Азотирование и науглероживание - оба процесса упрочнения корпуса, используемые для улучшения свойств поверхности металлов, но они имеют явные различия с точки зрения применения, преимуществ и недостатков.Хотя азотирование дает такие преимущества, как повышение твердости, износостойкости и усталостной прочности, оно также имеет ряд недостатков по сравнению с науглероживанием.К ним относятся ограничения по глубине обработки, совместимости материалов, температуре процесса и требованиям к последующей обработке.Ниже мы подробно рассмотрим основные недостатки азотирования по сравнению с науглероживанием.
Ключевые моменты:
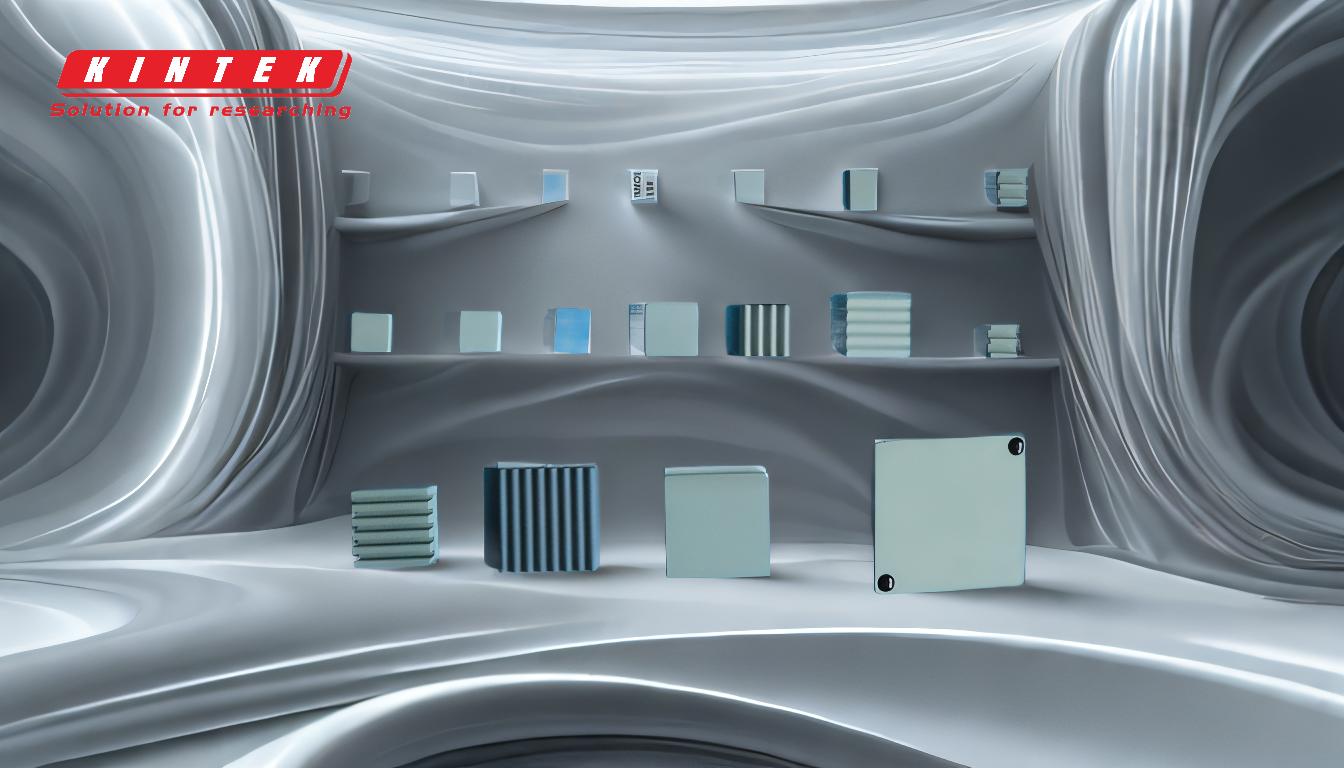
-
Ограниченная глубина гильзы
- Азотирование обычно дает меньшую глубину корпуса по сравнению с науглероживанием.
- При науглероживании глубина корпуса может составлять от 0,5 мм до 2 мм и более, в зависимости от продолжительности процесса и материала.
- Азотирование, с другой стороны, обычно приводит к глубине корпуса от 0,1 мм до 0,6 мм, что может оказаться недостаточным для задач, требующих более глубоких упрочненных слоев.
- Это ограничение делает азотирование менее подходящим для деталей, подвергающихся высокому износу или большим нагрузкам, где необходим более толстый закаленный слой.
-
Совместимость материалов
- Азотирование в первую очередь эффективно для определенных легированных сталей, например, содержащих хром, молибден и алюминий, которые образуют твердые нитриды.
- Однако науглероживание может применяться к более широкому спектру низкоуглеродистых и легированных сталей, что делает его более универсальным.
- Такая ограниченная совместимость азотирования с материалами ограничивает его применение в отраслях, где используется широкий спектр марок стали.
-
Более низкая температура процесса
- Азотирование выполняется при относительно более низких температурах (обычно от 500 до 570 °C) по сравнению с науглероживанием (обычно от 850 до 950 °C).
- Более низкая температура снижает деформацию и расход энергии, но при этом ограничивает диффузию азота в металл, что приводит к меньшей глубине корпуса.
- Более высокая температура науглероживания обеспечивает более глубокую диффузию углерода, что делает его более эффективным в условиях, требующих значительного упрочнения корпуса.
-
Требования к последующей обработке
- Азотирование не требует закалки после процесса, что снижает риск деформации.
- Однако отсутствие закалки означает, что азотированные детали могут иметь меньшую твердость сердцевины по сравнению с науглероженными деталями, которые подвергаются закалке и отпуску для получения твердой поверхности и прочной сердцевины.
- Это ограничение может повлиять на общие механические характеристики азотированных деталей, особенно в условиях высоких нагрузок.
-
Обработка поверхности и эстетика
- Азотирование может иногда приводить к менее эстетичной обработке поверхности из-за образования хрупкого \"белого слоя\" (слоя нитридов железа).
- Этот слой может потребовать дополнительной обработки, такой как шлифовка или полировка, для достижения желаемого качества поверхности.
- Науглероживание с последующей закалкой и отпуском обычно дает более гладкую и однородную поверхность, снижая необходимость в дополнительных этапах обработки.
-
Стоимость и сложность
- Процессы азотирования, такие как газовое или плазменное азотирование, могут быть более сложными и дорогостоящими по сравнению с науглероживанием.
- Необходимость точного контроля азотосодержащей атмосферы или плазменной среды повышает стоимость оборудования и эксплуатационные расходы.
- Науглероживание, будучи более известным и широко используемым процессом, часто является более экономичным и простым в реализации в условиях крупномасштабного производства.
-
Ограничения в зависимости от применения
- Азотирование менее эффективно для деталей, требующих сквозного упрочнения, или деталей, подвергающихся высоким ударным нагрузкам, поскольку оно упрочняет в основном поверхность.
- Для таких целей лучше подходит науглероживание с его большей глубиной раковины и способностью упрочнять как поверхность, так и сердцевину.
- Кроме того, азотированные детали могут иметь пониженную вязкость, что делает их менее пригодными для работы в динамичных или ударопрочных средах.
В итоге, хотя азотирование имеет такие преимущества, как уменьшение деформации и повышение износостойкости, его недостатки, такие как ограниченная глубина раковины, ограниченная совместимость материалов и более высокая стоимость, делают науглероживание более универсальным и эффективным выбором для многих промышленных применений.Решение о выборе между азотированием и науглероживанием в конечном итоге зависит от конкретных требований к детали, включая ее назначение, состав материала и желаемые механические свойства.
Сводная таблица:
Аспект | Азотирование | Науглероживание |
---|---|---|
Глубина корпуса | От 0,1 мм до 0,6 мм (тоньше) | От 0,5 мм до 2 мм и более (более глубокие) |
Совместимость материалов | Ограничена определенными легированными сталями (например, Cr, Mo, Al) | Совместимость с широким спектром низкоуглеродистых и легированных сталей |
Температура процесса | 500°C - 570°C (ниже) | 850°C - 950°C (выше) |
Постобработка | Закалка не требуется (низкая твердость сердцевины) | Закалка и отпуск (более высокая твердость сердцевины) |
Финишная обработка поверхности | Может потребовать дополнительной отделки из-за хрупкости \"белого слоя\". | Более гладкая и равномерная отделка |
Стоимость и сложность | Более высокая стоимость и сложность (например, газовое/плазменное азотирование) | Более рентабельна и проста в применении |
Области применения | Менее эффективны для применения при сильных ударах или сквозном упрочнении | Лучше подходит для применения при сильных ударах и сквозном упрочнении |
Нужна помощь в выборе правильного процесса упрочнения корпуса для вашего применения? Свяжитесь с нашими специалистами прямо сейчас!