Электронно-лучевая обработка поверхности - это сложная технология, использующая сфокусированный электронный луч для изменения свойств поверхности материалов. Этот процесс включает в себя быстрый нагрев тонкого поверхностного слоя, что приводит к локализованным изменениям, таким как закалка, отжиг, отпуск, текстурирование и полировка. Высокая плотность мощности электронного пучка создает значительные температурные градиенты, что позволяет проводить самозакаливание без использования внешних охлаждающих жидкостей. Кроме того, технология позволяет создавать микроструктуры, такие как шиповидные образования, для улучшения сцепления и шероховатости поверхности. Электронно-лучевая обработка поверхности широко используется в различных отраслях промышленности, включая производство, электронику и пищевую промышленность, благодаря своей точности, эффективности и экологическим преимуществам.
Ключевые моменты:
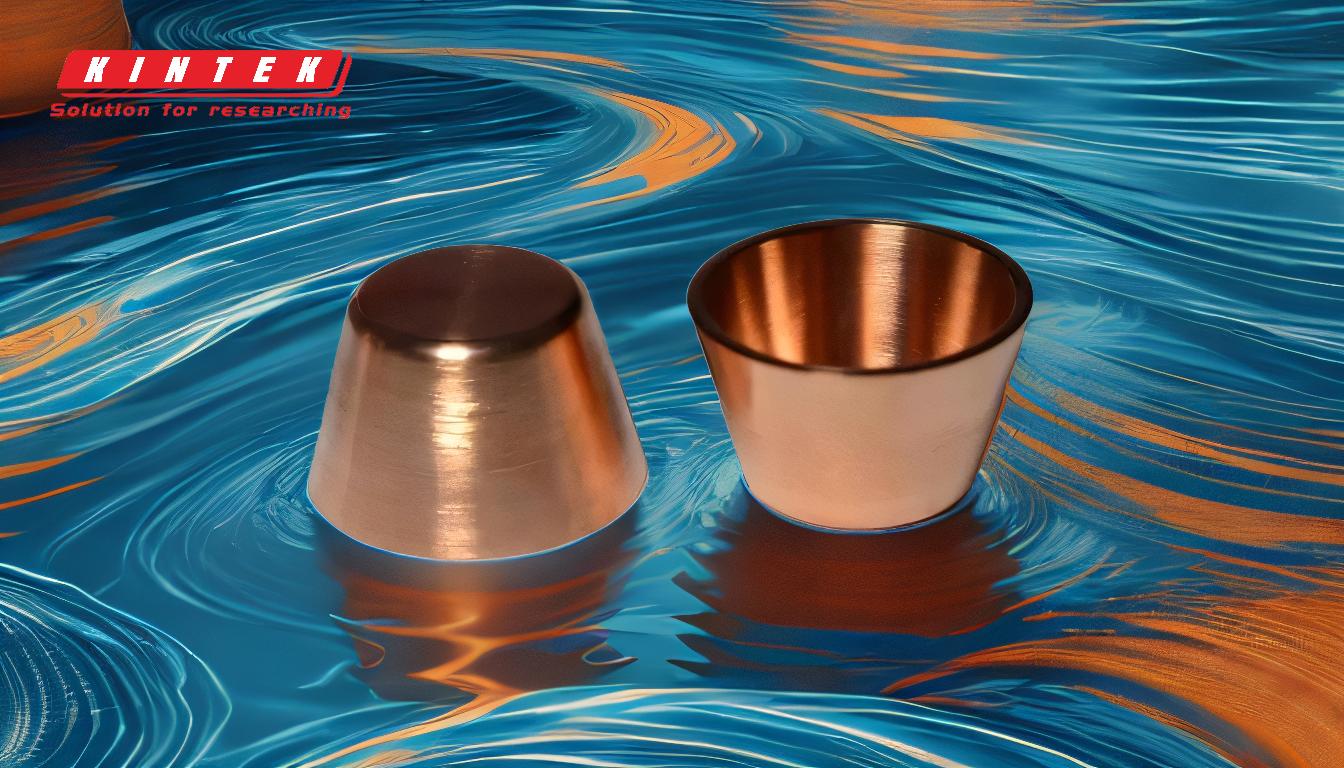
-
Принцип электронно-лучевой обработки поверхности:
- Электронный луч нагревает поверхность материала до температуры выше аустенитного диапазона.
- Теплопроводность в более холодном окружающем материале вызывает быстрое охлаждение (самозакаливание).
- Внешняя охлаждающая жидкость не требуется из-за высокой плотности мощности пучка, который создает крутые температурные градиенты.
-
Виды обработки поверхности:
- Упрочнение: Повышает твердость поверхности за счет быстрого нагрева и охлаждения.
- Отжиг: Уменьшает внутренние напряжения и повышает пластичность.
- Отпуск: Повышает вязкость за счет контролируемого нагрева и охлаждения.
- Текстурирование и полировка: Изменяет шероховатость поверхности и создает микроструктуры для улучшения сцепления.
-
Области применения электронно-лучевой обработки поверхности:
- Промышленные покрытия: Используется для получения однотонных покрытий, покрытий с низким COF, ESD и противоскользящих покрытий, а также антимикробных покрытий.
- Модификация материалов: Улучшение свойств металлов, керамики и полимеров за счет сшивания и расщепления цепей.
- Создание микроструктуры: Формирует шипообразные структуры для улучшения адгезии и шероховатости поверхности.
-
Преимущества электронно-лучевой обработки:
- Прецизионность: Нацеливается только на поверхностный слой, минимизируя воздействие на основной материал.
- Эффективность: Быстрая обработка сокращает время производства.
- Экологические преимущества: Устраняет необходимость во внешних охлаждающих жидкостях и уменьшает количество отходов.
-
Осаждение электронным лучом:
- Сфокусированный электронный луч испаряет материал из тигля.
- Пары конденсируются на подложке, образуя тонкое, равномерное покрытие.
- Усиливается ионными пучками для лучшей адгезии и более плотных покрытий.
-
Промышленное и коммерческое использование:
- Производство: Используется в термоусадочных пластиках, отверждении термореактивных композитов и улучшении полупроводников.
- Пищевая промышленность: Обеспечивает безопасность и продлевает срок хранения благодаря стерилизации.
- Оптические покрытия: Обеспечивает точную толщину и конформность покрытий для оптических поверхностей.
Используя уникальные свойства электронных пучков, эта технология предлагает универсальное и эффективное решение для обработки поверхностей в широком диапазоне применений, обеспечивая улучшение характеристик и долговечность материалов.
Сводная таблица:
Aspect | Подробности |
---|---|
Принцип | Быстрый нагрев и самозакаливание с помощью электронного луча, без использования внешних охлаждающих жидкостей. |
Виды обработки | Закалка, отжиг, отпуск, текстурирование и полировка. |
Области применения | Промышленные покрытия, модификация материалов, создание микроструктуры. |
Преимущества | Точность, эффективность и экологические преимущества. |
Применение в промышленности | Производство, пищевая промышленность, оптические покрытия. |
Преобразуйте поверхности ваших материалов с помощью электронно-лучевой технологии. свяжитесь с нами сегодня чтобы узнать больше!