Производство пресс-форм - это сложный и точный процесс, включающий несколько этапов, от проектирования до конечного производства.Обычно процесс начинается с создания детального проекта, затем следует выбор материала, механическая обработка и отделка.Затем пресс-форма тестируется и дорабатывается, чтобы убедиться в ее соответствии требуемым характеристикам.На последнем этапе происходит собственно изготовление деталей с использованием пресс-формы: жидкий материал впрыскивается в полость пресс-формы, охлаждается и затвердевает, образуя нужную форму.Этот процесс крайне важен в таких отраслях, как автомобилестроение, производство потребительских товаров и электроники, где важна высокая точность и повторяемость.
Объяснение ключевых моментов:
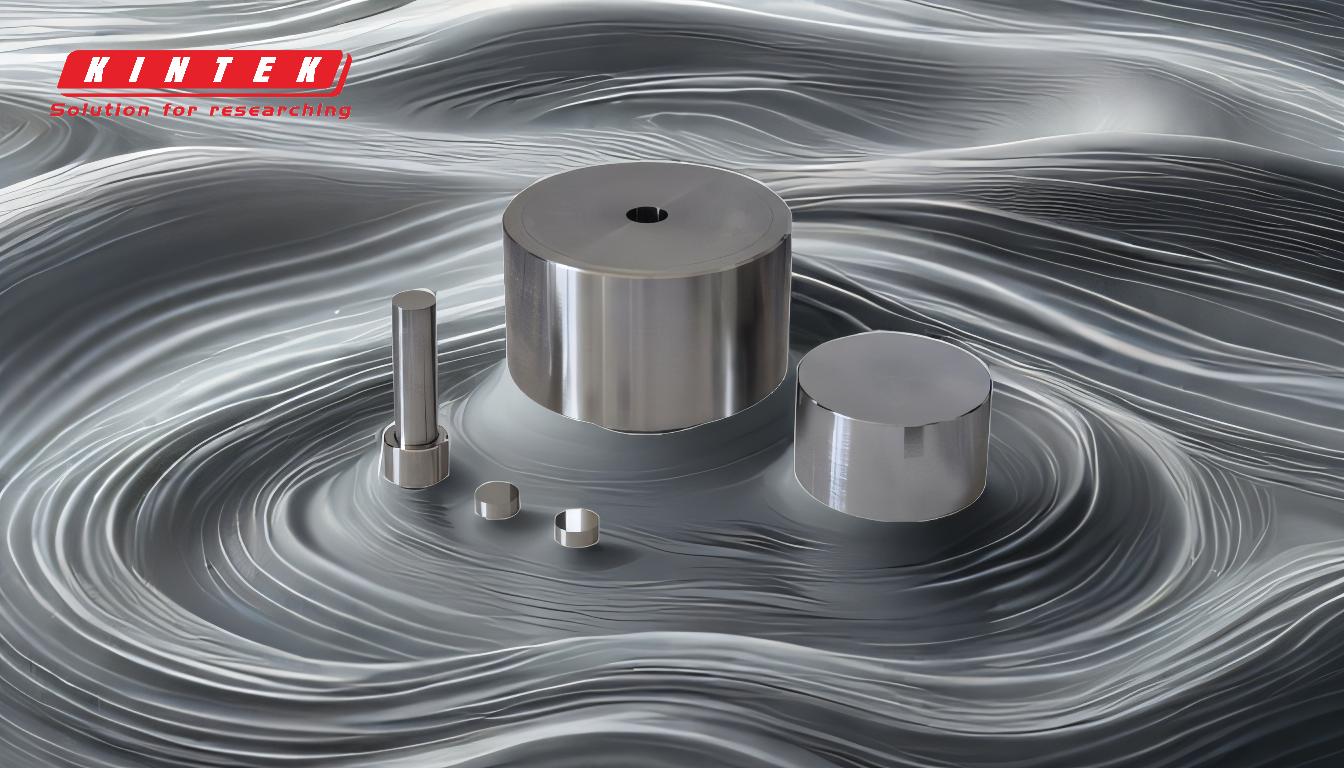
-
Дизайн и планирование:
- Концептуализация:Процесс начинается с разработки концепции конструкции пресс-формы, часто с использованием программного обеспечения CAD (Computer-Aided Design).На этом этапе определяются форма, размер и особенности пресс-формы.
- Выбор материала:Исходя из требований к конструкции, выбирается подходящий материал (обычно сталь или алюминий).Сталь предпочтительнее из-за ее прочности и способности выдерживать высокое давление, в то время как алюминий выбирают из-за его меньшего веса и более быстрого времени обработки.
- Моделирование и анализ:Перед изготовлением часто проводится моделирование, чтобы предсказать, как будет работать пресс-форма.Это включает анализ потока, чтобы убедиться, что материал правильно заполнит полость формы, и анализ охлаждения, чтобы оптимизировать процесс охлаждения.
-
Обработка:
- Обработка с ЧПУ:Выбранный материал затем обрабатывается на станках с ЧПУ (компьютерное числовое управление).Это включает в себя резку, сверление и фрезерование материала для формирования специфических характеристик пресс-формы.Обработка с ЧПУ обеспечивает высокую точность и повторяемость.
- EDM (электроэрозионная обработка):Для создания более сложных форм или труднодоступных участков используется EDM.Этот процесс включает в себя использование электрических разрядов для эрозии материала, что позволяет создавать сложные детали.
- Отделка поверхности:После механической обработки пресс-форма подвергается процессу обработки поверхности, такому как полировка или нанесение покрытия для улучшения качества и долговечности поверхности.Этот этап очень важен для обеспечения гладкости конечного продукта.
-
Сборка и тестирование:
- Сборка:После того как все компоненты пресс-формы обработаны и готовы, их собирают.Это включает в себя установку сердечника и полости, а также любых вставок и выталкивающих штифтов.
- Тестирование:Затем собранная пресс-форма тестируется на предмет правильности функционирования.Для этого в полость пресс-формы впрыскивается материал (чаще всего пластик) и проверяется качество полученной детали.По результатам испытаний в пресс-форму могут быть внесены коррективы.
-
Производство:
- Литье под давлением:На этапе производства пресс-форма используется в машине для литья под давлением.Жидкий материал (обычно пластик) подается в нагретую бочку, перемешивается, а затем под высоким давлением впрыскивается в полость формы.
- Охлаждение и выталкивание:Материал остывает и затвердевает до конфигурации формы.После затвердевания деталь извлекается из формы, и процесс повторяется для следующей детали.
- Контроль качества:На протяжении всего производственного процесса проводятся мероприятия по контролю качества, чтобы гарантировать соответствие каждой детали требуемым спецификациям.Это может включать визуальный осмотр, проверку размеров и функциональные испытания.
-
Техническое обслуживание и доработка:
- Регулярное обслуживание:Чтобы пресс-форма оставалась в хорошем состоянии и продолжала производить высококачественные детали, требуется регулярное техническое обслуживание.Оно включает в себя чистку, смазку и проверку на предмет износа.
- Доработка:Со временем пресс-форму может потребоваться доработать или модифицировать, чтобы учесть изменения в конструкции или улучшить характеристики.Это может потребовать повторной обработки определенных участков или обновления компонентов пресс-формы.
В целом, изготовление пресс-формы - это многоэтапный процесс, требующий тщательного планирования, точной обработки и тщательных испытаний.Каждый этап, от проектирования до производства, играет важную роль в обеспечении соответствия конечной формы требуемым техническим характеристикам и возможности стабильного производства высококачественных деталей.
Сводная таблица:
Этап | Основные виды деятельности |
---|---|
Проектирование и планирование | Разработка концепции, выбор материалов, моделирование и анализ |
Обработка | Обработка с ЧПУ, электроэрозионная обработка, финишная обработка поверхности |
Сборка и тестирование | Сборка, тестирование, регулировка |
Производство | Литье под давлением, охлаждение и выталкивание, контроль качества |
Техническое обслуживание | Регулярное обслуживание, усовершенствование |
Нужны рекомендации экспертов по изготовлению пресс-форм? Свяжитесь с нами сегодня за индивидуальными решениями!