контроль качества | Строгие испытания на плотность, пористость, теплопроводность и прочность. |
Вам нужен качественный графит для печных камер? Свяжитесь с нашими экспертами сегодня чтобы узнать больше!