Цель производственных процессов на основе порошков
Оглавление
- Цель производственных процессов на основе порошков
- Процесс холодного изостатического прессования (CIP)
- Процесс горячего изостатического прессования (HIP)
- Возможность одноэтапной предварительной обработки конструкций посредством аддитивного производства из нескольких материалов
- Использование технологии селективного осаждения Kintek при изостатическом прессовании
- Потенциал аналогичного подхода для деталей, обработанных с использованием HIP
- Заключение: мост селективного осаждения порошка между новым аддитивным производством и традиционным производством
Цель большинства производственных процессов на основе порошков
Целью большинства процессов порошкового производства , таких как порошковая металлургия (ПМ), является производство плотных деталей с пористостью менее 1% без плавления исходного материала. Рыхлый порошок, используемый в этих процессах, обычно имеет низкую плотность укладки: теоретическая максимальная плотность составляет всего 64% для случайно уложенных идеально сферических частиц. Однако при использовании надлежащего распределения частиц порошка по размерам или деформируемых порошков можно достичь плотности упаковки более 90%.
Ограничения одноосного прессования
Для получения удовлетворительных результатов в процессах производства порошков решающее значение имеет применение давления. Обычно используется одноосное прессование, при котором давление прикладывается в одном направлении. Однако этот метод имеет ограничения, особенно для толстых деталей. Это обычно приводит к различиям в плотности в направлении прессования, что может повлиять на качество конечной детали.
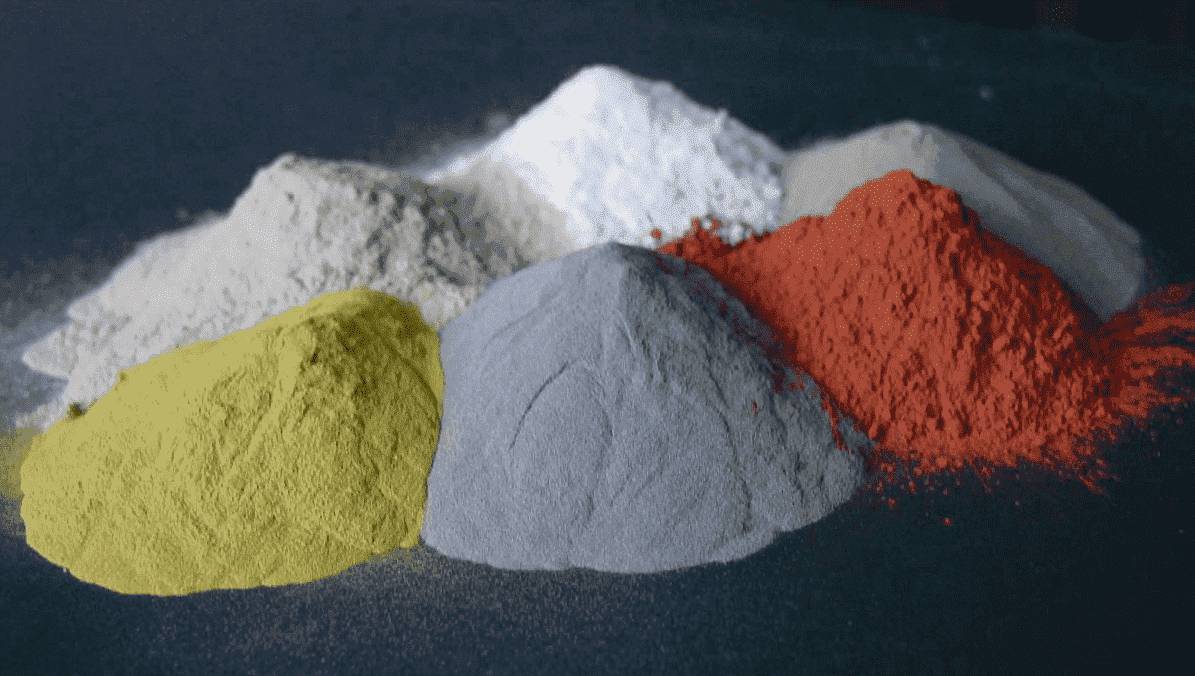
Решение: изостатическое прессование.
Чтобы преодолеть ограничения одноосного прессования, для объемных деталей часто используют изостатическое прессование . Изостатическое прессование — это метод обработки порошка, при котором для уплотнения детали используется давление жидкости. Металлические порошки помещают в гибкий контейнер, который служит формой для детали. Давление жидкости оказывается на всей внешней поверхности контейнера, заставляя его сжиматься и придавать порошку желаемую геометрию. В отличие от одноосного прессования, изостатическое прессование оказывает давление со всех сторон, что приводит к более равномерному распределению плотности.
Альтернативные процессы
Изостатическое прессование
Изостатическое прессование — это широко используемый процесс производства порошков, при котором применяется равномерное давление для консолидации порошков или устранения дефектов отливок. Его можно использовать для различных материалов, включая керамику, металлы, композиты, пластики и углерод. Процесс включает в себя помещение порошка в гибкую форму, ее герметизацию и воздействие на него давлением со всех сторон. Изостатическое прессование предлагает уникальные преимущества для керамических и огнеупорных изделий, поскольку позволяет формировать изделия с точными допусками, сокращая необходимость дорогостоящей механической обработки.
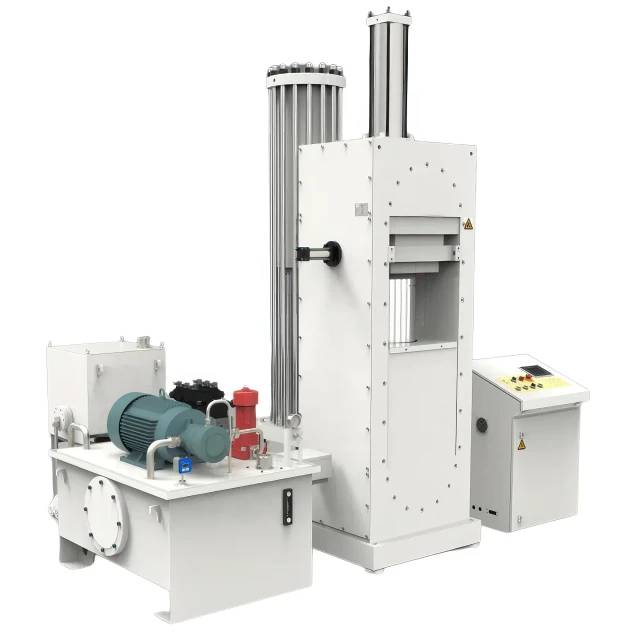
Обработка порошковых металлов
Порошковая обработка металлов – еще одна технология производства на основе порошков, позволяющая производить изделия со свойствами, превосходящими легированные материалы. В этом процессе металлические или керамические порошки вместе со связующим веществом смешиваются с образованием смеси, которой можно придать желаемую форму. Для более крупных деталей смесь заливают в формы. Этот процесс обычно используется при производстве таких продуктов, как буровые долота из поликристаллического алмазного композита (PDC) для бурения глубоких скважин, где смесь прессуется и обжигается для получения изделий почти чистой формы.
Достижения порошковой металлургии
Процессы на основе порошков, такие как компактирование порошка, горячее изостатическое прессование порошка (P-HIP), литье под давлением металла (MIM) и искровое плазменное спекание, все чаще используются для производства сетчатой формы (NS) и почти чистой формы. Формовые (ННС) компоненты высокопроизводительных сплавов. Эти процессы направлены на изготовление деталей, которые точно соответствуют требуемой конечной геометрии, сокращая затраты, время выполнения заказа и отходы материалов за счет минимизации таких этапов процесса, как механическая обработка и чистовая обработка. Порошковые технологии позволяют производить детали с эксплуатационными характеристиками, которые могут соответствовать или даже улучшаться по сравнению с традиционными производственными процессами, такими как литье. Это связано с такими факторами, как однородная микроструктура, связанная с сыпучими материалами, и достижениями в области порошковой металлургии, которые позволяют производить широкий спектр высокопроизводительных сплавов в порошковом формате.
В заключение отметим, что целью процессов производства на основе порошков является производство плотных деталей с высокой плотностью упаковки и минимальной пористостью. Изостатическое прессование — ценный метод, используемый для преодоления ограничений одноосного прессования, обеспечивающий более равномерное распределение плотности в толстых деталях. Кроме того, альтернативные процессы, такие как обработка порошковым металлом, и достижения в области порошковой металлургии расширили возможности порошкового производства, позволяя производить сложные формы и высокопроизводительные сплавы.
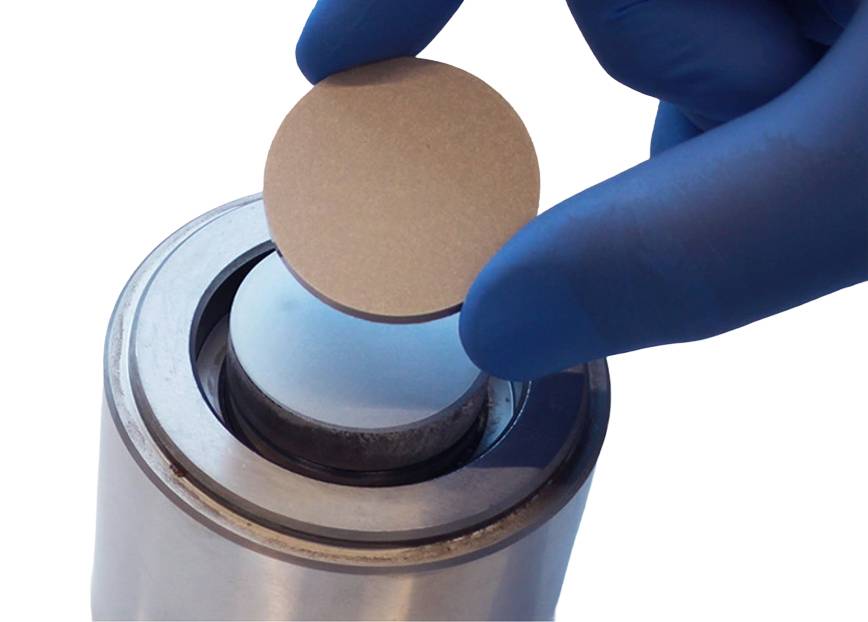
Процесс холодного изостатического прессования (CIP)
Процесс CIP
Холодное изостатическое прессование (CIP) — это метод обработки материалов, используемый для формования и уплотнения порошков в компоненты различных размеров и форм. Он предполагает помещение порошка или неспеченной детали низкой плотности в герметичный гибкий контейнер и погружение его в жидкость внутри сосуда под давлением. Прикладывается давление в несколько тысяч бар, сжимающее неспеченную прессовку настолько близко к максимальной плотности упаковки, насколько это возможно. Эта более высокая начальная плотность ускоряет консолидацию до конечной плотности в термическом цикле.
В CIP используется принцип, предложенный французским ученым Блезом Паскалем, который гласит, что изменение давления в закрытой несжимаемой жидкости передается в неизменном виде каждой части жидкости и поверхности ее контейнера. Порошковые материалы герметизируют в формовочной форме с низкой устойчивостью к деформации, например в резиновом мешке, и прикладывают давление жидкости для равномерного сжатия формованного изделия по всей его поверхности.
Прессование металлической формы — это метод прессования, аналогичный методу CIP. В этом методе порошковые материалы засыпаются в пространство, ограниченное металлической формой и нижним пуансоном. Затем они сжимаются за счет сужения расстояния между верхним и нижним пуансонами.
Преимущества высокой начальной плотности в ускорении консолидации до конечной плотности в термическом цикле
Высокая начальная плотность, достигаемая в процессе CIP, дает ряд преимуществ при консолидации порошков. Эти преимущества включают в себя:
Предсказуемое сжатие во время последующего процесса спекания. Высокое уплотнение и равномерная плотность обеспечивают предсказуемое сжатие во время процесса спекания, что приводит к стабильной и надежной конечной плотности.
Возможность обработки больших, сложных и идеальных форм: CIP позволяет обрабатывать большие и сложные формы с высокой точностью. Это экономит время и затраты во время процессов последующей обработки.
Создание деталей с большим соотношением сторон и одинаковой плотностью: CIP может производить детали с соотношением сторон более 2:1, сохраняя одинаковую плотность по всему компоненту.
Прочность сырца при транспортировке и обработке в процессе: сырой компакт, полученный посредством CIP, обладает достаточной прочностью, чтобы подвергаться транспортировке и обработке в процессе, что снижает производственные затраты.
В целом, процесс CIP обеспечивает эффективное и действенное формование и уплотнение порошков, в результате чего получаются высококачественные компоненты с желаемой плотностью. Его универсальность и способность обрабатывать различные материалы делают его ценным методом в таких отраслях, как точное производство, аэрокосмическая, оборонная и автомобильная промышленность.
Согласно отчету DataIntelo, прогнозируется, что мировой рынок оборудования для холодного изостатического прессования (CIP) будет расти со значительными среднегодовыми темпами в течение прогнозируемого периода 2020-2026 годов. Растущий спрос на продукцию CIP-обработки в таких отраслях, как точное производство, аэрокосмическая, оборонная и автомобильная промышленность, стимулирует этот рост.
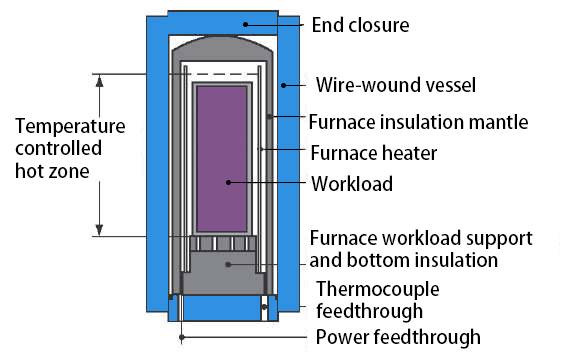
Процесс горячего изостатического прессования (HIP)
Преимущества одноосного спекания под давлением в HIP
Давление также может быть приложено во время термического цикла. При одноосном спекании под давлением обычно можно производить только пластинчатые изделия. Для более сложных деталей используется горячее изостатическое прессование (HIP). ГИП проводится в газовой атмосфере, поэтому основным требованием является то, чтобы наружная поверхность обрабатываемых деталей изначально была газонепроницаемой. Таким образом, этот процесс можно использовать для производства компонентов путем вакуумной запайки порошка детали в оболочку из мягкой стали. Равномерное приложение давления обеспечивает сохранение формы при усадке детали и оболочки. Порошки, обработанные с использованием стратегии HIP, обычно несовместимы с процессами плавления, поскольку требуют слишком высоких температур или создают неблагоприятную микроструктуру. Тем не менее, дополнительные усилия, прилагаемые для обработки этих материалов, указывают на их использование в сложных условиях, где даже низкий уровень пористости неприемлем.
Требования и результаты процесса HIP
Горячее изостатическое прессование (ГИП) — это одновременное воздействие высокой температуры и давления на металлы и другие материалы в течение определенного периода времени с целью улучшения их механических свойств. В установке HIP высокотемпературная печь заключена в резервуар под давлением. Температура, давление и время процесса точно контролируются для достижения оптимальных свойств материала. Детали нагреваются в инертном газе, обычно в аргоне, который равномерно распределяет «изостатическое» давление во всех направлениях. Это приводит к тому, что материал становится «пластичным», позволяя пустотам разрушаться под действием перепада давления. Поверхности пустот диффузионно соединяются друг с другом, эффективно устраняя дефекты, достигая плотности, близкой к теоретической, и одновременно улучшая механические свойства деталей, таких как отливки по выплавляемым моделям.
Несовместимость порошков, обработанных с использованием стратегии HIP, с процессами плавления.
Горячее изостатическое прессование (HIP) — это процесс обработки материала, который включает использование тепла и давления для улучшения физических свойств материала. Обычно это выполняется на металлах и керамике. Когда любой из этих типов материалов подвергается воздействию тепла и давления, их физические свойства изменяются. HIP — это эффективный процесс устранения дефектов в деталях, изготовленных аддитивным способом на основе порошка, позволяющий получить 100% плотный материал с улучшенными усталостными свойствами и пластичностью.
Секторы HIP завоевали свое признание после того, как достигли масштабов, сравнимых с литьем и поковкой, и стали признанным экономическим конкурентом ковки и литья в областях применения с более высокими затратами на сырье. В настоящее время существует три основных сектора HIP: нефть и газ, энергетика и аэрокосмическая промышленность. Производство компонентов PM HIP проще и короче, чем обычные традиционные металлургические процессы. Стоимость HIP по отношению к затратам на энергию и материалы снизилась на 65% за последние два десятилетия.
Введение Горячее изостатическое прессование (ГИП) — это процесс уплотнения порошков или литых и спеченных деталей в печи при высоком давлении (100-200 МПа) и температуре от 900 до 1250°С, например, для сталей и суперсплавов. Давление газа действует равномерно во всех направлениях, обеспечивая изотропные свойства и 100% уплотнение. Он дает множество преимуществ и во многих применениях стал жизнеспособной и высокопроизводительной альтернативой традиционным процессам, таким как ковка, литье и механическая обработка.
Спекание/Порошковая металлургия: технология горячего изостатического прессования (HIP)
За последние 50 лет горячее изостатическое прессование прошло путь от исследовательской лаборатории до полномасштабного регулярного производства. Будущее этой технологии выглядит светлым, поскольку растет спрос на улучшенные свойства материалов, использование порошковых материалов и желание производить детали чистой или почти чистой формы.
Источник температуры печи сопротивления внутри сосуда
Процесс HIP, первоначально известный как сварка под давлением газа, был разработан в лаборатории Мемориального института Баттел в Колумбусе, штат Огайо, в 1955 году. Первоначальным применением была диффузионная оболочка циркония в цирконий-урановые сплавы для ядерных топливных элементов. Примерно в то же время ASEA-Sweden использовала изостатическое давление для прессования первых синтетических алмазов. Горячее изостатическое прессование (ГИП) — это производственный процесс, используемый для уменьшения пористости металлов и увеличения плотности многих керамических материалов. Это улучшает механические свойства и обрабатываемость материала.
Что такое горячее изостатическое прессование (ГИП)?
Горячее изостатическое прессование (HIP), или «Hipp'ing», представляет собой одновременное воздействие на материалы тепла и высокого давления. Этот процесс идеально подходит для улучшения характеристик вашего аддитивного продукта за счет удаления пористости до 100%.
Сегодня этот процесс уже используется при совершенствовании продуктов аддитивного производства. Результатом Хиппинга является устранение внутренних пустот (т.е. пористости) и улучшение микроструктуры, что приводит к значительному улучшению механических свойств. HIP можно применять к широкому спектру сплавов, включая титан, стали, алюминий, медь и магний.
Возможность одноэтапной предварительной обработки конструкций посредством аддитивного производства из нескольких материалов
Потенциальные преимущества аддитивного производства из нескольких материалов в процессах CIP и HIP.
Аддитивное производство из нескольких материалов предлагает ряд потенциальных преимуществ как в процессах консолидации посредством изостатического прессования (CIP), так и в процессах горячего изостатического прессования (HIP). Используя селективное осаждение порошка, этот подход может преодолеть разрыв между новой технологией аддитивного производства и традиционными методами производства высококачественных компонентов. Объединение деталей с использованием отработанной технологии может помочь снизить опасения по поводу качества и надежности изделий, производимых AM.
Одним из ключевых преимуществ аддитивного производства из нескольких материалов является снижение производственных затрат. Благодаря увеличению сложности деталей, меньшему количеству этапов обработки и сокращению времени производители могут добиться экономии затрат. Это особенно полезно для производства небольших серий или прототипов, где эффективность и экономичность имеют решающее значение.
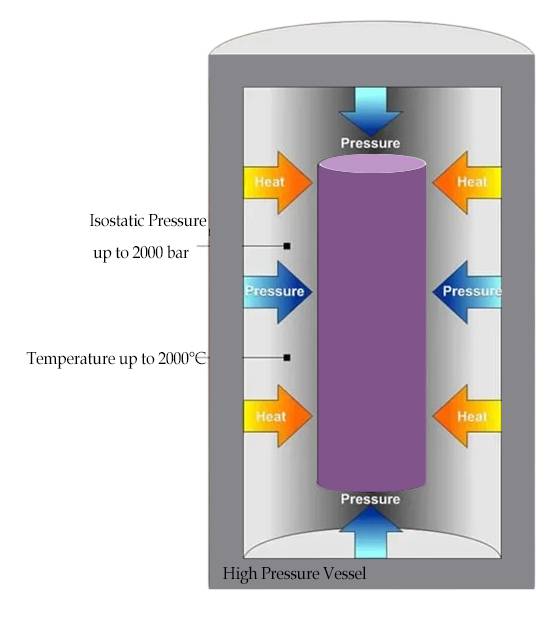
Потенциальное снижение производственных затрат за счет увеличения сложности детали, меньшего количества этапов обработки и времени.
Использование аддитивного производства из нескольких материалов может привести к снижению производственных затрат. Традиционные методы субтрактивного производства имеют геометрические ограничения, которые больше не применяются к аддитивному производству. Это означает, что можно создавать сложные формы и конструкции без значительного увеличения производственных затрат. Кроме того, возможность создавать несколько версий одного и того же продукта без изменения себестоимости производства может еще больше снизить затраты.
Еще одно существенное преимущество производства присадок из нескольких материалов.
Целью является радикальное сокращение отходов переработки. Добавляя материал шаг за шагом до тех пор, пока не будет получен желаемый объект, количество отходов минимально по сравнению с традиционными субтрактивными методами производства. Это не только снижает затраты, но и способствует более устойчивому производственному процессу.
В мире аддитивного производства металлов наблюдается заметный рост использования таких методов, как литье под давлением металла (MIM), струйная обработка связующим (BJ) и моделирование наплавлением (FDM). Эти методы предлагают уникальные преимущества с точки зрения стоимости, гибкости конструкции и свойств материала.

В аддитивном производстве металлов термическое удаление связующих является важнейшим процессом после печати. Он предполагает удаление связующих и других добавок для получения полностью плотной металлической детали. Правильное удаление связующих в деталях, изготовленных методом аддитивного производства, имеет важное значение для достижения желаемых механических свойств и точности размеров.
В процессах CIP и HIP используются конструкции из нескольких материалов. CIP предполагает использование полимерных корпусов с керамическими порошками, тогда как HIP использует сварной корпус из листовой мягкой стали с высококачественными сплавами порошковой металлургии. Эти методы предоставляют возможность одноэтапной предварительной обработки конструкций посредством аддитивного производства из нескольких материалов.
Этот подход особенно выгоден для производства небольших серий или прототипов, поскольку позволяет повысить сложность деталей за счет меньшего количества этапов обработки и меньшего времени. Используя преимущества аддитивного производства из нескольких материалов, производители могут добиться повышения эффективности и рентабельности своих производственных процессов.
Промышленная база процесса HIP быстро расширяется из-за растущего спроса на улучшенные свойства материалов и использования порошковых материалов. Кроме того, достижения в оборудовании HIP, сокращение времени обработки и улучшение экономики делают процесс HIP жизнеспособным выбором для широкого спектра материалов. Это еще больше усиливает потенциал одноэтапной предварительной обработки конструкций посредством аддитивного производства из нескольких материалов.
В заключение, аддитивное производство из нескольких материалов предлагает значительные возможности для повышения эффективности, снижения затрат и реализации сложных проектов как в процессах CIP, так и в процессах HIP. Используя преимущества этой технологии, производители могут оставаться в авангарде инноваций и отвечать требованиям современного конкурентного рынка.
Использование технологии селективного осаждения Kintek при изостатическом прессовании
Одновременное нанесение различных материалов
Изостатическое прессование — это метод уплотнения порошка в эластомерном контейнере, погруженном в жидкость под высоким давлением. Традиционно этот процесс использовался в основном для керамики и металлов. Однако недавние достижения в технологии селективного осаждения, такие как инновационный подход компании Kintek, открыли новые возможности для изостатического прессования.
Технология выборочного осаждения KinTek позволяет одновременно наносить различные материалы. Это означает, что вместо использования одного порошкового материала можно наносить слой за слоем несколько материалов. Это открывает ряд возможностей для создания сложных деталей из разных материалов с уникальными свойствами.
Создание формованной, непроницаемой для жидкостей полимерной оболочки, окружающей неуплотненный керамический порошок.
Одним из ключевых преимуществ технологии селективного осаждения KinTek при изостатическом прессовании является способность создавать формованную, непроницаемую для жидкостей полимерную оболочку, окружающую неуплотненный керамический порошок. Эта оболочка действует как барьер, предотвращая диспергирование керамического порошка в процессе изостатического прессования.
Используя избирательное осаждение для создания этой оболочки, можно добиться равномерной плотности сырца даже для деталей с большим соотношением высоты и диаметра. Это особенно важно для применений, где контроль размеров имеет решающее значение, например, в аэрокосмической или автомобильной промышленности.
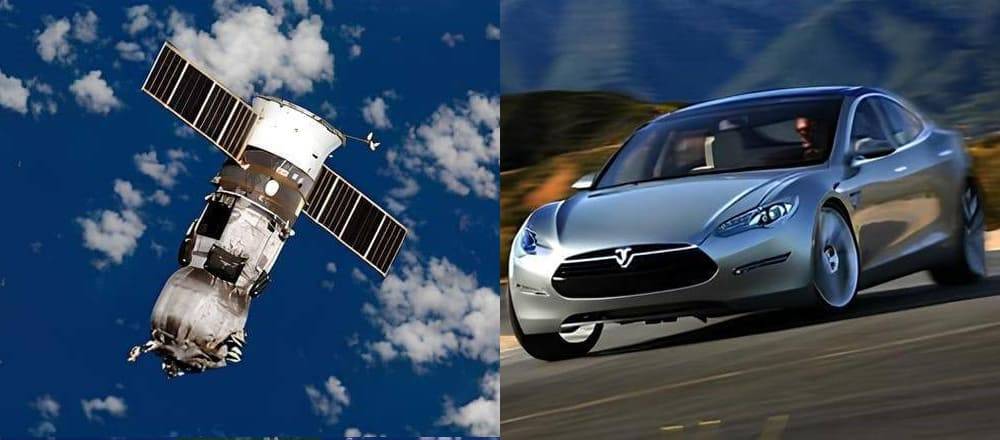
Легкая транспортировка и размещение конструкции внутри машины CIP.
Еще одним преимуществом технологии селективного осаждения является простота транспортировки и размещения конструкции внутри машины холодного изостатического прессования (CIP). Конструкция, состоящая из формованной полимерной оболочки, наполненной неуплотненным керамическим порошком, легко перемещается и размещается внутри машины CIP.
Такая простота транспортировки и размещения не только повышает эффективность, но и снижает риск повреждения конструкции в процессе погрузки. Это позволяет сделать процесс изостатического прессования более рациональным и надежным, обеспечивая стабильные результаты и высокое качество деталей.
В заключение отметим, что технология селективного осаждения предлагает потрясающие возможности для изостатического прессования. Одновременное осаждение различных материалов, создание формованной, непроницаемой для жидкости полимерной оболочки, а также легкая транспортировка и размещение конструкции внутри машины CIP – все это способствует совершенствованию этого производственного процесса. При дальнейшем развитии и совершенствовании эта технология может революционизировать способ производства сложных деталей из нескольких материалов с улучшенным контролем размеров и производительностью.
Потенциал аналогичного подхода для деталей, обработанных с использованием HIP
Совместное осаждение мягкой инструментальной стали и специального сплава ПМ с использованием системы селективного осаждения порошка.
Для деталей, которые необходимо обрабатывать с использованием HIP, можно использовать аналогичный подход. Мягкая инструментальная сталь и специальный сплав PM могут быть нанесены совместно с использованием системы селективного осаждения порошка, и потребуется консолидировать только внешнюю поверхность инструментальной стали. Поскольку сплав PM не нужно плавить, легко представить себе изготовление предварительно заполненного корпуса с трубами, которые позволят герметизировать этот корпус сваркой в вакууме, так же, как в деталях, производимых HIP, изготовленных из сварного листового металла. Остальная часть обработки HIP может пойти по традиционному маршруту.
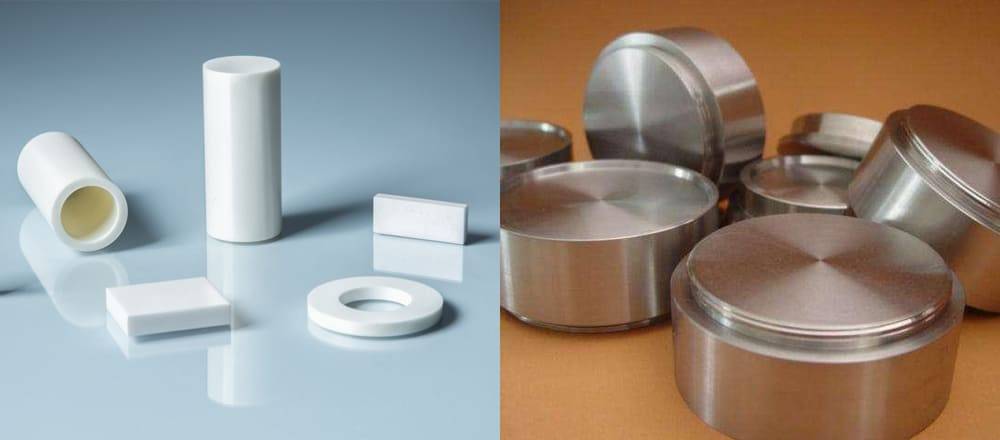
Изготовление предварительно заполненного корпуса с трубопроводами для сварки под вакуумом.
Аналогичный подход к обработке HIP можно использовать для деталей, требующих обработки HIP. Путем совместного осаждения мягкой инструментальной стали и специального сплава PM с использованием системы селективного нанесения порошка можно изготовить предварительно заполненный корпус с трубопроводами для сварки в вакууме. Это позволяет укрепить внешнюю поверхность инструментальной стали, сохраняя при этом целостность сплава PM. Оставшаяся обработка HIP может продолжаться в обычном режиме.
Традиционный маршрут остальной обработки HIP
После совместного осаждения мягкой инструментальной стали и специального сплава PM с использованием системы селективного нанесения порошка и консолидации внешней части инструментальной стали остальная часть обработки HIP может идти по традиционному маршруту. Это включает в себя использование передовых технологий охлаждения для повышения экономичности обработки и улучшения свойств конечного материала. Благодаря возможности более быстрого охлаждения с использованием аргона и внутренних систем охлаждения циклы HIP могут быть значительно сокращены, что приводит к экономии затрат и повышению качества деталей.
Использование HIP в различных отраслях промышленности оказалось весьма выгодным. HIP можно использовать для производства широкого спектра компонентов, в том числе больших и массивных металлических компонентов, близких к чистой форме, таких как детали для нефтегазовой отрасли и рабочие колеса сетчатой формы. Он также подходит для производства небольших режущих инструментов из быстрорежущей стали и мелких деталей, таких как стоматологические брекеты. С годами этот процесс превратился в высокопроизводительный, высококачественный и экономически эффективный метод производства металлических и керамических компонентов.
HIP-технология предлагает множество преимуществ, включая улучшение механических свойств, уменьшение количества отходов, минимальную механическую обработку и возможность омолаживать старые детали. Его можно применять к различным материалам, включая алюминий, сталь, нержавеющую сталь, суперсплавы, титан и керамику. Благодаря развитию оборудования HIP и сокращению времени обработки процесс HIP становится все более популярным для широкого спектра материалов и применений.
В заключение, аналогичный подход к обработке HIP можно применить к деталям, требующим обработки HIP. Путем совместного осаждения мягкой инструментальной стали и специального сплава PM с использованием системы селективного нанесения порошка можно производить предварительно заполненные корпуса с трубопроводами для сварки в вакууме. Этот подход предлагает множество преимуществ, включая улучшение качества деталей, сокращение времени обработки и экономию средств. Благодаря постоянному развитию технологии HIP потенциал использования этого подхода в различных отраслях продолжает расширяться.
Заключение: мост селективного осаждения порошка между новым аддитивным производством и традиционным производством
Потенциал селективного осаждения порошка в создании моста между новой технологией аддитивного производства и традиционным производством высококачественных компонентов.
Селективное осаждение порошка может сократить разрыв между новой технологией аддитивного производства (АП) и традиционным производством высококачественных компонентов. Этот подход использует преимущества хорошо изученных процессов обработки давлением и термоциклирования, которые уже доступны в промышленности. Использование этих признанных методов для консолидации деталей, созданных с помощью AM, может помочь снизить беспокойство отрасли по поводу изделий, производимых с помощью этой новой технологии.
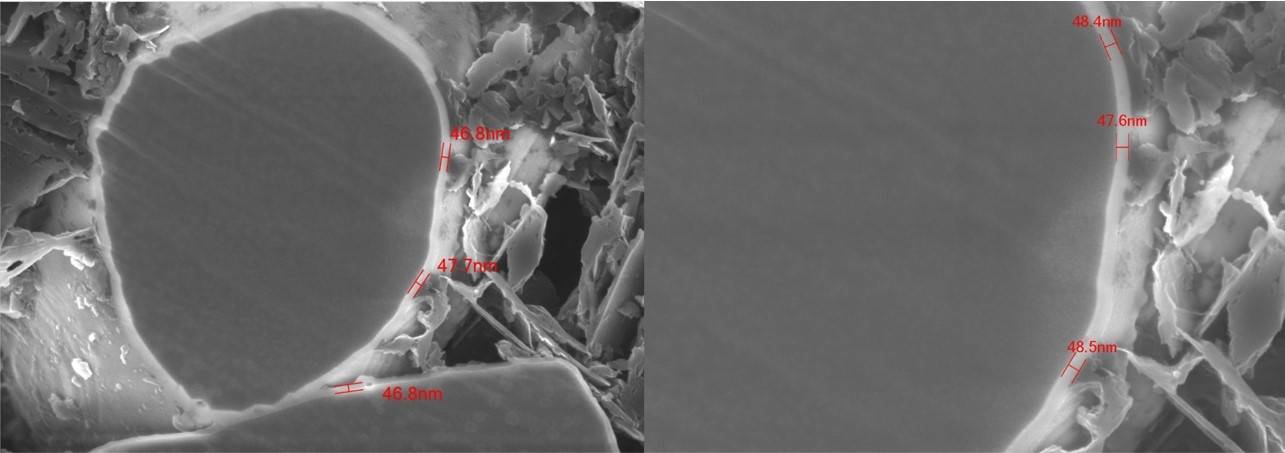
Возможность снизить беспокойство отрасли по поводу продукции, произведенной с помощью AM, благодаря этому подходу.
Когда дело доходит до аддитивного производства, одной из основных проблем в отрасли является качество и надежность конечной продукции. Традиционные методы производства совершенствовались на протяжении десятилетий, и существует определенный уровень доверия к компонентам, производимым с помощью этих процессов.
Используя селективное осаждение порошка, детали, созданные с помощью AM, могут быть сформированы с использованием новой технологии, но консолидированы с использованием давно зарекомендовавших себя методов. Это может помочь облегчить беспокойство, связанное с использованием AM для компонентов высокого класса.
В заключение, селективное осаждение порошка предлагает многообещающее решение, позволяющее преодолеть разрыв между новой технологией аддитивного производства и традиционным производством. Используя устоявшиеся процессы и методы традиционного производства, это может помочь укрепить доверие к компонентам, производимым с помощью AM.
СВЯЖИТЕСЬ С НАМИ ДЛЯ БЕСПЛАТНОЙ КОНСУЛЬТАЦИИ
Продукты и услуги KINTEK LAB SOLUTION получили признание клиентов по всему миру. Наши сотрудники будут рады помочь с любым вашим запросом. Свяжитесь с нами для бесплатной консультации и поговорите со специалистом по продукту, чтобы найти наиболее подходящее решение для ваших задач!