Покрытия PVD (Physical Vapor Deposition) известны своей высокой твердостью, которая обычно составляет от 1500 HV (твердость по Виккерсу) до 4500 HV, в зависимости от типа покрытия, материала подложки и используемого метода PVD.Для сравнения, твердость углеродистых сталей составляет около 250 HV, а азотированных или никелированных/хромированных сталей - от 600 HV до 1000 HV.PVD-покрытия, такие как TiN (нитрид титана), особенно ценятся за их способность повышать износостойкость, коррозионную стойкость и долговечность.В некоторых случаях специализированные покрытия, такие как DLC (алмазоподобный углерод), могут достигать твердости до 9000 HV.Твердость PVD-покрытий является важнейшим фактором, определяющим их эксплуатационные характеристики, что делает их пригодными для применения в таких ответственных отраслях, как автомобильная, аэрокосмическая и медицинская.
Ключевые моменты:
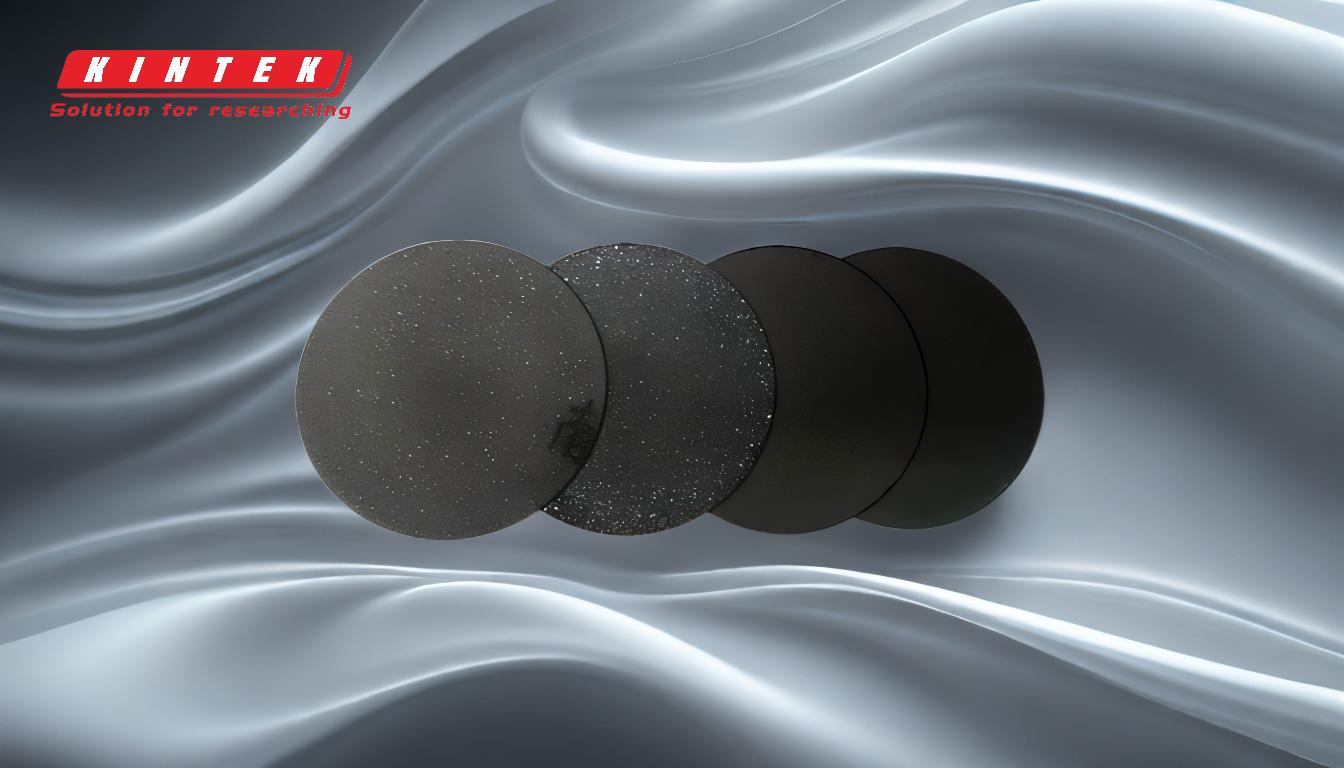
-
Диапазон твердости PVD-покрытий:
- PVD-покрытия обычно имеют диапазон твердости от 1500 HV - 4500 HV в зависимости от конкретного материала покрытия и процесса.
- Для справки, 900 HV соответствует 67 HRC (Rockwell C) , что значительно тверже многих распространенных материалов, таких как углеродистая сталь (250 HV) или азотированные стали (600-1000 HV).
- Специализированные покрытия, такие как DLC (алмазоподобный углерод) позволяет достичь еще более высоких значений твердости, достигающих 9000 HV .
-
Факторы, влияющие на твердость:
-
Твердость PVD-покрытий зависит от нескольких факторов:
- Материал покрытия:Различные материалы (например, TiN, TiCN, CrN, DLC) имеют разный уровень твердости.
- Материал подложки:Материал основы может влиять на свойства покрытия.Например, покрытия TiN на сплаве Ti-6Al-4V повышают предел усталости и выносливость.
- Метод PVD:Конкретный процесс PVD (например, напыление, дуговое испарение) и навыки оператора могут повлиять на твердость покрытия.
- Толщина:PVD-покрытия очень тонкие (0,5-5 мкм), но их твердость оптимальна для работы.
-
Твердость PVD-покрытий зависит от нескольких факторов:
-
Сравнение с другими материалами:
- Углеродистые стали:Обычно имеют твердость около 250 HV (25 HRC) .
- Стали с азотированным или никель-хромовым покрытием:Диапазон между 600 HV - 1000 HV .
- PVD-покрытия:На 1500-4500 HV PVD-покрытия значительно тверже, что делает их идеальными для применения в областях, требующих высокой износостойкости и долговечности.
-
Применение и преимущества:
- Покрытия PVD широко используются в таких отраслях, как автомобильная, аэрокосмическая и медицинская благодаря высокой твердости, износостойкости и коррозионной стойкости.
- Они также обеспечивают низкое трение и улучшенный эстетический вид что делает их пригодными как для функциональных, так и для декоративных целей.
-
Твердость и износостойкость:
- Хотя высокая твердость обычно коррелирует с повышенной износостойкостью Но прямой зависимости между ними не существует.Значения твердости выше оптимального порога могут указывать на обезуглероживание что может снизить эксплуатационные характеристики.
- PVD-покрытия позволяют найти баланс между твердостью и другими свойствами, такими как прочность и адгезия для обеспечения долговременной прочности.
-
Специализированные покрытия:
- DLC-покрытия:Это одни из самых твердых PVD-покрытий, их твердость достигает 9000 HV .Они особенно ценятся за низкое трение и отличная износостойкость .
- TiN-покрытия:Обычно используется для похожий на золото внешний вид и высокой твердостью, они идеально подходят для изготовления режущих инструментов, пресс-форм и декоративных изделий.
-
Измерение твердости:
- Твердость обычно измеряется с помощью твердость по Виккерсу (HV) шкала, которая подходит для тонких покрытий.Для сравнения, Роквелл С (HRC) Также используется показатель 900 HV, эквивалентный 67 HRC.
-
Оптимальная твердость и коррозионная стойкость:
- PVD-покрытия позволяют достичь оптимальный уровень твердости что повышает их коррозионная стойкость .Чрезмерная твердость может привести к образованию твердых фаз, что может ухудшить эксплуатационные характеристики.
В общем, твердость PVD-покрытий - это ключевое свойство, которое делает их высокопрочными и пригодными для использования в сложных условиях.Их твердость варьируется от 1500 до 4500 HV, а у специализированных покрытий типа DLC достигает 9000 HV.Такая исключительная твердость в сочетании с износостойкостью, коррозионной стойкостью и низким коэффициентом трения делает PVD-покрытия бесценными в различных отраслях промышленности.
Сводная таблица:
Аспект | Подробности |
---|---|
Диапазон твердости | 1500-4500 HV (до 9000 HV для DLC-покрытий) |
Материалы для сравнения | Углеродистая сталь: 250 HV; Азотированные стали: 600-1000 HV |
Ключевые преимущества | Высокая износостойкость, коррозионная стойкость, низкое трение и долговечность |
Применение | Автомобильная, аэрокосмическая, медицинская и декоративная промышленность |
Специализированные покрытия | TiN (нитрид титана), DLC (алмазоподобный углерод) |
Измерение | Твердость по Виккерсу (HV); 900 HV = 67 HRC |
Узнайте, как PVD-покрытия могут улучшить характеристики ваших материалов. свяжитесь с нашими специалистами сегодня !