Горячее изостатическое прессование (ГИП) — это универсальный производственный процесс, который дает значительные преимущества в улучшении свойств материала, таких как износостойкость, коррозионная стойкость и механические характеристики. Это может увеличить усталостную долговечность в 10–100 раз и достичь плотности материала, близкой к теоретическим значениям. Однако у него также есть ограничения, в том числе более низкая точность прессованных поверхностей, необходимость в дорогих порошках, высушенных распылением, и более низкая производительность по сравнению с другими методами, такими как экструзия или прессование. HIP широко используется в таких отраслях, как аэрокосмическая, автомобильная, нефтегазовая, медицинская техника, а также в технологиях хранения энергии, таких как литий-ионные батареи и топливные элементы. Процесс разделен на три основных применения: уплотнение, диффузионное соединение и продукты порошковой металлургии, выбранные в зависимости от конкретных потребностей обрабатываемых продуктов.
Объяснение ключевых моментов:
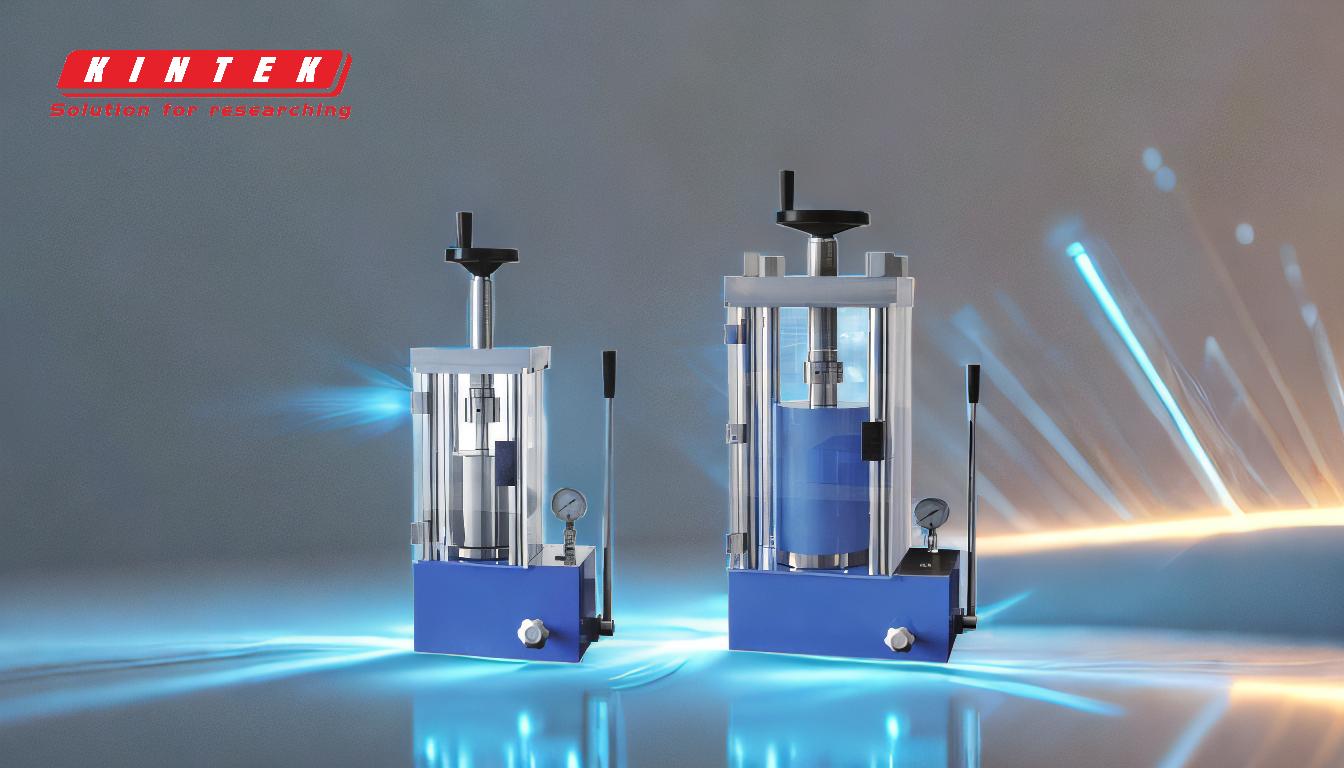
-
Преимущества горячего изостатического прессования (ГИП):
- Улучшенные свойства материала: HIP повышает износостойкость, устойчивость к коррозии и механические характеристики. Это значительно увеличивает усталостную долговечность в 10–100 раз и обеспечивает плотность материала, близкую к теоретическим значениям.
- Равномерная плотность и прочность: Этот процесс обеспечивает равномерную прочность во всех направлениях и равномерную плотность, что имеет решающее значение для высокопроизводительных компонентов.
- Гибкость формы: HIP позволяет создавать сложные формы и геометрии, что делает его пригодным для широкого спектра применений.
- Объединение этапов производства: HIP сочетает в себе процессы термообработки, закалки и старения, сокращая общее время и затраты на производство.
- Исправление дефектов: HIP эффективен для устранения дефектов в отливках и деталях, изготовленных аддитивным способом, решая такие проблемы, как пористость и плохая адгезия слоев, что приводит к созданию однородной микроструктуры.
-
Ограничения горячего изостатического прессования (HIP):
- Более низкая точность: Прессованные поверхности, прилегающие к гибкому пакету, могут иметь меньшую точность по сравнению с механическим прессованием или экструзией, часто требуя последующей механической обработки.
- Стоимость материалов: Этот процесс требует относительно дорогих порошков, высушенных распылением, для полностью автоматических прессов для сухих мешков.
- Темпы производства: HIP обычно имеет более низкую производительность по сравнению с экструзией или прессованием, что может быть ограничением для крупносерийного производства.
-
Применение горячего изостатического прессования:
- Уплотнение: HIP используется для получения материалов высокой плотности, что важно для применений, требующих высокой прочности и долговечности.
- Диффузионное соединение: Этот процесс используется для соединения разнородных материалов посредством диффузионной сварки, создавая прочные, бесшовные соединения.
- Продукция порошковой металлургии: ГИП широко используется в порошковой металлургии для производства высокопроизводительных деталей сложной формы и однородных свойств.
-
Промышленные применения:
- Аэрокосмическая и автомобильная промышленность: HIP используется для производства современной керамики и высокопроизводительных компонентов, требующих превосходных механических свойств и долговечности.
- Нефть и газ: Этот процесс применяется для производства компонентов, способных выдерживать суровые условия окружающей среды и высокое давление.
- Медицинские приборы: HIP используется для создания медицинских имплантатов и устройств с высокой биосовместимостью и механической прочностью.
- Хранение энергии: Этот процесс применяется при производстве литий-ионных батарей и топливных элементов, где решающее значение имеют равномерная плотность и высокая производительность.
-
Оптимизация процесса:
- Время, температура и давление: Эффективность HIP зависит от оптимизации этих трех ключевых переменных. Правильный контроль обеспечивает равномерную плотность и прочность конечного продукта.
- Уменьшение взаимодействия со стенками штампа: HIP уменьшает взаимодействие со стенками матрицы, повышая однородность образца и улучшая общие свойства материала.
Таким образом, горячее изостатическое прессование дает значительные преимущества в улучшении свойств материала и достижении однородной плотности и прочности, что делает его пригодным для широкого спектра высокопроизводительных применений. Однако у него также есть ограничения, такие как более низкая точность, более высокие материальные затраты и более низкие темпы производства. Этот процесс широко используется в отраслях, требующих высокопроизводительных компонентов, и оптимизируется за счет тщательного контроля времени, температуры и давления. Более подробную информацию о процессе вы можете получить, обратившись к теплый изостатический пресс тема.
Сводная таблица:
Аспект | Подробности |
---|---|
Преимущества | - Повышенная износостойкость и устойчивость к коррозии. |
- Увеличенный усталостный ресурс (10-100 раз) | |
- Равномерная плотность и прочность | |
- Гибкость формы для сложной геометрии. | |
- Объединение производственных этапов. | |
- Устранение дефектов при литье и аддитивном производстве. | |
Ограничения | - Меньшая точность прессуемых поверхностей |
- Требуются дорогие порошки, высушенные распылением. | |
- Более низкая производительность по сравнению с экструзией или прессованием. | |
Приложения | - Уплотнение, диффузионное соединение, порошковая металлургия. |
Отрасли | - Аэрокосмическая, автомобильная, нефтегазовая, медицинская техника, хранение энергии. |
Оптимизация | - Контроль времени, температуры и давления. |
- Уменьшение взаимодействия со стенками матрицы. |
Раскройте весь потенциал горячего изостатического прессования для своих задач. свяжитесь с нашими экспертами сегодня !