Лазерное спекание, в частности селективное лазерное спекание (SLS), - это универсальная технология аддитивного производства, обладающая уникальными преимуществами и недостатками.Она позволяет получать очень сложные и функциональные формы, которые трудно достичь традиционными методами спекания.Однако этот метод сопряжен со значительными затратами, как на оборудование, так и на материалы, и требует квалифицированных операторов.С другой стороны, альтернативные методы, такие как порошковая металлургия, более рентабельны для крупномасштабного производства, но могут приводить к получению неоднородных компонентов.Высокоскоростное спекание показало свои перспективы в повышении плотности и прочности, но не получило всеобщего одобрения, что указывает на потенциальные ограничения.
Ключевые моменты объяснены:
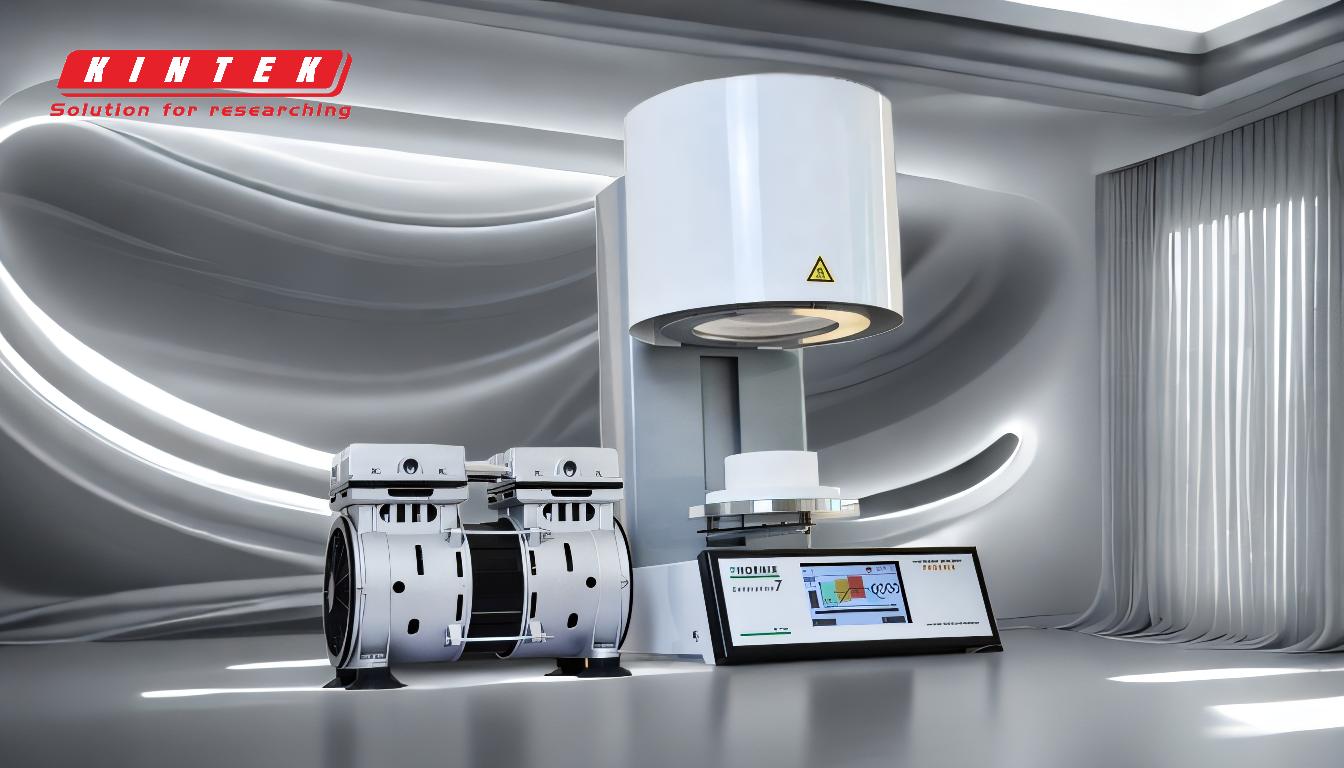
-
Преимущества лазерного спекания:
- Сложные и функциональные формы: Лазерное спекание, особенно SLS, позволяет создавать сложные и функциональные геометрические формы, которые трудно или невозможно получить с помощью традиционных методов спекания.Это делает его идеальным для приложений, требующих высокой точности и сложности, таких как аэрокосмическая промышленность или медицинские приборы.
- Универсальность материалов: SLS может работать с широким спектром материалов, включая полимеры, металлы и керамику, что позволяет применять его в различных отраслях промышленности.
- Минимальная постобработка: Детали, изготовленные с помощью SLS, часто требуют меньше постобработки по сравнению с другими методами аддитивного производства, так как этот процесс по своей природе позволяет получать компоненты почти чистой формы.
-
Недостатки лазерного спекания:
- Высокая стоимость: Первоначальные инвестиции в оборудование для SLS значительны и часто превышают 250 000 долларов.Кроме того, материалы, используемые в SLS, являются дорогостоящими, что еще больше увеличивает общую стоимость.
- Требование к квалифицированному оператору: Для работы с SLS требуются операторы со специальными навыками и подготовкой, что увеличивает эксплуатационные расходы и сложность.
- Ограниченная масштабируемость: Хотя SLS отлично подходит для создания прототипов и мелкосерийного производства, он менее эффективен для крупномасштабного производства по сравнению с такими методами, как порошковая металлургия.
-
Сравнение с порошковой металлургией:
- Экономическая эффективность: Порошковая металлургия, как правило, более доступна по цене, как с точки зрения оборудования, так и материалов, что делает ее более подходящей для крупномасштабного производства.
- Простота эксплуатации: В отличие от SLS, порошковая металлургия не требует высококвалифицированных операторов, что снижает затраты на рабочую силу и требования к обучению.
- Проблемы с однородностью: Одним из недостатков порошковой металлургии является возможность получения неоднородных компонентов из-за трения между порошком и инструментом, что может повлиять на качество и однородность конечного продукта.
-
Высокоскоростное спекание:
- Повышение плотности и прочности: Некоторые исследования показывают, что высокоскоростное спекание позволяет получать детали с несколько более высокой плотностью и прочностью по сравнению с традиционными методами спекания.
- Ограниченное одобрение: Несмотря на эти преимущества, не все поставщики материалов, особенно циркония, одобряют высокоскоростное спекание.Это может быть связано с опасениями по поводу совместимости материалов, стабильности процесса или других технических ограничений.
-
Соображения для покупателей оборудования и расходных материалов:
- Требования к применению: Выбирая между SLS и другими методами спекания, покупатели должны учитывать специфические требования, предъявляемые к их применению, такие как необходимость в сложных геометрических формах, свойства материалов и объем производства.
- Бюджетные ограничения: Высокая стоимость SLS может стать ограничивающим фактором для некоторых организаций, особенно с ограниченным бюджетом или требующих крупномасштабного производства.
- Опыт операторов: При принятии решения следует учитывать необходимость в квалифицированных операторах, поскольку это может повлиять как на первоначальную настройку, так и на текущие эксплуатационные расходы.
- Совместимость материалов: Для тех, кто рассматривает возможность высокоскоростного спекания, необходимо проверить совместимость материалов и проконсультироваться с поставщиками, чтобы убедиться, что метод подходит для предполагаемого применения.
В целом, лазерное спекание, в частности SLS, дает значительные преимущества с точки зрения гибкости конструкции и универсальности материалов, но сопряжено с высокими затратами и сложностью эксплуатации.Альтернативные методы, такие как порошковая металлургия, более рентабельны для крупномасштабного производства, но могут нарушать однородность деталей.Высокоскоростное спекание демонстрирует потенциал для улучшения свойств материала, но не является общепринятым, что указывает на необходимость тщательного рассмотрения его ограничений.Покупатели должны сопоставить эти факторы со своими конкретными потребностями и ограничениями, чтобы принять обоснованное решение.
Сводная таблица:
Аспект | Лазерное спекание (SLS) | Порошковая металлургия | Высокоскоростное спекание |
---|---|---|---|
Сложные формы | Превосходно справляется с созданием сложных и функциональных геометрических форм | Ограниченные возможности для создания сложных форм | Ограниченные данные |
Универсальность материалов | Работает с полимерами, металлами и керамикой | Ограниченный выбор материалов | Потенциальные проблемы совместимости с такими материалами, как диоксид циркония |
Стоимость | Высокие первоначальные инвестиции (> $250 000) и дорогие материалы | Более рентабельно для крупномасштабного производства | Затраты варьируются; не везде одобряется |
Квалификация оператора | Требуются высококвалифицированные операторы | Проще в эксплуатации; требуется меньше квалифицированной рабочей силы | Требуются специализированные знания |
Масштабируемость | Лучше всего подходит для создания прототипов и мелкосерийного производства | Подходит для крупномасштабного производства | Ограниченная масштабируемость из-за технических ограничений |
Постобработка | Требуется минимальная постобработка | Может потребоваться дополнительная постобработка | Минимальная постобработка |
Однородность компонентов | Высокая точность и согласованность | Возможность получения неоднородных компонентов | Повышение плотности и прочности, но ограниченное одобрение |
Нужна помощь в выборе подходящего метода спекания для вашей задачи? Свяжитесь с нашими специалистами сегодня для получения индивидуальной консультации!