Спекание - важнейший процесс в порошковой металлургии, который существенно влияет на свойства порошкового компакта, полученного методом прессования.Во время спекания компактный материал нагревается до температуры ниже температуры плавления, что приводит к различным физическим и химическим изменениям, таким как сцепление частиц, рост зерен и устранение пор.Эти изменения улучшают механические свойства материала, включая прочность, твердость и износостойкость.Однако при спекании могут также появляться дефекты, такие как усадка и крупные зерна, которые могут ослабить материал.В процессе спекания задействуются механизмы диффузии, которые формируют шейки в местах контакта частиц, что приводит к уплотнению и улучшению структурной целостности.В целом спекание превращает слабосвязанный зеленый компакт в плотный, сплошной компонент с улучшенными эксплуатационными характеристиками.
Объяснение ключевых моментов:
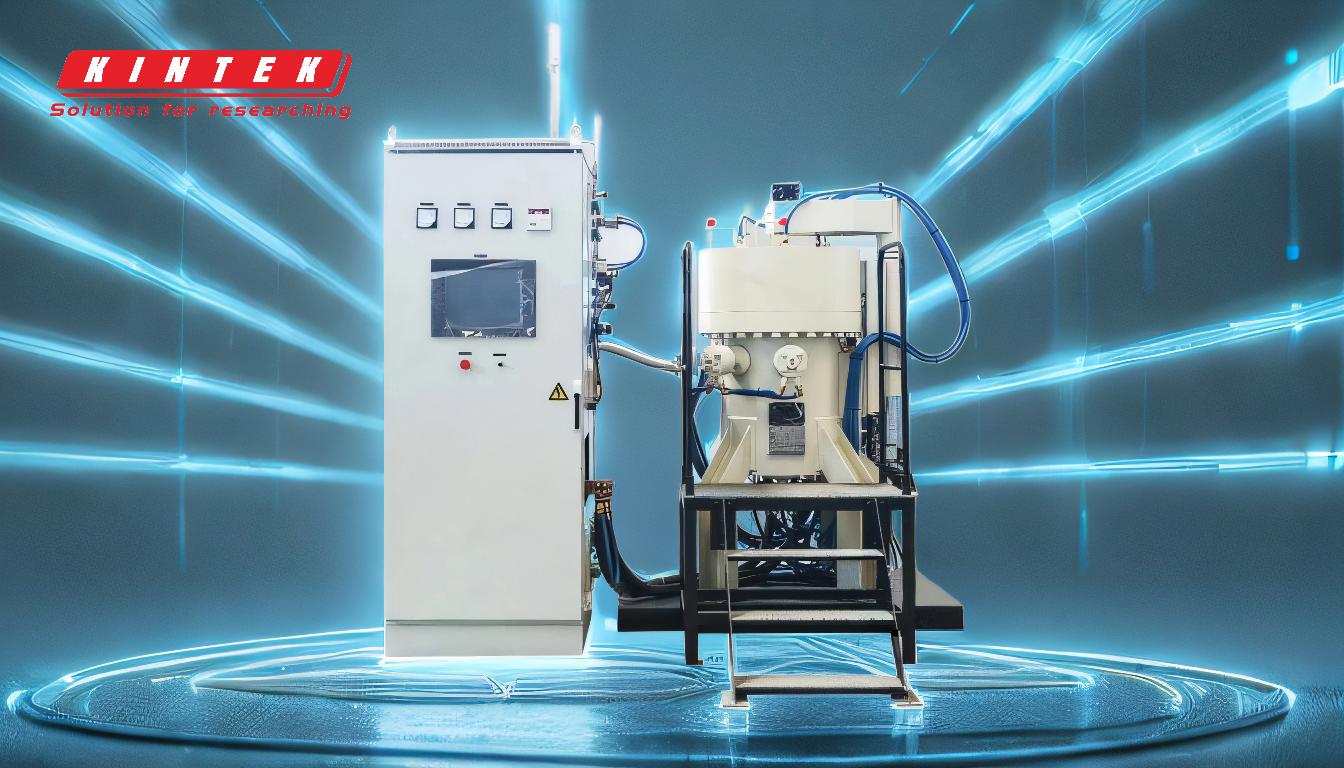
-
Металлургическое скрепление и дефекты:
- Спекание создает прочные металлургические связи между металлическими порошками и основой под воздействием высоких температур или давления.
- Такое соединение может привести к появлению дефектов, таких как сортировка, усадка и крупное зерно, которые могут ослабить механические свойства материала.
- Последствия для покупателей:Понимание этих потенциальных дефектов имеет решающее значение для выбора материалов и условий спекания, которые минимизируют неблагоприятные эффекты при максимальном повышении прочности соединения.
-
Температура и реорганизация частиц:
- Спекание происходит при температурах ниже температуры плавления материала, что делает его пригодным для материалов с высокой температурой плавления.
- При высоких температурах тонкодисперсные керамические порошки подвергаются росту зерен и перестройке частиц, что приводит к устранению пор.
- Последствия для покупателей:Выбор температуры спекания имеет решающее значение для достижения желаемой плотности и микроструктуры, которые непосредственно влияют на эксплуатационные характеристики материала.
-
Холодные сварные швы и зеленая прочность:
- После уплотнения частицы порошка удерживаются вместе холодными сварными швами, обеспечивая компактному материалу достаточную для работы прочность.
- Во время спекания под действием диффузионных процессов в этих точках контакта образуются и растут шейки, повышая структурную целостность материала.
- Последствия для покупателей:Обеспечение надлежащего уплотнения и начальной зеленой прочности имеет важное значение для успешного спекания и качества конечного продукта.
-
Улучшенные механические свойства:
- Спекание улучшает механические свойства материалов, в результате чего получаются детали с повышенной прочностью, твердостью и износостойкостью.
- Контролируемый нагрев и механизмы диффузии способствуют формированию плотной и сплошной структуры.
- Последствия для покупателей:Спеченные компоненты идеально подходят для приложений, требующих высоких механических характеристик, что делает их ценным выбором для сложных условий эксплуатации.
-
Микроструктурные изменения:
- Спекание влияет на размер зерен, размер пор, форму и распределение границ зерен в микроструктуре материала.
- Эти изменения влияют на такие свойства, как прочность и долговечность.
- Последствия для покупателей:Понимание микроструктурных изменений помогает выбрать материалы и процессы, которые оптимизируют желаемые свойства для конкретных применений.
-
Физические и химические изменения:
- Во время спекания происходит несколько изменений, включая испарение воды или органических веществ, удаление адсорбированных газов, снятие напряжения, уменьшение поверхностных оксидов, миграцию материала, рекристаллизацию и рост зерен.
- Последствия для покупателей:Эти изменения необходимо тщательно контролировать, чтобы добиться желаемых свойств материала и избежать дефектов.
-
Компактирование порошка:
- Прессование порошка включает в себя механическое уплотнение посредством холодного или горячего прессования в пресс-форме для создания экологически чистой детали.
- Этот процесс позволяет эффективно производить детали с жесткими допусками благодаря низкой усадке при сушке.
- Последствия для покупателей:Правильные методы уплотнения необходимы для достижения желаемой формы и плотности перед спеканием, что обеспечивает соответствие конечного продукта техническим требованиям.
Учитывая эти ключевые моменты, покупатели могут принимать обоснованные решения относительно материалов и процессов, используемых при спекании, обеспечивая производство высококачественных компонентов с требуемыми механическими свойствами и эксплуатационными характеристиками.
Сводная таблица:
Аспект | Ключевые детали |
---|---|
Металлургическое склеивание | Создает прочные соединения, но может привести к появлению таких дефектов, как усадка и крупное зерно. |
Температурные эффекты | Происходит ниже температуры плавления; критично для контроля плотности и микроструктуры. |
Холодные сварные швы и зеленая прочность | Обеспечивает структурную целостность благодаря диффузии и образованию шейки. |
Механические свойства | Повышает прочность, твердость и износостойкость для сложных условий эксплуатации. |
Микроструктурные изменения | Влияет на размер зерен, размер пор и распределение по границам зерен. |
Физические и химические изменения | Включает испарение, снятие напряжения, рекристаллизацию и рост зерен. |
Компактирование порошка | Обеспечивает эффективное производство деталей с жесткими допусками. |
Узнайте, как спекание может улучшить характеристики вашего материала. свяжитесь с нашими специалистами сегодня для получения индивидуальных решений!