Трехплитная пресс-форма - это специализированный тип инструмента для литья под давлением, предназначенный для отделения системы бегунков (каналов, по которым течет расплавленный пластик) от готовой детали.Такое разделение достигается за счет использования трех отдельных плит, которые последовательно открываются в процессе литья.Основным преимуществом пресс-формы с тремя плитами является возможность автоматического извлечения системы бегунков и готовой детали по отдельности, что повышает эффективность и сокращает количество отходов.Такая конструкция особенно полезна для сложных деталей или при использовании материалов, требующих точного контроля над потоком расплавленного пластика.Ниже подробно описаны ключевые моменты работы трехплитной пресс-формы.
Объяснение ключевых моментов:
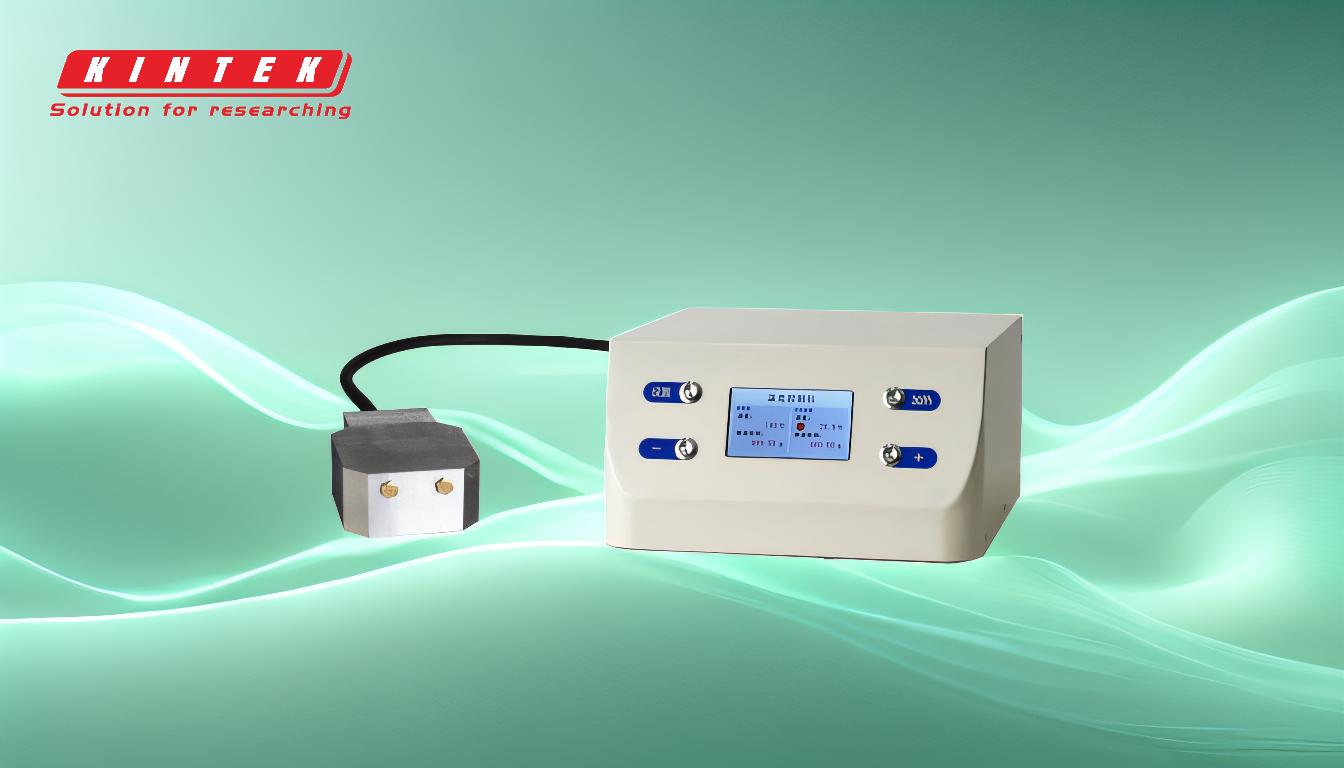
-
Структура трехпластинчатой пресс-формы:
- Трехплитная пресс-форма состоит из трех основных плит:. стационарная плита (ближайшая к инжектору), подвижная пластина подвижная пластина (соединенная с системой выброса), и средняя пластина (которая отделяет систему бегунков от детали).
- Система бегунков расположена между неподвижной и средней плитами, а полость для готовой детали - между средней и подвижной плитами.
-
Последовательность открытия пресс-формы:
-
Когда форма раскрывается, она разделяется на три отдельные стадии:
- Первая стадия:Стационарная и средняя пластины разъединяются, позволяя выбросить систему бегунов.
- Вторая ступень:Средняя и подвижная пластины отделяются, позволяя выталкивать готовую деталь.
- Такое последовательное отделение обеспечивает независимое удаление бегунковой системы и готовой детали.
-
Когда форма раскрывается, она разделяется на три отдельные стадии:
-
Конструкция бегунковой системы:
- Система обкатки в трехплитной пресс-форме обычно представляет собой холодный бегунок То есть он не нагревается в процессе формовки.
- Бегунки расположены в двух плоскостях, а затворы (точки входа в полость) расположены таким образом, чтобы расплавленный пластик мог беспрепятственно поступать в полость детали.
-
Механизм выталкивания:
- Бегущая система выбрасывается через первое отверстие между неподвижной и средней пластинами, часто с помощью выталкивающих штифтов или зачистной пластины.
- Готовая деталь выбрасывается через второе отверстие между средней и подвижной плитами, обычно с помощью выталкивающих штифтов или воздушной струи.
-
Преимущества трехпластинчатой пресс-формы:
- Автоматическое разделение бегунков:Система бегунков и готовая деталь выбрасываются отдельно, что сокращает ручные операции и повышает эффективность.
- Гибкость в размещении ворот:Затворы могут быть расположены в оптимальных местах детали, что позволяет лучше контролировать поток пластика и уменьшает видимые следы от затворов.
- Пригодность для сложных деталей:Конструкция идеально подходит для деталей со сложной геометрией или множеством полостей.
-
Области применения:
- Трехплитные пресс-формы обычно используются для производства небольших сложных деталей, таких как электронные компоненты, медицинские приборы и потребительские товары.
- Они также предпочтительны для материалов, требующих точного контроля над процессом впрыска, таких как высокоэффективные пластмассы.
-
Проблемы:
- Сложность:Конструкция и эксплуатация трехплитной пресс-формы сложнее, чем двухплитной, требует точного выравнивания и обслуживания.
- Стоимость:Дополнительная плита и механизмы выталкивания увеличивают стоимость пресс-формы.
- Время цикла:Последовательный процесс раскрытия и выталкивания может несколько увеличить общее время цикла по сравнению с более простыми конструкциями пресс-форм.
Понимая эти ключевые моменты, покупатели оборудования и расходных материалов могут лучше оценить, является ли трехплитная пресс-форма правильным выбором для их конкретных производственных нужд, сбалансировав преимущества автоматизации и точности с более высокой стоимостью и сложностью.
Сводная таблица:
Аспект | Подробности |
---|---|
Структура | Три пластины: стационарная, средняя и подвижная.Система бегунков и полость для деталей разделены. |
Последовательность открытия | Два этапа: сначала выталкивается бегунок, затем деталь. |
Система бегунов | Конструкция холодного бегуна с затворами в двух плоскостях для оптимального потока пластика. |
Механизм выталкивания | Бегунок выталкивается через первое отверстие; деталь выталкивается через второе отверстие. |
Преимущества | Автоматическое разделение бегунков, гибкое размещение затворов, идеальное решение для сложных деталей. |
Области применения | Мелкие детали сложной формы (электроника, медицинские приборы, потребительские товары). |
Проблемы | Повышенная сложность, увеличение стоимости, незначительное увеличение времени цикла. |
Готовы оптимизировать свой процесс литья под давлением? Свяжитесь с нами сегодня чтобы узнать, как трехплитная пресс-форма может удовлетворить ваши производственные потребности!