Покрытия из алмазоподобного углерода (DLC) широко используются благодаря своей превосходной износостойкости, низкому трению и химической инертности.Однако они также имеют ряд недостатков, включая ограничения по температурам обработки, сложности в применении из-за требований к высоким температурам, а также проблемы, связанные с напряжением, растрескиванием и однородностью покрытия.Кроме того, DLC-покрытия могут подходить не для всех материалов или областей применения, особенно для тех, которые связаны с прерывистыми процессами резки или требуют точного маскирования.Эти факторы могут ограничить их эффективность и применимость в определенных промышленных условиях.
Объяснение ключевых моментов:
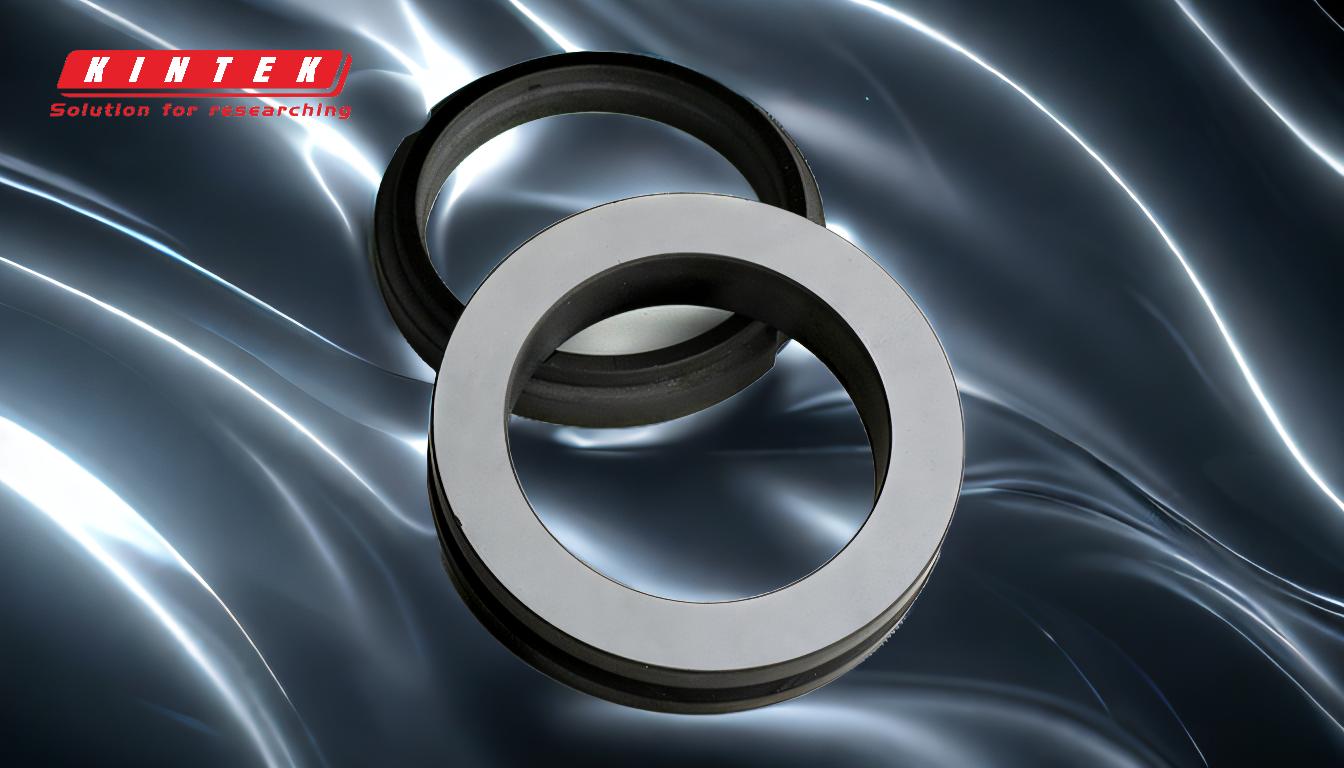
-
Высокие температуры обработки:
- DLC-покрытия, особенно нанесенные методом химического осаждения из паровой фазы (CVD), требуют высоких температур обработки (800-1000°C или 1875-1925°F).Это ограничивает их применение материалами, способными выдержать такую температуру, например цементированным карбидом.Многие субстраты, особенно с более низкой температурой плавления или термической стабильностью, не выдерживают таких условий, что ограничивает спектр применения DLC-покрытий.
-
Растягивающее напряжение и растрескивание:
- Толщина CVD-покрытий (10-20 мкм) может привести к растягивающему напряжению во время охлаждения.Это напряжение часто приводит к образованию мелких трещин, которые могут распространяться при внешнем воздействии, вызывая отслаивание покрытия.Это делает DLC-покрытия менее подходящими для применения в условиях прерывистого процесса резания, например при фрезеровании, где покрытие более склонно к разрушению.
-
Ограничения в маскировке и равномерности покрытия:
- CVD-процессы затрудняют маскировку определенных областей, что часто приводит к получению покрытия "все или ничего".Такой недостаток точности может быть проблематичным для приложений, требующих селективного покрытия.Кроме того, размер деталей, на которые можно наносить покрытие, ограничен вместимостью реакционной камеры, поэтому для нанесения покрытия детали часто приходится разбирать на отдельные компоненты.
-
Неоднородная зернистая структура и шероховатость поверхности:
- Зернистая структура CVD-алмазных покрытий неоднородна из-за процесса роста, и шероховатость поверхности изменяется с увеличением толщины.Это приводит к необходимости полировки для приложений, требующих гладких поверхностей, таких как теплораспределители.Неоднородность также может повлиять на механические и термические свойства покрытия.
-
Метастабильная природа и изменчивость сцепления:
- DLC - это метастабильная форма аморфного или гидрогенизированного аморфного углерода, содержащая смесь sp2 и sp3 связей.Свойства пленки зависят от соотношения этих связей, которое может значительно варьироваться.Это может привести к несоответствию твердости, износостойкости и других критических свойств, что затрудняет достижение одинаковых характеристик различных покрытий.
-
Ограниченная пригодность для прерывистых процессов резания:
- Из-за склонности к растрескиванию и отслаиванию под нагрузкой DLC-покрытия менее эффективны в процессах прерывистого резания, таких как фрезерование.Многократные удары и термоциклирование в таких процессах могут усугубить разрушение покрытия, что ограничивает их применение в этих областях.
-
Логистические проблемы:
- Процесс CVD не является процессом \"на месте\", то есть детали должны быть доставлены в специализированные центры нанесения покрытий.Это усложняет логистику, увеличивает стоимость и время производственного процесса, особенно для крупных или сложных компонентов.
-
Компромисс между химической стойкостью и износостойкостью:
- Хотя DLC-покрытия известны своей превосходной износостойкостью и химической стойкостью, эти свойства могут варьироваться в зависимости от метода осаждения и конкретного состава покрытия.В некоторых случаях достижение оптимальной износостойкости может происходить за счет других желаемых свойств, таких как адгезия или теплопроводность.
В целом, хотя DLC-покрытия обладают значительными преимуществами в плане долговечности, снижения трения и химической стойкости, их высокая температура обработки, восприимчивость к напряжениям и растрескиванию, а также ограничения в маскировке и однородности являются заметными недостатками.Эти факторы необходимо тщательно учитывать при выборе DLC-покрытий для конкретных применений.
Сводная таблица:
Недостаток | Описание |
---|---|
Высокие температуры обработки | Требуется 800-1000°C, что ограничивает применение жаропрочных материалов, таких как цементированный карбид. |
Растягивающее напряжение и растрескивание | Толстые покрытия приводят к образованию трещин, вызванных напряжением, что делает их непригодными для прерывистых процессов резки. |
Маскирование и равномерность покрытия | CVD-процессам не хватает точности при маскировании, что приводит к получению покрытий по принципу "все или ничего". |
Неоднородная структура зерна | Структура зерен и шероховатость поверхности различны, что требует полировки для гладкого применения. |
Метастабильность и изменчивость связей | Свойства зависят от соотношения связей sp2/sp3, что приводит к непостоянной твердости и износостойкости. |
Ограниченная пригодность для прерывистого резания | Склонны к разрушению при фрезеровании и аналогичных процессах из-за напряжения и термоциклирования. |
Логистические проблемы | Детали необходимо доставлять в специализированные центры, что увеличивает время и стоимость. |
Компромиссы между химической стойкостью и износостойкостью | Оптимальная износостойкость может ухудшить адгезию или теплопроводность. |
Нужна помощь в определении того, подходят ли DLC-покрытия для вашей области применения? Свяжитесь с нашими экспертами сегодня для получения индивидуальной консультации!