Выбор оптимального покрытия для металлических инструментов зависит от конкретной области применения, условий окружающей среды и требований к эксплуатационным характеристикам.Ключевыми факторами являются тип процесса нанесения покрытия (например, CVD или PVD), материал основы, а также подверженность инструмента износу, коррозии и истиранию.Покрытия из карбида вольфрама идеально подходят для экстремальных условий износа, в то время как другие покрытия могут лучше подходить для коррозионной стойкости или специфических условий эксплуатации.Чтобы убедиться, что выбранное покрытие соответствует стандартам долговечности и производительности, необходимо проконсультироваться с техническими специалистами.
Ключевые моменты объяснены:
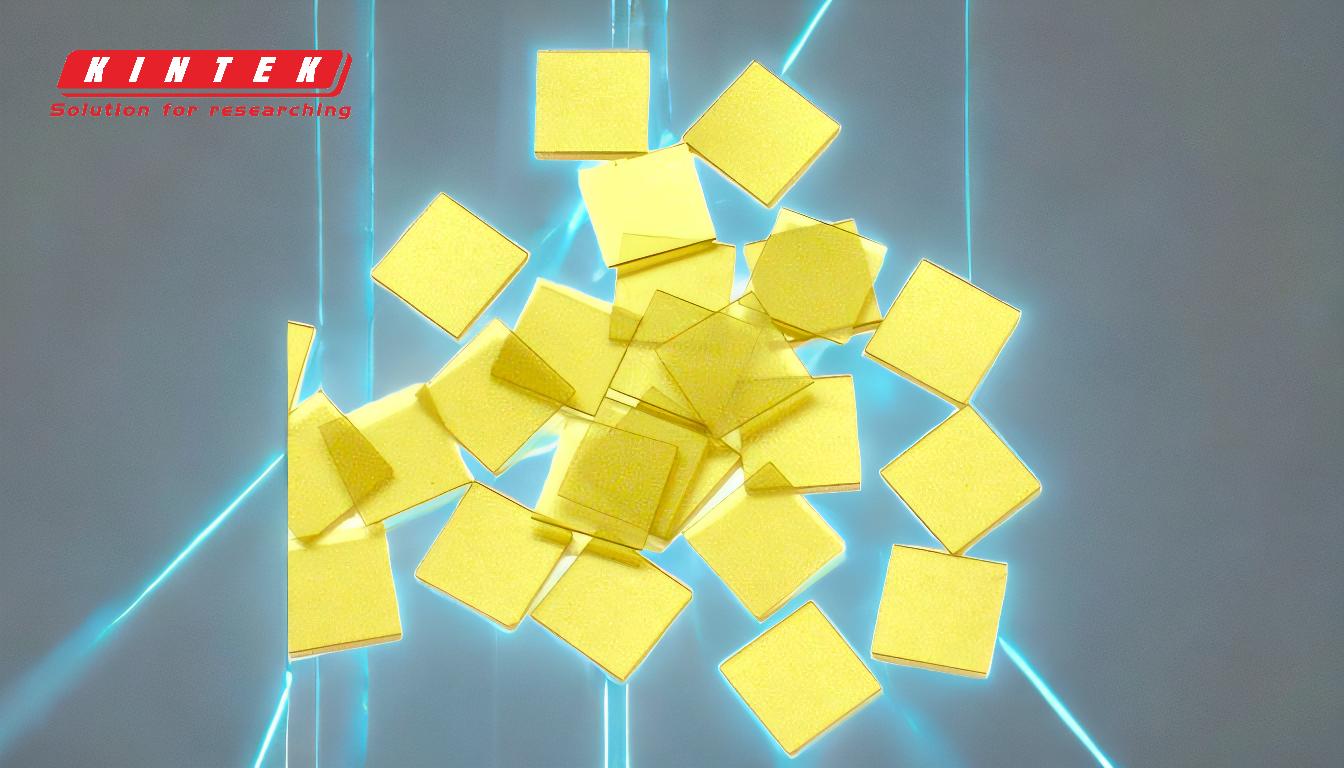
-
Процессы нанесения покрытий:CVD против PVD
-
Химическое осаждение из паровой фазы (CVD):
- Химическая реакция, в результате которой покрытие наносится на поверхность инструмента.
- Создает толстые, прочные покрытия с отличной адгезией.
- Подходит для высокотемпературных применений и инструментов, подверженных сильному износу.
- К распространенным покрытиям относятся нитрид титана (TiN) и карбид вольфрама.
-
Физическое осаждение из паровой фазы (PVD):
- Для нанесения покрытий используются физические методы, такие как напыление или испарение.
- Создает более тонкие и гладкие покрытия с высокой твердостью и износостойкостью.
- Идеально подходит для прецизионных инструментов и применений, требующих тонкой обработки поверхности.
- В качестве примера можно привести нитрид титана-алюминия (TiAlN) и алмазоподобный углерод (DLC).
-
Химическое осаждение из паровой фазы (CVD):
-
Особенности применения
-
Износостойкость:
- Покрытия из карбида вольфрама очень эффективны для инструментов, подверженных сильному износу и истиранию.
- Такие покрытия часто используются в режущих инструментах, буровых коронках и горнодобывающем оборудовании.
-
Коррозионная стойкость:
- Такие покрытия, как нитрид хрома (CrN) или DLC, идеально подходят для инструментов, используемых в коррозионных средах, например, в морской или химической промышленности.
-
Температурная стойкость:
- CVD-покрытия, такие как TiN или оксид алюминия (Al₂O₃), хорошо работают в условиях высоких температур, что делает их пригодными для обработки или металлообрабатывающих инструментов.
-
Износостойкость:
-
Совместимость с подложкой
- Материал подложки (например, сталь, титан или карбид) играет важную роль в определении наилучшего покрытия.
- Например, PVD-покрытия часто предпочтительны для инструментов из быстрорежущей стали (HSS) благодаря их способности сохранять острые кромки и снижать трение.
- CVD-покрытия лучше подходят для твердосплавных подложек, поскольку они выдерживают более высокие температуры и обеспечивают превосходную износостойкость.
-
Экологические и эксплуатационные факторы
-
Абразия и эрозия:
- Инструменты, подвергающиеся воздействию абразивных материалов или сильных ударов, выигрывают от применения твердых покрытий, таких как карбид вольфрама или покрытия на основе керамики.
-
Химическое воздействие:
- В средах, подверженных воздействию кислот, щелочей или растворителей, рекомендуется использовать коррозионно-стойкие покрытия, такие как CrN или DLC.
-
Трение и смазка:
- Покрытия с низким коэффициентом трения, такие как DLC или дисульфид молибдена (MoS₂), идеально подходят для инструментов, требующих плавной работы или уменьшения износа.
-
Абразия и эрозия:
-
Консультация технических экспертов
- Выбор оптимального покрытия предполагает баланс между множеством факторов, включая стоимость, производительность и требования к применению.
- Технические специалисты могут предоставить индивидуальные рекомендации, основанные на конструкции инструмента, условиях эксплуатации и желаемых результатах.
- Для подтверждения эффективности покрытия в реальных условиях могут потребоваться испытания и изготовление прототипов.
-
Примеры распространенных покрытий
-
Нитрид титана (TiN):
- Обеспечивает отличную износостойкость и золотистый цвет покрытия.
- Обычно используется для изготовления режущих инструментов и сверл.
-
Нитрид титана и алюминия (TiAlN):
- Обеспечивает высокотемпературную стабильность и устойчивость к окислению.
- Идеально подходит для высокоскоростной обработки.
-
Алмазоподобный углерод (DLC):
- Сочетает низкое трение с высокой твердостью и коррозионной стойкостью.
- Подходит для прецизионных инструментов и деталей в жестких условиях эксплуатации.
-
Нитрид хрома (CrN):
- Известен своей коррозионной стойкостью и долговечностью.
- Часто используется в морских и химических инструментах.
-
Нитрид титана (TiN):
В заключение следует отметить, что выбор наилучшего покрытия для металлических инструментов зависит от конкретного применения, подложки и условий окружающей среды.Понимание сильных и слабых сторон различных процессов нанесения покрытий и материалов необходимо для достижения оптимальной производительности и долговечности.Консультации с техническими экспертами гарантируют, что выбранное покрытие будет соответствовать требованиям инструмента и продлит срок его службы.
Сводная таблица:
Фактор | Основные соображения |
---|---|
Процесс нанесения покрытия | - CVD:Толстые, прочные, устойчивые к высоким температурам.PVD:Тонкие, гладкие, готовые к точной обработке. |
Потребности в применении | - Износостойкость:Карбид вольфрама.Устойчивость к коррозии:CrN или DLC. |
Материал подложки | - Сталь:Предпочтительно PVD.Карбид:Рекомендуется CVD. |
Экологические факторы | - Абразия:Твердые покрытия.Химическое воздействие:Коррозионно-стойкие покрытия. |
Распространенные покрытия | - TiN, TiAlN, DLC, CrN. |
Нужна помощь в выборе правильного покрытия для ваших металлических инструментов? Свяжитесь с нашими экспертами сегодня для получения индивидуальных решений!