CVD (химическое осаждение из паровой фазы) и PVD (физическое осаждение из паровой фазы) — это два широко используемых метода нанесения покрытий на вставки, каждый из которых имеет разные процессы, свойства и области применения. CVD включает химические реакции при высоких температурах (800–1000 °C) для нанесения более толстых покрытий (10–20 мкм), тогда как PVD использует физическое испарение при более низких температурах (250–500 °C) для создания более тонких и сверхтвердых пленок (3 –5 мкм). Покрытия CVD более плотные и однородные, но могут создавать растягивающие напряжения и мелкие трещины из-за высоких температур обработки. С другой стороны, PVD-покрытия создают сжимающие напряжения и идеально подходят для прецизионных применений, требующих гладких и прочных поверхностей. Выбор между CVD и PVD зависит от таких факторов, как толщина покрытия, рабочая температура и требования конкретного применения.
Объяснение ключевых моментов:
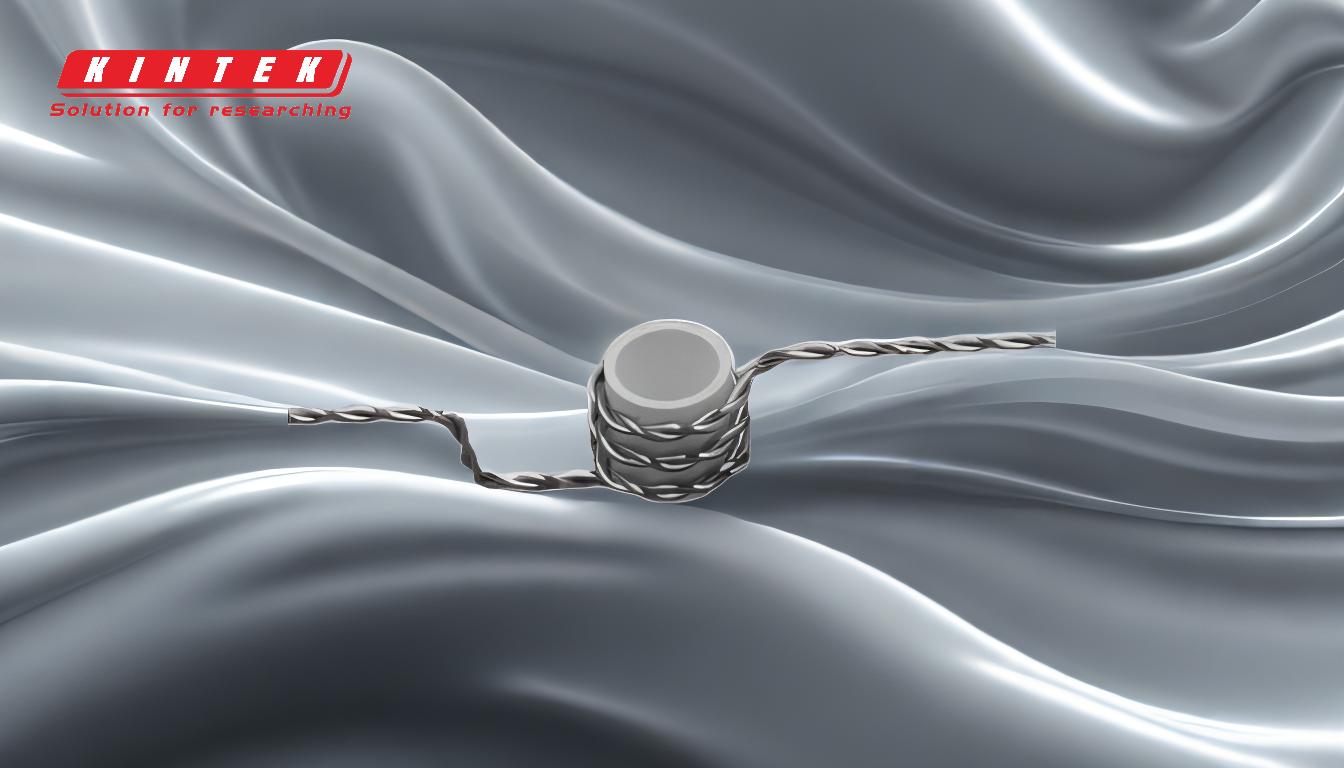
-
Механизм осаждения:
- ССЗ: Включает химические реакции между газообразными предшественниками и субстратом при высоких температурах (800–1000 °C). Это приводит к разнонаправленному осаждению, при котором покрытие формируется равномерно на всех поверхностях, включая сложные геометрические формы.
- ПВД: использует физический процесс, такой как распыление или испарение, для нанесения материала непосредственно на подложку в пределах прямой видимости. Это ограничивает покрытие открытыми поверхностями, но позволяет точно контролировать свойства пленки.
-
Рабочая температура:
- ССЗ: Требуются высокие температуры (800–1000 °C), которые могут повлиять на механические свойства основы и привести к растягивающим напряжениям или мелким трещинам в покрытии.
- ПВД: Работает при более низких температурах (250–500 °C), что делает его пригодным для термочувствительных материалов и снижает риск деформации подложки.
-
Толщина и однородность покрытия:
- ССЗ: Образует более толстые покрытия (10–20 мкм) с превосходной однородностью, что делает их идеальными для применений, требующих высокой износостойкости и долговечности.
- ПВД: Образует более тонкие покрытия (3–5 мкм) с превосходной гладкостью и точностью, подходящие для применений, требующих идеальной обработки поверхности и минимальных изменений размеров.
-
Стресс и адгезия:
- ССЗ: Высокие температуры обработки могут привести к растягивающим напряжениям в покрытии, что в некоторых случаях может привести к образованию микротрещин и снижению адгезии.
- ПВД: Создает сжимающее напряжение во время охлаждения, улучшая адгезию и долговечность покрытия, особенно в высокоточных приложениях.
-
Совместимость материалов:
- ССЗ: В основном используется для керамики и полимеров, обладает превосходной химической стойкостью и термической стабильностью.
- ПВД: Может наносить более широкий спектр материалов, включая металлы, сплавы и керамику, обеспечивая большую универсальность для различных применений.
-
Приложения:
- ССЗ: Обычно используется в отраслях, требующих толстых, износостойких покрытий, таких как режущие инструменты, компоненты аэрокосмической отрасли и производство полупроводников.
- ПВД: Предпочтителен для применений, требующих тонких, гладких и точных покрытий, таких как медицинское оборудование, оптические компоненты и декоративная отделка.
-
Стоимость и время обработки:
- ССЗ: Как правило, более дорогой и трудоемкий из-за высоких температур и сложных химических процессов.
- ПВД: сокращает время обработки и снижает затраты, что делает его более экономичным для крупносерийного производства.
Таким образом, выбор между вставками с покрытием CVD и PVD зависит от конкретных требований применения, включая толщину покрытия, рабочую температуру, совместимость материалов и желаемые свойства поверхности. CVD идеально подходит для толстых, однородных покрытий в условиях высоких температур, тогда как PVD превосходно подходит для прецизионных применений, требующих гладких, прочных поверхностей при более низких температурах.
Сводная таблица:
Аспект | ССЗ | ПВД |
---|---|---|
Механизм осаждения | Химические реакции при высоких температурах (800–1000 °C), разнонаправленные. | Физическое испарение при более низких температурах (250–500 °C), на прямой видимости. |
Толщина покрытия | Более толстый (10–20 мкм), однородный | Тоньше (3–5 мкм), сверхтвердый и гладкий |
Рабочая температура | Высокая (800–1000 °C), может вызвать растягивающее напряжение. | Низкий (250–500 °C), снижает деформацию подложки. |
Стресс и адгезия | Растягивающее напряжение, возможные микротрещины | Сжимающее напряжение, улучшенная адгезия |
Совместимость материалов | Керамика, полимеры, высокая химическая стойкость | Металлы, сплавы, керамика, универсальные |
Приложения | Режущие инструменты, аэрокосмическая промышленность, полупроводники | Медицинские приборы, оптика, декоративная отделка |
Стоимость и обработка | Дорого, отнимает много времени | Экономичная и быстрая обработка |
Нужна помощь в выборе между CVD и PVD для вашего приложения? Свяжитесь с нашими экспертами сегодня за индивидуальную консультацию!