Покрытия PVD (Physical Vapor Deposition) известны своей исключительной долговечностью и устойчивостью к износу, коррозии и сколам.Эти покрытия соединяются на молекулярном уровне с основой, создавая прочный тонкий слой, который обладает высокой устойчивостью к внешним воздействиям.Благодаря своей твердости, износостойкости и низким фрикционным свойствам, PVD-покрытия менее склонны к сколам по сравнению с традиционными покрытиями.Их способность выдерживать жесткие условия окружающей среды, включая высокие температуры и коррозионные условия, еще больше увеличивает их долговечность.Хотя ни одно покрытие не может быть полностью защищено от повреждений, PVD-покрытия являются одними из самых долговечных вариантов, что делает их идеальными для применения в таких требовательных отраслях, как автомобильная, аэрокосмическая и медицинская.
Объяснение ключевых моментов:
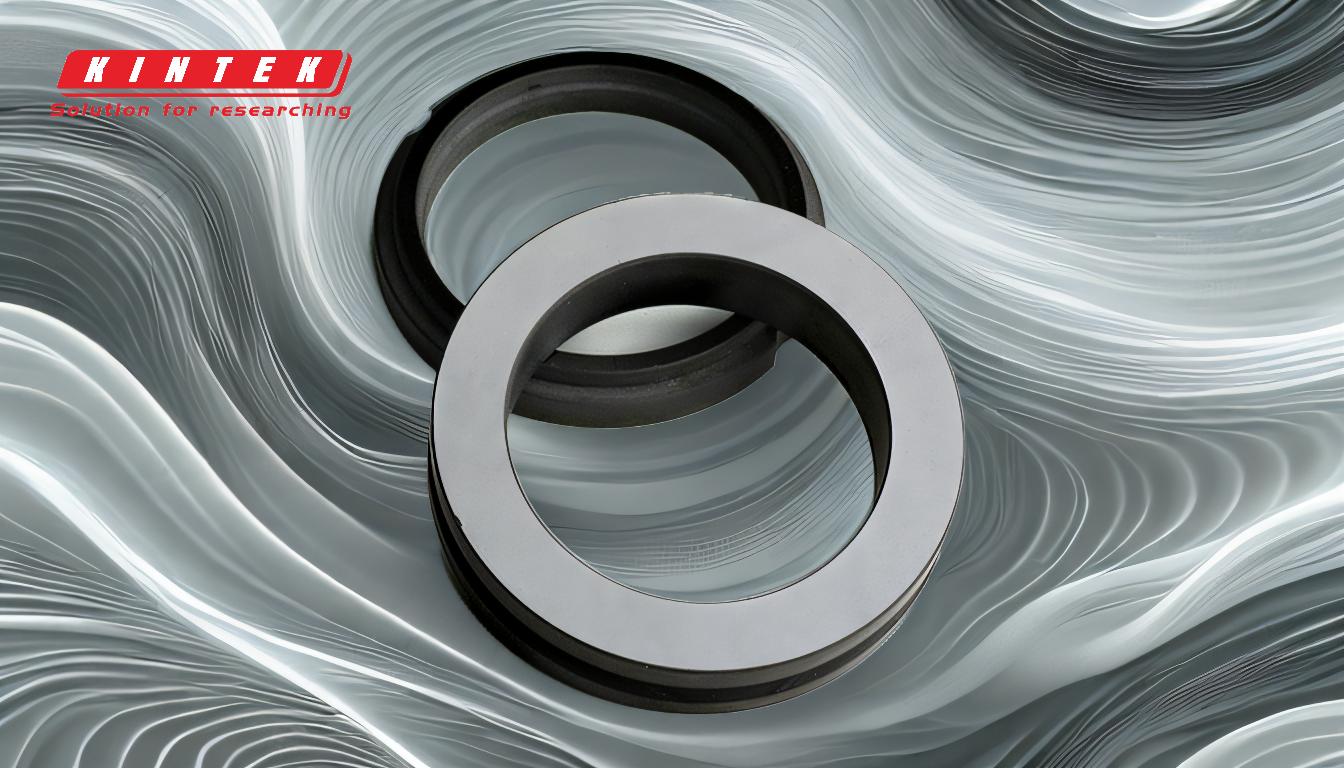
-
Молекулярное связывание и адгезия
- Покрытия PVD образуют с подложкой связь на молекулярном уровне, создавая прочное и долговечное соединение.
- Такой механизм сцепления обеспечивает плотное прилегание покрытия к поверхности, делая его устойчивым к сколам даже при механических нагрузках или ударах.
-
Твердость и износостойкость
- Покрытия PVD известны своей высокой твердостью, часто превышающей твердость традиционных покрытий.
- Твердость покрытия способствует его способности противостоять износу, истиранию и сколам даже в условиях высоких нагрузок.
-
Тонкий и прочный слой
- PVD-покрытия очень тонкие, обычно от 0,5 до 5 микрон.
- Несмотря на свою тонкость, эти покрытия очень прочны и трудно удаляются, что еще больше снижает вероятность сколов.
-
Устойчивость к коррозии и окислению
- Вакуумная среда во время процесса PVD устраняет загрязнения и предотвращает окисление, в результате чего покрытие становится очень устойчивым к коррозии и разрушению под воздействием окружающей среды.
- Эта устойчивость повышает общую прочность и долговечность покрытия, снижая риск образования сколов со временем.
-
Применение в требовательных отраслях промышленности
- Покрытия PVD широко используются в таких отраслях, как автомобильная, аэрокосмическая и медицинская, где долговечность и износостойкость имеют решающее значение.
- Их способность выдерживать суровые условия и механические нагрузки делает их менее склонными к сколам по сравнению с другими покрытиями.
-
Сравнение с традиционными покрытиями
- В отличие от традиционных покрытий, PVD-покрытия значительно тверже и более устойчивы к износу и коррозии.
- Благодаря этой превосходной прочности они реже скалываются, даже если подвергаются грубому обращению или экстремальным условиям.
-
Эффективность в реальном мире
- Было доказано, что PVD-покрытия на значительную долю процентов повышают предел усталости и выносливость материалов, таких как сплав Ti-6Al-4V.
- Эти улучшения демонстрируют способность покрытия противостоять повреждениям, включая сколы, в реальных условиях.
В целом, несмотря на то, что ни одно покрытие не может быть полностью защищено от повреждений, покрытия PVD являются одними из самых прочных и устойчивых к сколам.Их молекулярная связь, твердость, тонкость, устойчивость к коррозии и износу делают их отличным выбором для тех областей применения, где прочность и долговечность имеют первостепенное значение.
Сводная таблица:
Ключевая характеристика | Описание |
---|---|
Молекулярное скрепление | Образует прочную связь с основой на молекулярном уровне, снижая риск сколов. |
Твердость и износостойкость | Превосходит традиционные покрытия, обеспечивая превосходную стойкость к износу и истиранию. |
Тонкий и прочный слой | Очень тонкий (0,5-5 мкм), но при этом очень прочный, что сводит к минимуму образование сколов. |
Устойчивость к коррозии | Противостоит коррозии и окислению, повышая долговечность в суровых условиях. |
Применение в промышленности | Широко используется в автомобильной, аэрокосмической и медицинской промышленности для обеспечения долговечности и производительности. |
Реальные характеристики | Улучшает пределы усталости и выносливости, снижая повреждения в экстремальных условиях. |
Хотите повысить долговечность ваших материалов с помощью PVD-покрытий? Свяжитесь с нами сегодня чтобы узнать больше!